工場を効率化する事例10個【製造業の小さな改善アイデア】
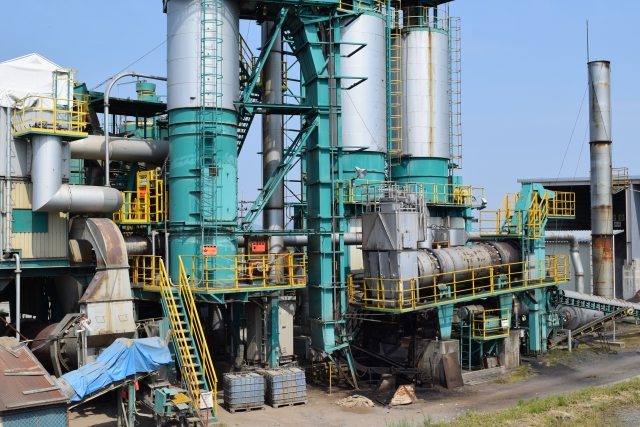
工場を効率化するために、まずは小さな改善アイデアから取り組んでいきましょう。小さな改善アイデアから取り組むメリットは、比較的簡単で即効性があり、効果をすぐに実感しやすいことです。現場の作業員が日々の業務の中で困っていること、不便だと感じていることを中心にアイデアを出すようにすれば、改善の成果は自然と高くなります。
工場の改善案実施では、継続が不可欠ですが、自分たちで出して取り組んだ改善案であれば、定着しやすくなることもメリットです。今回は、工場を効率化する事例10個【製造業の小さな改善アイデア】をご紹介します。工場を効率化するときのポイントもまとめているため、ご参考にしてください。
工場を効率化するときのポイント
工場を効率化するためには、現場の作業員のモチベーションを大切にすることが重要になります。形だけの改善案や改善への取り組みの負荷が、大きくなりすぎたりしないように気をつけましょう。工場を効率化するときのポイントをご紹介します。
目的を見失わない
工場の効率化は、問題や課題を改善することで働きやすい環境を整え、生産性を向上させることが目的です。改善アイデアを出すときは、その改善案でどんな問題や課題を解消できるのか、一つ一つの目的も見失わないように気をつけましょう。
改善アイデアをたくさん出すのは良いことですが、例えば「改善案を、一人◯個出すように」というような指示でノルマを決めてしまうと、逆効果になってしまうこともあります。改善アイデアを出すこと自体が、目的やノルマになってしまいがちだからです。改善アイデアは量よりも質を重視して、得られる成果を意識しながら取り組んでいきましょう。
小さな改善を大切にする
工場の効率化は、複数の小さな改善から成り立ちます。工場の効率化を成功させるポイントは、取り組むハードルが高い大きな改善よりも、すぐに実行できる小さな改善から始めることです。小さな改善の達成感は、更なる改善へのモチベーションアップにもつながります。
効果をすぐに実感できるメリットもあるため、まずは日々の業務に潜む、身近な改善ポイントを探すことから始めてみましょう。
改善案の実行によって負荷が増えていないか気をつける
改善アイデアの実行により、新たな業務が加わる場合は特に注意する必要があります。
例
- 梱包材を安いものに見直したが、梱包の作業手順などが増えてしまった
- マニュアルをデジタル化したが、タブレットの操作性が不安定で、作業員が確認しにくくなり、結果的にする確認する頻度が減ってしまった
総合的に見てプラスに働くのであれば(コスト削減やミスの低減など)問題ありませんが、負荷の方が大きくなるようであれば本末転倒です。
改善による負荷が増えると作業員たちのモチベーション低下につながり、継続的な改善が維持できなくなってしまう可能性もあります。取り組もうとしている改善アイデアは、総合的に見て本当に価値のあるものなのか、負荷が増えすぎていないか気をつけながら進めましょう。
工場を効率化する事例10個【製造業の小さな改善アイデア】
工場を効率化するための改善アイデアは、いざ考えようと思っても、なかなか浮かばないことがあります。改善アイデアの考案に悩んだときは、製造業での事例を参考にすることがおすすめです。
工場を効率化する事例10個【製造業の小さな改善アイデア】を今回はご紹介します。
1.作業台の天板を高く幅の広いものに変更
改善前の問題点
作業台の天板が低いため、作業や図面を見るときに姿勢が悪くなり、作業員の腰に負担がかかっていました。天板の幅も狭く、物をあまり置けないため、他の作業ができない問題点もありました。
取り組んだ改善アイデア
作業台の天板を高く幅の広いものに変更
改善後の成果
作業のとき前に屈む必要がなくなったため、作業員の腰の負担が軽減した。またスペースが広くなったため、作業もしやすくなりました。
参考出典:https://www.imao.co.jp/kaizen-118.html
2.階段での転倒を防止するために金網を取り付け
改善前の問題点
切削水で階段が濡れており、滑りやすく危険でした。階段でバランスを崩し、ヒヤリとすることもありました。
取り組んだ改善アイデア
階段に滑り止めとして金網を取り付けた
改善後の成果
靴底についた切削水が網目に落ちやすくなり、階段が滑らなくなりました。
