工場の動線を安全に確保するための手順を3ステップで紹介!レイアウト図の書き方も
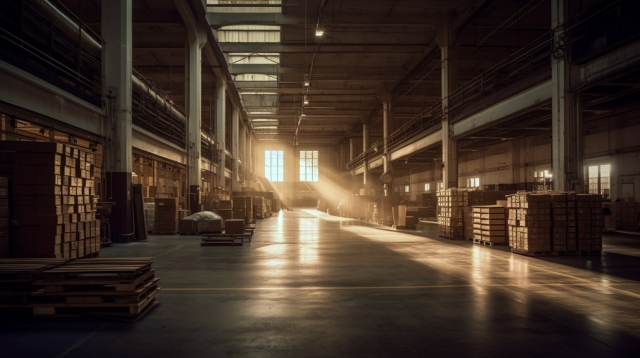
工場の動線は、製造業において業務を安全かつ効率的に行うために、重要な要素の一つです。生産業務全体の流れに沿った工場の動線は、生産性向上に大きく貢献します。いっぽう工場の動線レイアウトに問題があると、業務や作業に無駄が多く生じることになり、生産性が低下してしまいます。
またミスの増加や事故の発生など、安全面でのリスクが生じやすくなることが大きな問題です。現場で働く従業員が安全に快適に業務作業に取り組めるかは、管理者が設計する工場の動線レイアウトが鍵になります。今回は、工場の動線を安全に確保するための手順を3ステップで紹介します。
工場の動線を表すレイアウト図の書き方も解説するので、ご参考にしてみてください。
コンテンツ
工場の動線改善・効率化は生産性向上に大きく貢献する
工場の動線とは、工場内での作業員や製品、業務の流れのことです。製造業の工場では、多数の作業員と生産工程が存在しています。工場の動線の流れが悪いと、以下のように安全面と業務の効率面で、問題が生じる恐れがあります。
各手法について、それぞれ具体的に解説します。
- 人の動きが重なり合う動線により作業者同士の接触事故
- 人と機械設備の距離が近すぎる動線で人と機械設備の接触事故
- 不必要に長すぎる動線でロスタイムの発生
- 保管エリアと出荷エリアが混合している動線で出荷ミスの増加
- 関係部署間の距離が遠すぎる動線で伝達ミスの発生
工場の動線は、安全の確保と業務の効率化に大きな影響を与える重要な項目です。企業として従業員の安全を守り、生産性向上を目指すのであれば、工場の動線改善に取り組むことが重要な課題になります。
工場の動線を安全に確保するための手順3つ
工場の動線を改善するときは、第一に安全面を考慮するようにしましょう。従業員の安全面確保を優先してから、効率化も意識して設計するのが企業の努めです。工場の動線を安全に確保するための手順3つを紹介します。
工場の動線分析をする
工場の動線を改善するときは、まず現状のレイアウトの分析を行います。レイアウトの動線分析をするときは、人や製品の全体の流れを俯瞰的視点で確認することから始めましょう。工場の動線を安全に確保するためには、以下のような点に着目することも大切です。
- 過去にトラブルや事故が発生した箇所
- ヒヤリハット案件が多発している箇所
- 動線が狭く、人同士や人と機械の接触が多い箇所
事故を未然に防ぐ意識を持ち、少しでも懸念する箇所があれば動線改善の対象としてみましょう。動線分析の具体的なやり方としては、現状の動線の長さを算出しておくことが必須です。
改善後と比較できるように、製品ごとの人や製品の流れ、作業手順等を可視化したシートを作成します。また、動線分析をするときは、整流化を意識することも重要です。整流化とは、モノが制作工程に合わせて、順序良く流れるようにすることです。工場の動線が整流化すれば、きちんと工程が連結するようになり、付加価値作業が最短で効率良くつながるようになります。
レイアウト図を見直して改善する
工場の動線分析が完了したら、実際にレイアウト図を見直して改善していきます。動線を安全に確保するためには、具体的に以下のようなポイントを意識しましょう。
- 「通路」「作業場」「資材置き場」など区分を設ける
- 設けた区分を誰が見てもわかるようにする
部門別にエリア分けを明確にすることで、工程に沿った自然かつ安全性の高い動線が実現しやすくなります。設けた区分は誰が見てもわかるように、表示等を実施するのもポイントです。
工場の動線改善の効果検証をしながら定着化を目指す
工場の動線のレイアウト図の見直しと改善が完了したら、効果検証を実施します。改善後は、改善前の問題点(事故が多く発生していた箇所、危険が潜んでいた箇所など)がきちんと解消されているか、効果検証をしながら定着化を目指すことも大切です。
動線改善をしたことで、思わぬ新たな安全面での不安が生じるケースもあります。その際はすぐに見直し改善できるよう、PDCAサイクルをスピーディーに回していく意識も重要です。
工場の動線を表すレイアウト図の書き方
工場の動線を表すレイアウト図は、原案であれば手書きで作成することもあります。大まかな骨組みを手書きで作成後、最終決定となるレイアウト図は誰が見てもわかるように、専用のソフトやアプリを使ってブラッシュアップしましょう。
エクエルを活用して作成することも可能です。
工場の動線を表すレイアウト図の具体的な書き方の例には、以下のような手順があります。
- 1.改善前のレイアウト図を入手して面積を把握
- 2.改善前のレイアウト図をベースにして骨組みをトレース
