ボトルネック工程の解消ステップ5つ|見つけ方と注意点も
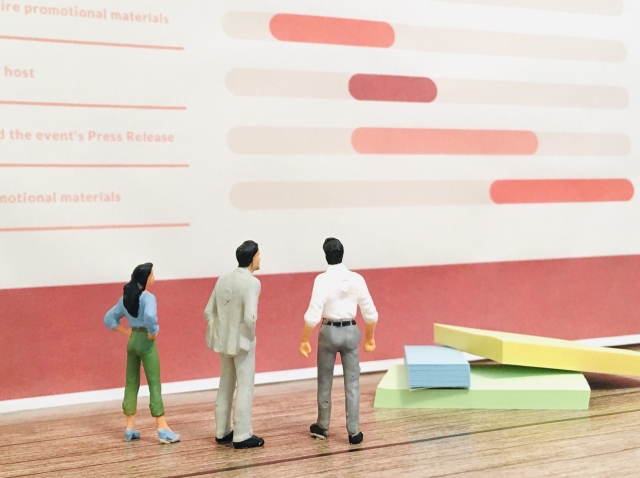
ボトルネック工程とは、生産工程の中で最も生産能力の低い工程のことを指します。
ボトルネックの直訳は「瓶の首」です。
どんなに大きな瓶でも首の部分が狭いと、一定時間に出てくる液体の量が少なくなることから、生産工程で障害や問題となる部分の用語として使われています。
ボトルネック工程が製造ラインに与える影響は大きく、全体の生産量や品質、納期遵守を左右します。まずは、ボトルネック工程がどこにあるのかを見つけて、解消できるように取り組むことが必要です。
今回は、ボトルネック工程の解消ステップ5つ(TOC手法)をご紹介します。
ボトルネック工程が製造ラインに与える影響や見つけ方、注意点もご解説するので、ご参考にしてください。
コンテンツ
ボトルネック工程が製造ラインに与える影響
実は、生産工程において、他の工程の生産能力がどんなに高くても、ボトルネック工程の生産能力以上に、全体の生産量は高められないという特性があります。
例えば、同一製造ラインに以下のような5つの工程があったとします。
A工程 B工程 C工程 D工程 E工程
1時間あたりの各工程における生産量を以下のようにすると、ボトルネック工程は生産量が最も少ない「C工程」になります。
A工程 B工程 C工程 D工程 E工程
16個 14個 10個 12個 14個
ポイントとなるのは、他の工程の生産量がどんなに多くても、ボトルネック工程(C工程)では1時間に10個の生産が限度ということです。
他の工程の生産能力に関係なく、1時間に10個以上の生産はできません。
つまり、製造ライン全体の生産量を上げるためには、ボトルネック工程の底上げをする必要があります。
また、製造ラインへの影響として、ボトルネック工程の前の工程では必ず仕掛品が発生し、増加してしまうというものがあります。
ボトルネック工程は、製造ラインに対して全体の生産量を制約し、仕掛品を増やし続けるという悪影響を及ぼします。
ボトルネック工程の見つけ方
まずは、ボトルネック工程がどこに潜んでいるのか把握することからです。ボトルネック工程の見つけ方と、着目するべき工程をご紹介します。
作業が停滞している工程
最も分かりやすい見つけ方です。生産量が圧倒的に低い工程や、前に仕掛品が積み上がっている工程に着目してみましょう。
稼働率が高い工程
稼働率が高いということは、余裕がなく、他の工程のスピードに追い付けていない証です。ボトルネック工程である可能性が高いといえます。
問題やトラブルがよく発生している工程
問題やトラブルがよく発生する工程は、何らかのムリが生じている可能性が高いです。
ムリによって生じた問題やトラブルが原因となり、さらに生産能力が低くなり、ボトルネック工程となっているケースもあります。
ボトルネック工程を見つける手段として有効なものに、「ピッチダイアグラム」の活用があります。
ピッチダイアグラムとは、各工程の作業時間を棒グラフにまとめたもので、作業時間の観点からボトルネックを見つけたり、判断したりするのに役立ちます。
製造ラインの改善案も分かるようになる、メリットがあります。
ボトルネック工程の解消ステップ5つ【TOC手法】
ボトルネック工程を解消するには、TOC手法の5つのステップが参考になります。
TOC手法とは、イスラエルの物理学者エリヤフ・ゴールドラット氏が提唱した、ボトルネックの解決を目指す手法のことです。
5つのステップに従いながら、ボトルネック工程を集中的に管理し、解決を目指します。
ここからは、「車の製造ラインにおけるボトルネック工程の解消」を例にしながら、ボトルネック工程の解消ステップ5つ【TOC手法】について詳しくご紹介します。
1.ボトルネック工程を見つける
まずは、ボトルネック工程を見つけます。
- 作業が停滞している工程
- 稼働率が高い工程
- 作業時間が長い工程
- 問題やトラブルがよく発生している工程
