スマートファクトリーとは?DXとの違いをわかりやすく解説
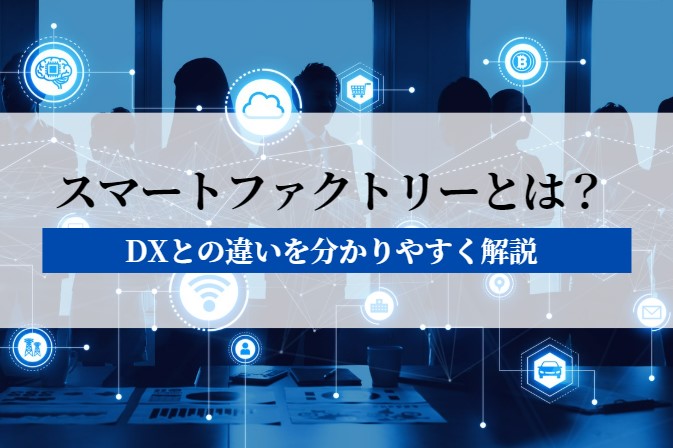
製造業の現場では、生産性の向上や品質管理、コスト削減といった課題が常に求められています。
こうした課題を解決するために注目されているのが、デジタル技術を活用した「スマートファクトリー」です。
スマートファクトリーでは、IoTやAI、ビッグデータを駆使することで工場内の機器やシステムがリアルタイムに連携し、より効率的な生産が可能になります。
また、人の経験や勘に頼っていた部分をデータで補い、トラブルの未然防止や品質の安定化を実現できるのもメリットです。
本記事では、スマートファクトリーの概要やメリット、事例や導入のポイントを解説します。
スマートファクトリーとは?
スマートファクトリーの定義
スマートファクトリーとは、IT技術やIoT、AI(人工知能)、ロボットなどを活用して、生産プロセスを最適化した『次世代型の工場』です。
「スマート=賢い」「ファクトリー=工場」なので、単なる自動化ではなく、データを活用することでより効率的な動きをする工場を目指しています。
これまでは人間の経験や勘に依存していた部分を、センサーで取得したデータをAIが学習・分析し、的確なフィードバックを行うことで、より生産性を高められる点が特徴です。
例えば、不良品が出る予兆の段階でシステムがアラートを発し、作業者がすぐに原因箇所を特定して対策できることで、より迅速な対応が可能になるのです。
★Point
・スマートファクトリーとは、デジタル化・自動化によって従来よりも最適化された仕組みを持つ工場
従来の工場との違い
従来の工場では、ラインの自動化や機械の導入は進んでいましたが、それぞれの機械が独立して動作していました。
スマートファクトリーでは、IoTやAI、ビッグデータを活用し、機械やセンサーがリアルタイムでデータをやり取りしながら連携。
生産状況の見える化や、最適な生産計画の自動調整が可能になります。
また、従来の工場では、設備が故障したら修理を行う「事後保全」や、定期的な点検による「予防保全」が一般的です。
しかし、これだと急な故障でラインが止まるリスクや、まだ壊れていない部品の無駄な交換が発生していました。
スマートファクトリーではセンサーで設備の状態をリアルタイムに監視し、AIが異常の兆候を分析することで、故障の前にメンテナンスを行う「予兆保全」ができるのです。
そのため、設備のダウンタイム(停止時間)を最小限に抑えられます。
★Point
・従来の工場 = 機械が独立して動作
・スマートファクトリー = 設備が連携することで自動最適化
DXとの違い
DX(デジタルトランスフォーメーション)とは、デジタル技術を活用してビジネスモデルや働き方そのものを変革する取り組み全般を指す言葉です。
スマートファクトリーもDXの一種ですが、あくまでも「工場」という製造現場のDXに特化している点で違います。
つまり「スマートファクトリー」は製造現場での具体的な仕組みを指し、「DX」はもっと広い範囲で組織や社会全体を変える概念と捉えるとわかりやすいでしょう。
例えば、営業やマーケティング、オフィスワークのデジタル化はDXですが、スマートファクトリーとは呼びません。
一方、工場内でデータやAIを使った効率化は「スマートファクトリー」と言えます。
★Point
・DX = 企業全体のデジタル変革
・スマートファクトリー = 製造業や工場現場のDX化
スマートファクトリー導入のメリットは?