- 3.デッドスペースになっている箇所、安全面に懸念がある箇所、短縮できそうな箇所などを探す
- 4.優先する製品を決定するために製品ごとの物量を確認
- 5.従業員と製品の動きを確認し、業務過程が似ているグループは近くに配置するなど、作業の流れに沿う動線改善案を書き足していく
ポイントは、誰が見てもわかるような表記にすること、改善前と改善後の違いが明確になるようにすることです。担当者複数人で広い視野を持って、根本的な見直しと改善結果を出せるよう、重要なプロジェクトとして取り組むようにしましょう。
工場の動線を安全に確保するためには分析・改善・定着化が大切(まとめ)
工場の動線は、従業員の安全面を確保するうえで、とても重要な項目です。動線の見直しと改善を行うときは、まずは現状の分析をすることから始めましょう。従業員と製品の動き全体を、俯瞰的視点から考えることが大切です。
工場の動線を安全に確保するためには、過去にトラブルや事故が発生した箇所、ヒヤリハット案件が多発している箇所、動線が狭く人同士や人と機械の接触が多い箇所に、着目するのもポイントです。従業員の安全を確保するためには、事故を必ず未然に防ぐという高い意識を持つことも重要になります。
動線の分析・改善・定着化を意識して、PDCAサイクルを回しながら、実行していきましょう。
今日のポイント
- 工場の動線は安全の確保と効率化に大きな影響を与える重要な項目
- 工場の動線を安全に確保するための手順3つは「工場の動線分析」→「レイアウト図を見直して改善」→「工場の動線改善の効果検証をしながら定着化を目指す」
- 工場の動線を表すレイアウト図はアプリやエクセルを使っての作成もでき
製造業のDXはあおい技研
株式会社あおい技研は、製造業に特化した業務改善コンサルティングを提供し、製造現場のDX推進をサポートします。80以上の製造現場での診断や改善の経験を活かし、お客様に合ったDX戦略を提案します。
データ分析、業務効率化システムの開発、現場のデジタル化などを通じて、お客様の業務改善と生産性向上を支援します。
製造業のDXについては、あおい技研にご相談ください。
関連記事
-
QC(品質管理)とQA(品質保証)の違いを3つの項目で徹底解説!
2022年8月23日
-
製造業における教育計画を立案するときの手順6ステップ!重要性と具体例
2024年9月2日
-
QCDとは?初心者向けに4つのポイントで重要な理由や関係性を解説!
2022年9月20日
-
工場の稼働率を上げるには?有効な方法3つと計算式の求め方や目安を解説
2023年10月13日
-
在庫管理をバーコードでするメリット3つ!デメリットやエクセルで自作する方法も解説
2023年11月6日
-
改善点とは?製造業における意味と洗い出すときに必要な7つの視点
2023年5月23日
-
業務効率化ツールを選ぶときのポイント5つ!エクセルで自作するのはあり?
2023年3月20日
-
改善のフレームワーク7選|ECRSやKPTなど役立つアイデアを初心者向けに徹底解説
2023年4月17日
-
工場を効率化する事例10個【製造業の小さな改善アイデア】
2022年4月28日
カテゴリー
- IT化
- QCD
- QCサークル
- コスト削減
- コンサルタント
- スマートファクトリー
- ボトルネック工程
- 中小企業
- 労働生産性
- 合理化
- 品質担保
- 品質管理
- 在庫管理
- 工場IoT
- 工場効率化
- 工程管理
- 工程管理システム
- 投入資源
- 業務効率
- 業務改善
- 生産ライン
- 生産性向上
- 生産管理
- 生産管理システム
- 経費削減
- 製造業
- 製造業 DX
- 製造業IoT
- 見える化
- 設備管理
新着コラム
-
2025年7月30日
工場の労働環境を改善するための具体策とは?改善のステップや事例もご紹介
-
2025年7月30日
工場の暑さ対策を徹底解説!2025年義務化対応と効果的な対策とは?
-
2025年7月30日
工場の5S活動とは?生産性と安全性を高める改善の進め方
-
2025年6月30日
産業用ロボットとは?サービスロボットとの違いや種類、導入するメリットを解説
-
2025年6月30日
工場の省人化に取り組むメリットを解説!具体的なステップと事例をご紹介
-
2025年6月30日
【産業用ロボット】主要メーカーの市場シェアはどれぐらい?市場規模などわかりやすく解説
-
2025年5月28日
事例から学ぶ工場の安全対策!製造業の労災件数も紹介
-
2025年5月28日
ベンダーコントロールとは?定義やToDoを解説
-
2025年5月28日
外部コンサルタントとは?内部との違いやメリット・デメリット
-
2025年4月25日
勘と経験に頼らないモノづくりとは?製造業10社のデータ活用事例を紹介