合理化とは?製造業における意味と効率化との違い・事例3つをご紹介
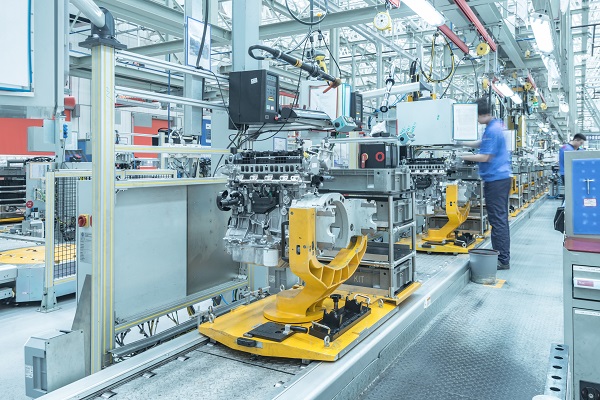
合理化とは、ムダを省いて能率を上げ、生産性を高めようとすることです。特に製造業の現場においては生産性を高めるために合理化はとても重要視されています。なぜなら、合理化を進めると持続的な生産性向上、有限資源の有効活用ができるようになるからです。
合理化は日本の製造業における問題や課題を解消し、進化し続けるマーケット競争に打ち勝つための鍵となります。ただし、合理化を進めるときは特に効率化との違いに気をつけながら、慎重に進めていかなくてはなりません。
今回は、製造業における合理化の意味と重要性、効率化との違いなどについて解説します。合理化を進めるべき理由や注意点、製造業での事例3つも紹介するため、ご参考にしてみてください。
コンテンツ
合理化とは|製造業における意味
製造業において合理化とは、業務を能率的にすることを指します。
合理化=人件費削減のイメージを抱いている人が多いのですが、実際にそれだけではありません。製造業における合理化は、省力化・組織化を進め、生産性向上を目指すことです。そのために人件費削減を検討することもありますが、業務のムダを省いて工程を削減したり、適材適所となるように人員配置を見直したりと、アプローチする方法はたくさんあります。
合理化と効率化の違い
合理化と似た言葉に、「効率化」があります。どちらもムダを省いて生産性を高める意味は同じですが、重視している点に大きな違いがあります。まず合理化は、誰もが納得することを重視しています。経営層も従業員も全員が合理的な取り組みであると、納得して進めていくことが前提です。
一方、効率化は合理化に比べると機械的で、経営層が決定すれば従業員が納得していなくても、進めていくことが特徴です。ニュアンス的な意味の違いとも捉えられますが、合理化は効率化よりも理由づけがあることから、誰もが納得するようにムダを省くことを重視しています。そのため製造業においては、合理化を重視した取り組みが求められています。
合理化を進めるべき理由
合理化を進めると、製造業におけるさまざまな現場の問題が解消されます。最終的には、企業の価値や競争力向上にもつながることがメリットです。それでは製造業が合理化を進めるべき理由を解説します。
持続的な製造実力の維持向上を目指すため
製造業における合理化の取り組みでは、具体的に以下のようなことを実行します。
- 今ある業務の手順や管理方法を見直す
- 使用器具や機械が適切かどうかを検討し見直す
- 人員配置を変更し、各所の必要人員数を最適化する
見直しや検討を行った結果、ムダな手順や業務は思い切って省いたり、効率的な機械設備を新たに導入したりすることもあります。製造業では機械に任せられる業務は機械に任せ、人が本当に必要な仕事だけに集中できるようにすることで、持続的な生産性の維持・向上を目指せるようになります。
結果的には企業の価値も高め、最新の顧客ニーズにも対応できるようになり、市場競争を勝ち抜くことにもつながります。
有限資源を最大限に有効活用できるようにするため
有限資材の中でも、日本の製造業において人材は最も重要であるといえます。日本は少子高齢化が著しく、労働人口不足における問題が深刻化しています。事務職やサービス職が好まれる傾向にある近年の日本で、製造業での人材を確保することは難しいのが現状です。そこで、人材をメインとする有限資材をムダなく最大限に活用できるかどうかが、今後の製造業の企業の命運を分けることになります。
合理化では機械化や自動化、人員配置の見直しなどを行い、従業員が適材適所に輝ける職場環境を目指すことも目的の一つです。人材を最大限に活用するというのは、決して従業員を酷使することではありません。無理のない働き方で、従業員が健康的に能力を最大限発揮できる環境作りを目指しましょう。結果的に従業員のやる気の向上やモチベーション維持により、生産性の向上につながることになります。
合理化を進めるときの注意点
合理化は、製造業の企業存続に関わる重要な取り組みですが、合理化を進めるときは、慎重に判断と実行をしていく必要があります。ここでは合理化を進めるときの注意点を解説します。
業務や人員を機械的に切り捨てない