生産性・収益性の向上
スマートファクトリーでは、生産ラインの稼働状況や作業進捗がリアルタイムに可視化されます。
センサーなどから得たビッグデータをAIで分析し、ラインのボトルネックを迅速に特定することができるため、設備稼働率を飛躍的に高められる点がメリットです。
結果的に、今までと同じ人員・時間でより多くの製品を生産することが可能になり、企業の収益力を底上げします。
品質向上・不良率の低減
従来は不良品が大量に出てから原因追及に着手する「事後対応型」が当たり前でした。
スマートファクトリー化が進むと、製造工程のあらゆるデータが常時モニタリングされるため、不良品が出そうな予兆を捉え、リアルタイムで対策を打てるようになります。
画像検査やAI検知を活用すれば、人の目では見落としがちなミスの早期発見も期待できます。
コスト削減(無駄な工程・在庫の最適化)
大量の生産データをAIが分析することで、需要予測や生産計画を自動化してくれます。
必要最低限の材料・部品のみを適切なタイミングで発注できれば、在庫コストを削減できます。
また、不具合や設備故障によるロスが減れば、結果的に生産コスト全体の抑制につながります。
人材不足の解消と技術継承
生産工程の自動化や省人化が進めば、人員確保が難しい時代でも安定した生産が可能となります。
また、熟練技術者の動きや加工ノウハウをセンサーや動画で記録し、AIに学習させることで若手社員でも熟練者に近い精度で作業できる仕組みが作れます。
このように技術継承に役立つため、製造現場の継続的な成長にも貢献するのです。
予知保全でトラブルを未然に防ぐ
生産設備が突然故障すると、部品の交換費用はもちろん、生産ラインが止まることで大きな機会損失が発生します。
センサーやAI分析により「異音・異常振動のパターン」などを検出すれば、故障が起こる前にメンテナンスを実施でき、設備停止リスクを最小限に抑えられます。
工場全体の見える化による迅速な意思決定
工場の稼働状態を一元管理するダッシュボードを導入すれば、経営層や管理者は工場の状況を迅速に把握できます。
市場の需要変動があった場合、全体の稼働状況を踏まえて「どのラインをどこまで増強できるか」の素早い判断に役立つのです。
スマートファクトリー導入の課題と解決策
【課題】高額な初期投資とROIの不透明さ
スマートファクトリー化には、センサー類やネットワーク設備、AIアルゴリズムを扱うシステムの導入など、まとまった投資が必要です。
そのため導入費用の高さがネックとなりがちで、「ROI(投資対効果)がいつ回収できるのかわからない」という意見も少なくありません。
【解決策】スモールスタートと段階的拡張
★一部ラインだけで検証
全体導入に踏み切る前に、まずは重要度の高い工程や不良率の大きいラインで限定的に導入し、導入効果を測定。
成果が確認できれば他のラインや設備へ展開しやすくなる。
★必要最小限の機器投資
すべてを一度にデジタル化するのではなく、既存の機器・システムとの接続を図る。
優先度の高い部分にだけ新たな投資を行い、費用を分散させる。
【課題】レガシー設備やシステムとの統合
古い生産管理システムや独自の設備が稼働している現場も多く、新しいIoT機器やAIツールがうまく連携できないケースがあります。
データの形式や通信方法が合わないため、導入後にトラブルが起こることも。
【解決策】ゲートウェイの活用と段階的改修
★ゲートウェイ接続
古いシステムと新しいシステムの橋渡しをするゲートウェイ接続を使えば、データを統一してスムーズに連携できる。
★システム入れ替えの優先順位付け
すべての設備を一気に入れ替えるのではなく、老朽化の進んだ機器から更新するなど、段階的に移行する方がリスクやコストを抑えられる。
セキュリティリスク
ネットワークにつながる機器が増えるほど、サイバー攻撃による生産停止リスクや情報漏洩リスクが高まります。
工場内システムがハッキングされると、稼働データを不正操作されて製品品質に影響が出たり、顧客情報が流出する恐れもあります。