参考出典:https://www.imao.co.jp/kaizen-109.html
3.備品置き場を指定化して整理整頓
改善前の問題点
備品が乱雑に置いてあり、取り出しづらい状態でした。同じ備品や、使えないものも混ざっており、無駄や手間もたくさんありました。
取り組んだ改善アイデア
備品の使用頻度を調査して置き場を指定化
改善後の成果
必要な備品を、取り出しやすくなりました。指定場所に備品がないと、ひと目でわかるため、備品の持ち出しや紛失についても激減しました。
参考出典:https://www.sunstaff.co.jp/service/improvement/examples/detail/fixtures.html
4.充電状態を判別できるように箱を設置
改善前の問題点
保管しているバッテリーが充電済みか判別できず、交換するときに確認のため何度も付け替えていました。
取り組んだ改善アイデア
「充電未・済」の箱をそれぞれ設け、色分けして表示
改善後の成果
ひと目で充電済のバッテリーがわかるようになり、交換作業の時間が短縮されました。
参考出典:https://www.sunstaff.co.jp/service/improvement/examples/detail/charging-station.html
5.すぐに必要なボルトを見つけるために管理方法を見直し
改善前の問題点
ボルトを大小の区別だけで、1か所にまとめて管理していたため、作業が変わる度に、次に使用するボルトを探す必要があり、時間がかかっていました。
取り組んだ改善アイデア
作業ごとに使用するボルトを分けて管理
作業に対してどのボルトを使えばいいか、一目でわかるようにケースにラベリング
改善後の成果
時間をかけて探していたボルトを、ほんの数秒で見つけられるようになりました。
参考出典:https://www.imao.co.jp/kaizen-122.html
6.新入社員への指導方法を口頭からチェックシートに変更
改善前の問題点
新入社員への教育方法として、口頭だけで指導することがありました。新入社員が指導内容を忘れやすく、困ったときに教育者がいないと疑問点や不安点を確認できないまま、作業に取り組んでしまっていました。
取り組んだ改善アイデア
作業工程のチェックシートを作成(口頭での指導をなくした)
改善後の成果
作業工程の一連の流れが見えることで、「今やること」、「次にやること」がはっきりわかるようになり、確認漏れや確認待ちによるロスなどが低減しました。
参考出典:https://www.imao.co.jp/kaizen-116.html
7.書類の保管方法をファイルから箱に変更
改善前の問題点
書類を種類ごとにファイルに綴じて保管していたため、書類への穴あけ作業や留め具の着脱などに手間がかかっていました。
取り組んだ改善アイデア
ファイルでの保管方法をやめ、入れるだけの箱を設置
改善後の成果
穴あけや留め具の着脱などの手間がなくなりました。また種類ごとに箱をわけているので書類を見つけやすく、取り出しやすくもなりました。
参考出典:https://www.imao.co.jp/kaizen-113.html
8.吊り具の置き方を見直し
改善前の問題点
吊り具を乱雑に置いていたため、必要な時にすぐ取り出せませんでした。足元の吊り具を踏んでしまう危険性もありました。
取り組んだ改善アイデア
吊り具が床面に触れない高さのスタンド式専用置き場を設置
1本ずつ引っ掛けて取れるようにした
改善後の成果
「取り出す・戻す」作業が楽になり、作業時間が短縮されました。床に垂れ下がっている吊り具が無くなり、足元も安全になりリスクの低減も実現しました。
参考出典:https://www.sunstaff.co.jp/service/improvement/examples/detail/lifting-tool.html
9.梱包資材を見直しコスト削減
改善前の問題点
作業性は良いのですが、コストが気になる梱包材を使用していました。
取り組んだ改善アイデア
梱包資材を安いものに変更
改善後の成果
梱包資材費を削減でき、1梱包あたり約110円コストカットできました。
参考出典:https://www.imao.co.jp/kaizen-111.html
10.貯蔵品の発注方法を見直し担当者の負担を軽減
改善前の問題点
発注のタイミングが月に1~2回と少なく、1回に発注する品番数が多くなるため、購買担当者の負担になっていました。
取り組んだ改善アイデア