などに潜んでいる可能性が高いため、これらの工程に着目して探してみましょう。
- 例
稼働率が最も高い工程を探してみると、塗装工程が該当した。稼働率は高いのに前の工程には仕掛品が積み上がっており、塗装工程がボトルネック工程であることが判明した。
2.ボトルネック工程をフル稼働させる
ボトルネック工程が見つかったら、フル稼働させるように努めます。
ボトルネック工程が能力を十分に発揮できていない場合は、その原因を突き止めて改善し、稼働率を100%に限りなく近づけていきましょう。
100%に近づけるためのポイントは、ボトルネック工程に必要最小限の仕掛品を置き、稼働停止を避けることです。
- 例
塗装工程の稼働率が高い原因は、塗装を1色ずつ行っていたことだった。1台ずつ塗装を完成させていくのではなく、5〜10台を1色ずつ塗装していき、まとめて次の工程に引き渡していた。フル稼働させるために、塗装工程の前には必要最小限の仕掛品を置いておくようにし、塗装の効率化を進めるにはどうしたらいいか考えた。
3.ボトルネック工程に他の工程作業を合わせる
ボトルネック工程は、製造ライン全体の生産量を定め、他の工程を制約してしまう特性があります。
そのため、一旦ボトルネック工程が処理できる量だけ資材を投入し、ボトルネック以外の工程は稼働させないという試みも必要です。
他の工程全てをボトルネック工程に従わせ、過剰な仕掛品が発生しないようにします。
ボトルネック工程の生産能力向上を目指す前に、まずは全工程の能力を同期させて、バランスを取っていくイメージです。
- 例
塗装工程では1時間の生産量が60台であったため、同一製造ラインの他の工程の稼働率を調整し、生産量を同じく60台前後になるようにした。過剰な仕掛品の発生はなくなった。
4.ボトルネック工程の能力を高める
ボトルネック工程の原因を突き止めて改善し、能力を最大限に引き出したところで、新たな資材や人員投入で、能力をさらに高められないか考えてみます。
また、他の工程との助け合いを行いながら、ボトルネック工程の作業負担を軽減できないか取り組んでみることも有効です。
- 例
塗装工程の能力を高めるために、新しいロボットを導入した。異なる色でも1台ずつ同時に塗装できるようになり、生産能力が向上した(1時間の生産量アップ)。
5.ボトルネック工程が解消・改善されたら最初のステップに戻る
ボトルネック工程が解消・改善されたら、最初に戻り1〜5のステップを繰り返します。
ボトルネック工程は移動したり変化したりするため、最初に戻り解消と改善を繰り返していく必要があるからです。
このとき、解消したボトルネック工程はどのように改善されたのかを振り返り判断しながら、再び進めていくことが大切です。
- 例
塗装工程のボトルネック工程は、解消された。最初のステップに戻り、ボトルネック工程が現在はどこに潜んでいるのかを確認し、同じ手順で解消と改善を繰り返していく。
ボトルネック工程を解消するときの注意点
ボトルネック工程を解消するときの重要な注意点が、1つだけあります。それは、「ボトルネック工程は完全にはなくならない」ということです。
詳しくご解説します。
ボトルネック工程は完全にはなくならない
実は、ボトルネック工程が完全になくなることはありません。
なぜなら、一つのボトルネック工程が解消・改善されても、全ての工程が均一に問題なく稼働し続けるということはありえないからです。
別の工程が新たに、ボトルネック工程となって生じてきます。
ボトルネック工程は完全に解消し、なくすことを目指すのではなく、常にあるものとしてその都度、解消や改善を行っていくという認識を持つようにしましょう。
ボトルネック工程はTOC手法の5つのステップで解消できる(まとめ)
ボトルネック工程は、製造ラインに大きな影響を与え、全体の生産量や品質、納期遵守を左右します。
生産現場全体の生産量を上げるためには、ボトルネック工程を見つけて解消・改善に取り組むことが必要です。ボトルネック工程の見つけ方は、作業が停滞している工程や稼働率が高い工程に着目してみることです。
