制約理論を初心者向けにわかりやすく解説【業務改善手順の5ステップ】
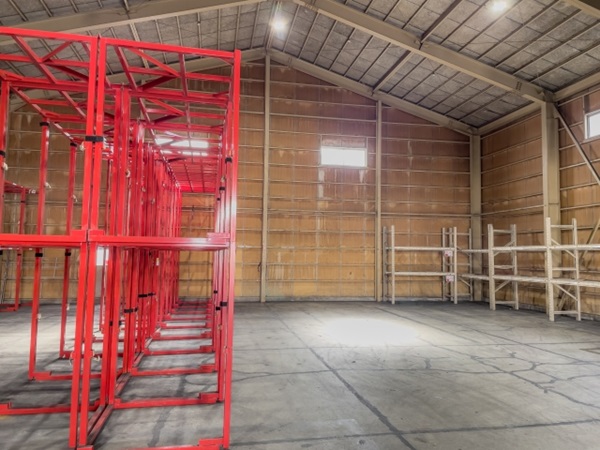
制約理論は、製造業の現場で活用されることの多い改善手法です。生産性の低いボトルネックや、パフォーマンスを妨げている制約を洗い出して、集中して改善すれば、全体最適が実現するという理論に基づいています。製造業において制約理論の業務改善は、確かに大きな効果が期待できます。
ボトルネックや制約を洗い出して徹底的に改善できれば、最小の努力で最大の成果を得られる可能性が高いからです。今回は、制約理論を初心者向けにわかりやすく解説します。制約理論に基づいた業務改善手順の5ステップも紹介するので、ご参考にしてみてください。
コンテンツ
制約理論とは制約にフォーカスして改善することで全体最適の実現を目指すこと
制約理論とは、制約の最大パフォーマンスを引き出すことで、全体最適の実現を目指すことです。英語で『Theory of Constraints』と表現されTOCとも呼ばれています。
制約理論は1984年に出版された『ザ・ゴール』の著者であり、物理学者でもあるエリヤフ・ゴールドラット博士が開発した全体最適のマネジメント理論であり、TOCは生産現場の改善手法としてだけでなく、SCM(サプライチェーン・マネジメント)、プロジェクト管理、流通、小売、IT、保守など、さまざまな領域で活用されています。
ではなぜ、制約の最大パフォーマンスを引き出し、改善活動を行えば、全体最適の実現を目指せるのでしょうか。理由は制約理論が「どんなシステムであれ、常に、ごく少数(たぶん唯一)の要素または因子によって、そのパフォーマンスが制限されている」という仮定から出発しているからです。
制約理論では、「制約」と「非制約」の概念を大切にしています。
わかりやすくいうと、「制約=大きな問題で改善すれば成果も高いもの」、「非制約=小さな問題(あるいは問題ではない)で改善しても成果が低いもの」ともいえます。製造業において改善活動を行うとき、最初に取り組むのは問題や課題の洗い出しです。
制約理論でも同じ順序を辿りますが、特徴的なのは全ての問題や課題を改善しようとするのではなく、根本原因となっている「制約」に集中する点です。
制約に集中していない改善を行うと、小さな問題や課題は解消できるかもしれませんが、全体最適の観点からすると、ほとんど意味のないことがあります。
制約理論に基づかない改善活動はコストが高く、成果に対して十分なリターンを得られにくいことがデメリットです。
制約理論のフレームワーク
制約理論の代表的なフレームワークには、「5段階集中プロセス」と「思考プロセス」があります。どちらも制約理論の改善活動を行うときに、役立つフレームワークです。
「5段階集中プロセス」は、製造業の工程を改善するための具体的なプロセスであり、全ての課題に対策を打つのではなく、その課題の根本原因となっているごく少数の制約条件に対策を打つことで、最小の手間と時間で最大の改善効果を得られるマネジメント手法です。
「思考プロセス」も制約理論のフレームワークですが、5段階集中プロセスとの大きな違いは、制約の特定により特化している点です。思考プロセスのフレームワークでは、根本問題となっている制約を洗い出し、克服するための改善方法を導き出します。
そのため思考プロセスでは、全てを変える必要はなく、変えるべきものをどのように変えていくかが重要となります。今回は、主に5段階集中プロセスを活用した、制約理論の改善活動の進め方を紹介します。
制約理論に基づいた業務改善手順の5ステップ
制約理論のフレームワークの中で、最も活用されているのが「5段階集中プロセス」です。PDCAサイクルのように、5つの手順を繰り返しながら、改善活動を行う手法です。制約理論に基づいた業務改善手順の5ステップを紹介します。
制約を見つける
まずは、業務全体を俯瞰的な視点で確認し、制約を見つけます。洗い出すポイントは、特に業務の流れを遅くしている、ボトルネックに着目することです。
制約理論で制約を最重要している理由は、非制約を改善しても、全体のパフォーマンス向上に大きな影響は及ばないからです。明らかに業務のパフォーマンスを妨げているもの(=制約)がないか、慎重に洗い出してみましょう。
制約を徹底活用する方法を考える
制約理論では、見つけ出した制約を潰すのではなく、徹底活用する方法を探します。このステップは、制約理論の中でも重要な考え方です。例えば、制約が人員不足による業務進行の遅れであったとします。
この場合は制約を徹底活用するために、人員配置を見直したり、ITツールの導入で自動化したりする試みが有効です。制約となっている箇所を、どうすれば徹底活用できるか考えましょう。
業務プロセスを制約に合わせる
制約を徹底活用する方法を考え、準備を整えたら、その他の業務プロセスの調整を行います。制約理論では、制約にその他の業務プロセスを合わせる、従属させる考え方を採用しています。