【解決策】多層防御と徹底した監視
★ファイアウォール・VPN・暗号化通信
外部からのアクセスを制限・監視する仕組みを用意し、データ通信はすべて暗号化する。
★セキュリティ運用ルールの制定
定期的なアップデートやログ監視など、運用フェーズでの対策を社内規定化して徹底する。
従業員のITスキル不足・抵抗感
現場スタッフのITリテラシーが十分でない場合、新しいシステム導入に抵抗を感じたり、使いこなせずに形骸化してしまいます。
「機械が多すぎてよくわからない」「既存のやり方を変えたくない」といった声が出ることも珍しくありません。
【解決策】教育プログラムと成功体験の共有
★研修やワークショップ
システム導入の初期段階で研修を行い、センサーやAIがどのように業務を改善するのかを体感してもらう。
★小さな成功体験の積み上げ
使い勝手の良いツールを先行導入して、作業効率が上がると実感してもらうことで心理的ハードルを下げる。
スマートファクトリーの事例
三菱電機株式会社
三菱電機では工場の自動化を支えるFA機器について、機器同士のデータ連携が不十分で生産性向上やコスト削減の課題がありました。
スマートファクトリー実現のため、FA機器とITシステムを連携する「e-F@ctory」を開発。
生産現場のデータをリアルタイムで収集・分析し、より適切な制御を行う仕組みを構築しました。
データ活用により生産効率が向上し、より技術連携を強化する体制も整備。
生産現場の情報だけでなく、CADデータなどのエンジニアリングチェーンとの連携も可能になりました。
※参照元:経済産業省┃製造業DX取組事例集┃PDF31ページ
東芝デジタルソリューションズ株式会社
東芝グループは、工場の生産性向上や品質改善を目的に、スマートファクトリー化を促進。
単にシステムを導入するのではなく、IE(インダストリアル・エンジニアリング)の手法とデジタル技術を組み合わせ、現場のカイゼンを進めています。
また、AI画像検査や設備の遠隔監視、KPIの明確化やデータ管理の標準化を取り入れ、バリューチェーン全体のDXを目指しています。
※参照元:製造業DXに向けた東芝の「スマートマニュファクチャリング」の取り組み(後編)
スマートファクトリー導入のポイント
目的・ゴールを明確にする
スマートファクトリーを導入する際には、まず「どの課題を最優先で解決したいのか」を明確にすることが大切です。
例えば「不良率を30%削減する」「段取り替え時間を半減してリードタイムを短縮する」「人材不足を解決して生産量を増やす」など、具体的な数値目標や改善すべき工程を設定しましょう。
目的が明確であれば、導入時の投資対効果(ROI)を測定しやすくなり、経営判断が迅速に行えます。
現場の従業員にも目指す姿が伝わりやすく、モチベーションを高める効果が期待できます。
スモールスタートで効果を検証
すべてのラインや工程を一気にデジタル化すると、現場が混乱したり初期投資が膨らみすぎるリスクがあります。
そこで、まずは特定の工程や生産ラインを対象に部分的な導入を行いましょう。
スモールスタートであれば、導入によるトラブルが起こっても範囲が限定されるため、リカバリーコストを抑えやすくなります。
また、PoC(概念実証)を通じて効果が定量的に確認できれば、他のラインや事業所に横展開する際の社内説得もしやすくなります。
この段階で得られたデータは、システムの微調整や最適化に大いに役立ちます。
データ活用基盤の整備
スマートファクトリーでは、設備やセンサー、ロボットなどから大量のデータが生成されます。
これらのデータをただ集めるだけでは意味がありません。
適切に蓄積・分析・可視化するための基盤(クラウドやデータウェアハウス、BIツールなど)を整える必要があります。
リアルタイムでダッシュボードを確認できるようにすれば、現場と管理者が同じ情報を共有しながら素早く意思決定を下せます。
