製造業の業務改善アイディア例10選!具体的な見直し方法と注意点もご解説
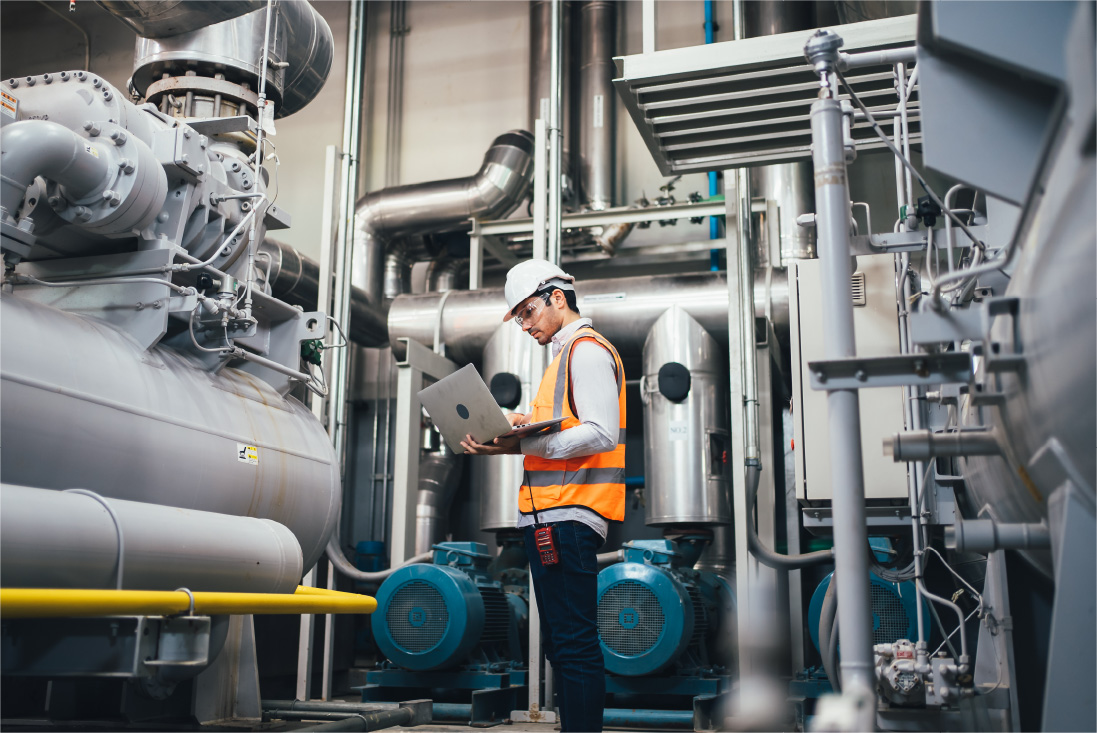
業務改善とは、職場業務の効率を上げるために現在行っている業務を見直して、手順の削減や見直しをすることです。
アイディア自体はたくさんありますが、ただ導入するだけでは高い成果を得られません。
・自社の業務に合ったアイディアを選んで実践する
・必要に応じてアイディアを自社に合うように適応する
こういった取り組みが必要不可欠です。
今回は、製造業で働く方に向けて【自社に応用できる効果の高い業務改善アイディア10選】を厳選してご紹介します。
具体的なアイディアの実践内容をしっかりとお伝えするので、ぜひご参考にしてください。
コンテンツ
製造業の業務改善のアイディア例10選
製造業の業務改善の基本は、3M(ムリ・ムダ・ムラ)を取り除くことです。
ムリ…作業者や設備の能力以上の負荷がかかっている状態
ムダ…作業の手順や内容が非効率で、必要のないものが潜んでいる状態
ムラ…ムリとムダが混在した状態。能力や作業量・品質などが一定でないこと。
それぞれの項目別に、アイディアをご紹介していきます。
【ムリに着目した改善案】
作業者の作業工程や設備の稼働状況にムリがあるということは、改善の余地があるということ。
作業者のムリは心身の疲労を招き、設備のムリは故障や不良品発生率の増加を招くリスクがあります。まずは、作業者や設備のムリがどこに潜んでいるのか考えてみましょう。
繰り返しの多い作業や負荷の高い作業に着目する
繰り返しの多い作業や負荷の高い作業を改善することは、成果の高さに直結します。繰り返し頻度が高いのであれば、改善結果も掛け算で大きく効いてくるからです。繰り返しの多い作業と負荷の高い作業の見直しから始めてみましょう。
滞っている作業や仕掛在庫の積みあがっている工程がないか探す
滞っている作業や仕掛在庫が積みあがっている工程は、作業者や設備の能力で処理しきれていないという証拠です。
作業の滞りや仕掛在庫の積みあげは、「ムダ」の要因にもなります。
作業の滞りや仕掛在庫の積みあげの原因が何にあるのか考えて、改善の試みを行いましょう。
【ムダに着目した改善案】
大手自動車メーカーのトヨタは、「ムダ」を7つに分類しました。
1.加工のムダ
2.在庫のムダ
3.つくりすぎのムダ
4.手持ちのムダ
5.動作のムダ
6.運搬のムダ
7.不良・手直しのムダ
仕事だと思ってやっている作業の中にも、付加価値を生まないムダが存在します。トヨタはムダを無くすために、ムダの種類を細分化しました。
そして、それぞれの項目について「乾いた雑巾を絞る」ように、ムダを省いていきました。分類した7つのムダを見つけ出し減らしていくことで、生産効率は高まります。
作業を主体作業と付帯作業に分ける
主体作業とは、その作業工程において価値を生み出している作業のことです。
付帯作業は、主体作業を行うための段取りや後処理など、価値を生み出す作業以外を指します。