業務プロセスを制約の処理能力に合わせることで、結果的に業務全体から無駄を省いた効率的なプロセスに最適化できる仕組みです。
制約の能力を高める
制約にその他の業務プロセスを従属させたあとは、制約自体の能力を高めていきます。制約をどうすればより効率化できるか、改善活動を実施していきましょう。
制約にその他の業務プロセスを従属させた状態で能力を高めれば、全体の能力も高まります。ボトルネック(=制約)のネック部分を、広げていくイメージです。
新たな制約を探す
制約の能力が高まったら、ステップの1に戻り、新たな制約を探します。制約は、常に変化し流動するものです。制約理論に基づいて、5段階のステップを繰り返しながら改善活動を行えば、継続的な成長が実現できます。
制約理論は最小の努力で最大の成果を得られる改善手法(まとめ)
制約理論は、改善活動を最大限に効率化できる手法です。最初のステップである「制約の特定」さえ適切にできれば、最小の努力で最大の成果を得られます。今回は、制約理論の代表的なフレームワークとして、「5段階集中プロセス」をご紹介しました。
5段階集中プロセスを活用すれば、一つの大きな制約に集中して改善活動に取り組めます。結果、スピーディーに改善活動が進み、業務全体も最適化します。
PDCAサイクルを回すように最初の手順に戻り、繰り返し制約を見つけて改善していくため、継続的に成長し続けられることが大きなメリットです。製造業の改善活動に取り組むときは、ぜひ制約理論とフレームワークを活用してみてくださいね。
今日のポイント
- 制約理論とは制約の最大パフォーマンスを引き出し、改善することで全体最適の実現を目指すこと
- 制約理論の代表的なフレームワークには「5段階集中プロセス」と「思考プロセス」がある
- 制約理論に基づいた業務改善手順の5ステップは制約を見つける→制約を徹底活用する方法を考える→業務プロセスを制約に合わせる→制約の能力を高める→新たな制約を探す
製造業のDXはあおい技研
株式会社あおい技研は、製造業に特化した業務改善コンサルティングを提供し、製造現場のDX推進をサポートします。80以上の製造現場での診断や改善の経験を活かし、お客様に合ったDX戦略を提案します。
データ分析、業務効率化システムの開発、現場のデジタル化などを通じて、お客様の業務改善と生産性向上を支援します。
製造業のDXについては、あおい技研にご相談ください。
関連記事
-
業務の見直しをする方法5つと注意点【改善ネタ・アイデア出しの参考になる】
2024年7月9日
-
業務効率化の成功事例7つを参考にアイデア出しをしよう!業務の無駄の見つけ方も解説
2023年12月12日
-
製造業の利益率の目安とは?計算方法5つや向上させる方法を解説!
2024年10月3日
-
労働生産性の計算式2つを初心者向けにわかりやすく解説|製造業が低い理由と向上させる方法
2024年8月15日
-
工程能力とは?基礎や工程能力指数の計算式を5つのステップでご解説!
2022年6月15日
-
スマートファクトリーとは?簡単に5つの事例を交えながら紹介|ロードマップも解説
2023年7月3日
-
製造業のIT遅れ、原因は?推進ポイントも紹介
2025年1月29日
-
業務効率化の事例15選 【製造業の改善ネタ探しに役立つ】
2023年1月25日
-
工場の動線を安全に確保するための手順を3ステップで紹介!レイアウト図の書き方も
2023年8月4日
カテゴリー
- IT化
- QCD
- QCサークル
- コスト削減
- コンサルタント
- スマートファクトリー
- ボトルネック工程
- 中小企業
- 労働生産性
- 合理化
- 品質担保
- 品質管理
- 在庫管理
- 工場IoT
- 工場効率化
- 工程管理
- 工程管理システム
- 投入資源
- 業務効率
- 業務改善
- 生産ライン
- 生産性向上
- 生産管理
- 生産管理システム
- 経費削減
- 製造業
- 製造業 DX
- 製造業IoT
- 見える化
- 設備管理
新着コラム
-
2025年7月30日
工場の労働環境を改善するための具体策とは?改善のステップや事例もご紹介
-
2025年7月30日
工場の暑さ対策を徹底解説!2025年義務化対応と効果的な対策とは?
-
2025年7月30日
工場の5S活動とは?生産性と安全性を高める改善の進め方
-
2025年6月30日
産業用ロボットとは?サービスロボットとの違いや種類、導入するメリットを解説
-
2025年6月30日
工場の省人化に取り組むメリットを解説!具体的なステップと事例をご紹介
-
2025年6月30日
【産業用ロボット】主要メーカーの市場シェアはどれぐらい?市場規模などわかりやすく解説
-
2025年5月28日
事例から学ぶ工場の安全対策!製造業の労災件数も紹介
-
2025年5月28日
ベンダーコントロールとは?定義やToDoを解説
-
2025年5月28日
外部コンサルタントとは?内部との違いやメリット・デメリット
-
2025年4月25日
勘と経験に頼らないモノづくりとは?製造業10社のデータ活用事例を紹介