また、分析で得られた知見を現場へフィードバックし、継続的な改善サイクル(PDCA)を回す体制づくりが重要。
ERP(基幹システム)や生産管理システムと連携し、受注情報や在庫データをリアルタイムに参照できるようにすると、サプライチェーン全体の効率にもつながります。
従業員への教育・組織風土づくり
いくら最先端のシステムを導入しても、現場スタッフがその価値を理解できずに使いこなせなければ意味がありません。
新しい機器やソフトウェアの操作方法だけでなく「なぜデータを使うと現場が良くなるのか」という考え方やメリットをしっかり伝えましょう。
ITリテラシーを上げるための研修やワークショップ、マニュアルや動画の活用なども効果的です。
また、デジタル技術導入による改善アイデアを積極的に募集し、現場からのアイデアやイノベーションを促進する雰囲気づくりも大切です。
まとめ
スマートファクトリーは、従来の製造現場と比べて「データを活用して最適化できる工場」という点で大きな進化を遂げています。
IoTやAIを活用することで 生産性向上・品質向上・コスト削減 など多くのメリットが期待でき、今後の製造業においては欠かせない取り組みとなるでしょう。
ただし、導入には初期投資の負担や既存設備との連携、従業員のITスキルといった課題もあります。
そのため「目的を明確にする」「スモールスタートで段階的に進める」「データ活用基盤を整備する」ことがポイント。
あおい技研では、こうした製造業の課題解決をサポートしています。ぜひお気軽にご相談ください。
製造業のDXはあおい技研
株式会社あおい技研は、製造業に特化した業務改善コンサルティングを提供し、製造現場のDX推進をサポートします。80以上の製造現場での診断や改善の経験を活かし、お客様に合ったDX戦略を提案します。
データ分析、業務効率化システムの開発、現場のデジタル化などを通じて、お客様の業務改善と生産性向上を支援します。
製造業のDXについては、あおい技研にご相談ください。
関連記事
-
製造業のサプライチェーンの課題4つ【対応策】
2024年3月4日
-
工場の稼働率を上げるには?有効な方法3つと計算式の求め方や目安を解説
2023年10月13日
-
スマートファクトリーとは?簡単に5つの事例を交えながら紹介|ロードマップも解説
2023年7月3日
-
業務の効率化の具体例5つ!成功事例も併せて紹介
2024年7月9日
カテゴリー
- IT化
- QCD
- QCサークル
- コスト削減
- コンサルタント
- スマートファクトリー
- ボトルネック工程
- 中小企業
- 労働生産性
- 合理化
- 品質担保
- 品質管理
- 在庫管理
- 工場IoT
- 工場効率化
- 工程管理
- 工程管理システム
- 投入資源
- 業務効率
- 業務改善
- 生産ライン
- 生産性向上
- 生産管理
- 生産管理システム
- 経費削減
- 製造業
- 製造業 DX
- 製造業IoT
- 見える化
- 設備管理
新着コラム
-
2025年8月27日
HACCP 7原則12手順で守る「食の安全」!
-
2025年8月27日
GMP認定で支える「安全性」!製造の信頼は工程から始まる
-
2025年7月30日
工場の労働環境を改善するための具体策とは?改善のステップや事例もご紹介
-
2025年7月30日
工場の暑さ対策を徹底解説!2025年義務化対応と効果的な対策とは?
-
2025年7月30日
工場の5S活動とは?生産性と安全性を高める改善の進め方
-
2025年6月30日
産業用ロボットとは?サービスロボットとの違いや種類、導入するメリットを解説
-
2025年6月30日
工場の省人化に取り組むメリットを解説!具体的なステップと事例をご紹介
-
2025年6月30日
【産業用ロボット】主要メーカーの市場シェアはどれぐらい?市場規模などわかりやすく解説
-
2025年5月28日
事例から学ぶ工場の安全対策!製造業の労災件数も紹介
-
2025年5月28日
ベンダーコントロールとは?定義やToDoを解説