ボトルネック工程を解消するには、TCC手法の5つのステップを参考にします。
段階を踏みながら、ボトルネック工程の能力を最大限に引き出したり、他の工程に合わせてもらったりし、全体のバランス調整を行いながら解消と改善を目指す手法です。
ただし、注意点としてボトルネック工程が完全になくなることはありません。
ボトルネック工程は絶えず移動・変化し、発生するものなため、その都度TOC手法などを参考にして解消や改善を行い続ける必要があります。
今日のポイント
- ボトルネック工程とは、生産工程の中で最も生産能力の低い工程のこと
- ボトルネック工程は、製造ラインに対して全体の生産量を制約し、仕掛品を増やし続けるという影響を与える
- ボトルネック工程はTOC手法の5つのステップで解消できる
- ボトルネック工程は完全にはなくならない(都度、解消と改善を目指すこと)
製造業のDXはあおい技研
株式会社あおい技研は、製造業に特化した業務改善コンサルティングを提供し、製造現場のDX推進をサポートします。80以上の製造現場での診断や改善の経験を活かし、お客様に合ったDX戦略を提案します。
データ分析、業務効率化システムの開発、現場のデジタル化などを通じて、お客様の業務改善と生産性向上を支援します。
製造業のDXについては、あおい技研にご相談ください。
関連記事
-
製造業の仕事はAI導入でなくなる?今後の動きと活用事例6選
2024年3月4日
-
工場の省人化に取り組むメリットを解説!具体的なステップと事例をご紹介
2025年6月30日
-
生産管理とは?7つの業務内容と向いている人の特徴
2022年3月3日
-
工場にIoTを導入してスマートファクトリー化すると解決できる課題5つ
2022年4月28日
-
業務管理の基本6つを初心者向けに解説!理由や進め方・役立つツールも紹介
2022年8月30日
-
設備管理が製造業において重要な理由3つ|工場での仕事内容や保全管理の基本
2022年7月15日
-
生産性を上げる方法を2つの視点で解説|製造業での取り組み事例も紹介
2024年5月7日
-
データ分析で製造業の何が変わる?つまずくポイントも解説
2025年3月24日
-
工場のヒヤリハットの原因4つ!対策と改善案のネタ切れに役立つ事例も紹介
2024年4月5日
カテゴリー
- IT化
- QCD
- QCサークル
- コスト削減
- コンサルタント
- スマートファクトリー
- ボトルネック工程
- 中小企業
- 労働生産性
- 合理化
- 品質担保
- 品質管理
- 在庫管理
- 工場IoT
- 工場効率化
- 工程管理
- 工程管理システム
- 投入資源
- 業務効率
- 業務改善
- 生産ライン
- 生産性向上
- 生産管理
- 生産管理システム
- 経費削減
- 製造業
- 製造業 DX
- 製造業IoT
- 見える化
- 設備管理
新着コラム
-
2025年7月30日
工場の労働環境を改善するための具体策とは?改善のステップや事例もご紹介
-
2025年7月30日
工場の暑さ対策を徹底解説!2025年義務化対応と効果的な対策とは?
-
2025年7月30日
工場の5S活動とは?生産性と安全性を高める改善の進め方
-
2025年6月30日
産業用ロボットとは?サービスロボットとの違いや種類、導入するメリットを解説
-
2025年6月30日
工場の省人化に取り組むメリットを解説!具体的なステップと事例をご紹介
-
2025年6月30日
【産業用ロボット】主要メーカーの市場シェアはどれぐらい?市場規模などわかりやすく解説
-
2025年5月28日
事例から学ぶ工場の安全対策!製造業の労災件数も紹介
-
2025年5月28日
ベンダーコントロールとは?定義やToDoを解説
-
2025年5月28日
外部コンサルタントとは?内部との違いやメリット・デメリット
-
2025年4月25日
勘と経験に頼らないモノづくりとは?製造業10社のデータ活用事例を紹介