まずは作業をこの二つに分けて、後者の付帯作業を減らすか無くすかできないかを考えてみましょう。
移動や運搬を減らせないか考える
移動や運搬は、付帯作業の最たるものです。
価値を生み出さないので、作業手順を見直して徹底したムダの排除を行う必要があります。
具体的には、
・歩行距離を減らす工夫をする
・移動の導線を見直すことを考える
などです。
工場やラインのレイアウトを見直して、移動や運搬を減らせないか考えてみましょう。
ものを探す時間を減らせるように工夫する
ものを探す時間ほど、ムダなことはありません。
探す時間や置き場を知っている人に確認する時間は、積み上がって膨大な損失になります。
必要な部品や資材、工具をどこに置いてあるのか、どの作業者でもすぐに分かるように、
・定位置
・定品
・定量
を決めて、表しましょう。
定位置、定品、定量を徹底するためにルールを作り管理していくことで、ものを探す時間が発生するのを防げます。
整理・整頓を徹底する
整理とは、不要なものを処分すること。
整頓とは、必要なものがすぐに取り出せるようにすることです。
整理・整頓を徹底すると、必要なものを探すというムダな工程作業がなくなるため、業務の効率がアップします。
作業手順をフローチャートに書き出す
作業手順をフローチャートに書き出すと、
・作業手順を標準化できる
・生産計画を立てるときに利用できる
・主体作業と付帯作業の区別が明らかになる
・工程の組み換え等による改善検討の土台になる
などのメリットがあります。
作業内のどの手順にムダがありそうかなど、工程内の改善ポイントも見えてきます。「ムリ」と「ムダ」の両方を炙り出して、業務改善を行えます。
重複作業がないか確認する
製造業の現場では、意外と重複作業が行われてしまっています。
例
作業実績や入出庫実績などを現場で紙の帳票に記帳
↓
内容を事務所で改めてPCに入力 など
この重複した二つの工程を一つにまとめるだけでも、作業効率は格段にアップします。
重複作業を削減するための手段はいろいろありますが、一つにIT化があります。
ハンディターミナルやタブレット端末を導入するIT化を進めると、工程を削減しながら効率的な作業の実現が可能です。
あおい技研は、製造業の現場作業を効率化できるIT導入を得意としています。
アナログな作業が多くITが浸透していないような現場でも、安心して活用していただけるようなサービス提供を行っています。
【ムラに着目した改善案】
ムラは、日によって工程や作業量に差があることや、作業者に能力差があることによって、
・作業者や設備の足りていないムリ
・作業者や設備が余っているムダ
が発生してしまう状況を指します。ムラを解消するためには、ムリとムダを把握したうえで、どうすれば一定に保てるのか工夫することです。
業務サイクルを見直す
一週間、一か月、四半期などの単位で、業務サイクルを見直してみましょう。
現場では業務の単位ごとに、負荷の高い日や低い日などバラつきが発生するもの。
負荷のムラを一定化させるためには、負荷の低い日に次の作業の段取りや設備のメンテナンスをするなど、負荷の高い日の作業準備に充てるといった工夫がおすすめです。