貯蔵品の棚を4つのエリアに分けて、毎週1エリアずつ在庫を確認し発注するように変更
改善後の成果
発注の回数は増えましたが、1回ごとの品番数が少なくなったため、発注業務の負担が減りました。
参考出典:https://www.imao.co.jp/kaizen-106.html
工場の効率化は事例を参考にして小さな改善アイデアから(まとめ)
工場の効率化は、製造業の企業の利益と発展につながる、重要な取り組みになります。ポイントは、小さな改善アイデアを出して、取り組んでいくことです。小さな改善アイデアであれば、取り組むハードルが低いことがメリットです。
現場の作業員たちが、日々の業務の中で感じている不便さからアイデアを出せるため、得られる成果が大きくなる傾向もあります。注意点は、改善アイデア出し自体が目的になったり、改善案の実行によって負荷が増えたりしないか、気をつけることです。工場を効率化するための、小さな改善アイデア考案に悩んだときは、製造業での事例を参考にして、自社内の改善ポイントを探してみてくださいね。
今日のポイント
- 工場を効率化するためには小さな改善アイデアから取り組んでいくこと
- 小さな改善アイデアから取り組むメリットはハードルが低く、効果をすぐに実感しやすいこと
- 工場を効率化するときのポイントは目的を見失わないようにしながら負荷が増えないように気をつけること
- 改善アイデアの考案に悩んだときは製造業での事例を参考にすることがおすすめ
製造業のDXはあおい技研
株式会社あおい技研は、製造業に特化した業務改善コンサルティングを提供し、製造現場のDX推進をサポートします。80以上の製造現場での診断や改善の経験を活かし、お客様に合ったDX戦略を提案します。
データ分析、業務効率化システムの開発、現場のデジタル化などを通じて、お客様の業務改善と生産性向上を支援します。
製造業のDXについては、あおい技研にご相談ください。
関連記事
-
製造業で品質管理を行うときのポイント4つ【重要性と構成する要素も解説】
2022年2月14日
-
工場内の物流を自動化したい!ハードルはなぜ高い?
2025年2月27日
-
工程管理の基本を3つの項目で徹底解説【工程管理表の作成方法も】
2022年3月28日
-
コスト削減の事例10選!製造業でのネタ出しにもおすすめ
2023年6月30日
-
生産性が高い人とは?特徴をわかりやすく5つのポイントで解説!
2022年12月31日
-
生産性の計算式4つを初心者向けに徹底解説【エクセルでの算出方法も】
2022年12月27日
-
「生産性」の使い方は?低くなる原因3つと対策を徹底解説!
2022年12月19日
-
製造業の効率化を妨げている原因5つ!それぞれの改善法も紹介
2023年1月25日
-
生産性を改善する方法5つ【取り組むべき理由や進めるうえでの注意点】
2022年12月1日
カテゴリー
- IT化
- QCD
- QCサークル
- コスト削減
- コンサルタント
- スマートファクトリー
- ボトルネック工程
- 中小企業
- 労働生産性
- 合理化
- 品質担保
- 品質管理
- 在庫管理
- 工場IoT
- 工場効率化
- 工程管理
- 工程管理システム
- 投入資源
- 業務効率
- 業務改善
- 生産ライン
- 生産性向上
- 生産管理
- 生産管理システム
- 経費削減
- 製造業
- 製造業 DX
- 製造業IoT
- 見える化
- 設備管理
新着コラム
-
2025年6月30日
産業用ロボットとは?サービスロボットとの違いや種類、導入するメリットを解説
-
2025年6月30日
工場の省人化に取り組むメリットを解説!具体的なステップと事例をご紹介
-
2025年6月30日
【産業用ロボット】主要メーカーの市場シェアはどれぐらい?市場規模などわかりやすく解説
-
2025年5月28日
事例から学ぶ工場の安全対策!製造業の労災件数も紹介
-
2025年5月28日
ベンダーコントロールとは?定義やToDoを解説
-
2025年5月28日
外部コンサルタントとは?内部との違いやメリット・デメリット
-
2025年4月25日
勘と経験に頼らないモノづくりとは?製造業10社のデータ活用事例を紹介
-
2025年4月25日
工程設計とは?フロー、重要さを解説【事例あり】
-
2025年4月25日
製造業の工程管理、うまくいかない?原因と解決策を解説
-
2025年3月24日
工程分析とは?使われる記号や手法、改善ポイントを解説