合理化の目的は、ムダを省いて誰もが納得した上で生産性を高めることです。
特に気をつけたいのは、業務や人員を安易にムダと判断し、機械的に切り捨ててしまうことです。人件費削減は大きなコストカットになり、一見、合理化のわかりやすい成功例となります。
しかし、人件費削減によって人員不足が生じたり、残された従業員への負荷が増えたりするケースは少なくありません。短期目線では大きなコストカットとなりますが、長期的に見るとそれでは生産性向上は見込めません。合理化を進めるうえで業務や人員の削減を検討するときは、長期目線で維持や向上が見込めるか、慎重に判断する必要があります。
生産ラインの自動化にはステージがある
製造業で合理化を進めるときに、生産ラインの自動化を目指すケースが多くあります。生産ラインの自動化が実現すると、生産性は大きく向上します。従業員の労働力削減や働き方改革にもつながる、重要な試みの一つです。
しかし、生産ラインの自動化は、一瞬にして実現できるものではありません。
生産ラインの自動化には、以下のようなステージがあります。
- すべて手作業の状態
- 一部が手作業の状態
- 大半が自動化の状態
- 完全自動化の状態
一度に自動化を目指すのではなく、手作業の部分における業務比率を少しずつ下げていくイメージです。
段階を無視して無理に自動化を進めると、従業員たちへの負担が増えたり、思わぬミスが生じたりする可能性があります。合理化の試みの一つである生産ラインの自動化は、長期目線で段階的に取り組むものであると理解しておきましょう。
製造業での合理化の事例3つ
製造業における合理化では取り組むことが多いため、具体的なイメージを抱きづらい人もいるでしょう。そのため合理化の取り組みを考案するときは、製造業における事例を参考にすることがおすすめです。ここでは日本の製造業での合理化の事例3つをご紹介します。
問い合わせ業務をコールセンターに集約
石油ファンヒーターを主力商品として製造販売している会社では、問い合わせやアフターサービスを各営業所で受け付けていました。そのため対応業務の負荷は大きく、他の仕事を圧迫したり残業が増えたりしている問題がありました。この問題を解消するために、同社は問い合わせやアフターサービスの対応業務を、本社のコールセンターに集約し、必要に応じて、各営業所への対応に切り替える体制へと変更しました。その結果、各営業所の対応業務負荷が大きく軽減され、残業時間も大幅に減りました。
参考出典:https://www.justsystems.com/jp/lab/efficiency/productivity-improvement.html
会議時間が短くなるよう工夫し労働時間を削減
電子基板を製造している会社では、生産性を下げずに職場環境を良くするために、会議時間の短縮を目指しました。具体的には、会議は45分までと時間制限を設けたり、全員が起立したまま参加する形式を、取り入れたりしました。結果、3年間で月の平均所定外労働時間を、約10時間削減することに成功。生産性が落ちることもなく、売上も営業利益も増えています。
参考出典:https://www.justsystems.com/jp/lab/efficiency/productivity-improvement.html
申請や決済業務を電子化しアナログ的な業務を改善
電力供給システム全般を提供している会社は、会議資料を紙で印刷していたり定型業務を手動で行っていたりと、アナログ的な環境でした。合理化のために、会議資料はタブレット端末で共有するように変更(ペーパーレス化)、定型業務はRPAで自動化など、IT技術を取り入れました。さらに、申請・決済業務を電子化するワークフローシステムも導入し、手動の必要がない業務は徹底的に、機械に任せるようにしました。結果、月の平均所定外労働時間が減少し、従業員が心身ともに健康な働き方ができる、「健康経営」が実現しました。
参考出典:https://work-holiday.mhlw.go.jp/detail/04431.html
合理化は製造業において欠かせない取り組み(まとめ)
合理化は、人件費削減のことを指すと誤解されがちです。製造業における合理化は、業務や環境のムダを徹底的に見抜いたうえで行う、生産性向上のための取り組みです。合理化を進めると、製造実力の維持向上を目指しながら、日本の製造業の課題である人手不足問題の解消にもつながります。
注意点は、合理化のために業務や人員を機械的に、切り捨てないようにすることです。合理化は生産性向上や従業員の働き方改革と、企業価値を高めることが最終目的です。何でも省けばいいということではなく、実行する合理化の取り組みによって、どのようなメリットを得られるのか、慎重に考えながら進めていく必要があります。
日本の製造業会社では、合理化を成功させた事例がたくさんあるため、イメージが湧きづらい場合は、参考にしてみることもおすすめです。
今日のポイント
- 合理化の製造業における意味はムダを省いて能率を上げ、生産性を高めようとすること
- 合理化と効率化の違いは前者は後者より理由づけがあり、誰もが納得するようにムダを省く点を重視していること
- 製造業で合理化を進めるべき理由は、持続的な製造実力の維持向上と有限資源の有効活用を実現するため
- 合理化を進めるときの注意点は、業務や人員を機械的に切り捨てないこと、生産ラインの自動化には段階があると理解しておくこと
製造業のDXはあおい技研
株式会社あおい技研は、製造業に特化した業務改善コンサルティングを提供し、製造現場のDX推進をサポートします。80以上の製造現場での診断や改善の経験を活かし、お客様に合ったDX戦略を提案します。
データ分析、業務効率化システムの開発、現場のデジタル化などを通じて、お客様の業務改善と生産性向上を支援します。
製造業のDXについては、あおい技研にご相談ください。
関連記事
-
労働生産性の計算式2つを初心者向けにわかりやすく解説|製造業が低い理由と向上させる方法
2024年8月15日
-
労働生産性を上げるには労働環境の見直しが大切【向上させる4つの方法と低い理由】
2023年9月12日
-
業務の効率化の具体例5つ!成功事例も併せて紹介
2024年7月9日
-
工程能力とは?基礎や工程能力指数の計算式を5つのステップでご解説!
2022年6月15日
-
業務効率化の成功事例7つを参考にアイデア出しをしよう!業務の無駄の見つけ方も解説
2023年12月12日
-
工場のヒヤリハットの原因4つ!対策と改善案のネタ切れに役立つ事例も紹介
2024年4月5日
-
製造業の人材育成をするときのポイント6つ【生産性向上につながる】
2024年5月7日
-
作業の効率化が進まない理由5つ!製造業における向上の事例も紹介
2023年9月12日
-
生産性の式5つを紹介【製造業における生産性分析の重要性と注意点】
2024年8月15日
カテゴリー
- IT化
- QCD
- QCサークル
- コスト削減
- コンサルタント
- スマートファクトリー
- ボトルネック工程
- 中小企業
- 労働生産性
- 合理化
- 品質担保
- 品質管理
- 在庫管理
- 工場IoT
- 工場効率化
- 工程管理
- 工程管理システム
- 投入資源
- 業務効率
- 業務改善
- 生産ライン
- 生産性向上
- 生産管理
- 生産管理システム
- 経費削減
- 製造業
- 製造業 DX
- 製造業IoT
- 見える化
- 設備管理
新着コラム
-
2025年7月30日
工場の労働環境を改善するための具体策とは?改善のステップや事例もご紹介
-
2025年7月30日
工場の暑さ対策を徹底解説!2025年義務化対応と効果的な対策とは?
-
2025年7月30日
工場の5S活動とは?生産性と安全性を高める改善の進め方
-
2025年6月30日
産業用ロボットとは?サービスロボットとの違いや種類、導入するメリットを解説
-
2025年6月30日
工場の省人化に取り組むメリットを解説!具体的なステップと事例をご紹介
-
2025年6月30日
【産業用ロボット】主要メーカーの市場シェアはどれぐらい?市場規模などわかりやすく解説
-
2025年5月28日
事例から学ぶ工場の安全対策!製造業の労災件数も紹介
-
2025年5月28日
ベンダーコントロールとは?定義やToDoを解説
-
2025年5月28日
外部コンサルタントとは?内部との違いやメリット・デメリット
-
2025年4月25日
勘と経験に頼らないモノづくりとは?製造業10社のデータ活用事例を紹介