負荷の低い日と負荷の高い日の負荷が一定に近づき、ムラを減らせます。
要員による能率差がないか確認する
作業者による能率差も、作業時間、負荷のムラにつながります。人によって作業時間にムラがある場合の解決方法は、
・人員配置と人材育成方法を見直す
・横展開できるノウハウがないかを調べる
・効率よく作業している人はどのような作業手順をしているのか確認する
などがあります。
能率差をできるだけ小さくするためには、少しでもそれぞれの能率を上げて均等にできるように、工夫をしましょう。
能率の高い作業者の作業からコツとノウハウを分析し、共有すれば、能率が低い作業者や標準的な能率の作業者の底上げを図れます。
業務改善を行うときの注意点
業務改善に無計画に取り組むと成果を得られなかったり、新たな3M(ムリ・ムダ・ムラ)を生じさせてしまったりと、本末転倒になってしまうこともあります。業務改善を行うときの注意点をご紹介します。
優先順位を決めておくこと
業務改善のために複数のアイディアを導入する場合は、優先順位を決めておくことが大切です。改善に要する費用や時間などのコストや、改善により得られる効果の観点から、
優先順位は、
・改善の難易度が低く、改善による効果が大きいもの
・改善の難易度が高く、改善による効果が大きいもの
・改善の難易度が低く、改善による効果が大きいもの
・改善の難易度が高く、改善による効果が小さいもの
に分類して、上から順に取り組むのがおすすめです。
一度に全てを導入しようとすると現場の混乱を招いてしまう可能性もあるので、一つずつ取り組んでいきましょう。
個別最適化に陥らないようにすること
個別最適化を目指すと、逆にムダな作業が増えてしまうことがあります。
例
・当該工程の業務改善として処理の手順を見直したが、処理の組み換えのために後工程の作業性が悪くなった
・効率化のためにバッチ処理(まとめ作業)をした結果、後工程への部材供給が不安定になった
ある工程の改善が進んだ結果、前後の工程や関連部署の負荷が上がってしまっては意味がありません。
製造業の業務改善を行うときは、全体を見ながらの調整と、改善したことで起こりうる影響を想定することが大切です。
一工程の改善だけに集中して、大局を見失わないように気をつけましょう。
長期的視点を持って取り組むこと
業務改善による成果は、一朝一夕で達成できるものではありません。すぐに成果を出そうとすることは、ムリに繋がります。
大切なのは、製造現場の業務に合った改善案を取り入れる必要や、必要に応じてアイディアを製造現場の業務に合わせて調整することです。
また、製造現場として長期的に達成したい目標に合わせた取り組みである必要もあります。
短期的成果を求めて導入したムダの削減案が、却って長期的目的を阻害することのないように、注意しながら導入していきましょう。
業務改善のアイディアを駆使して効率化を進めよう(まとめ)
今回ご紹介した業務改善のアイディア10選は、どれも製造業の現場で導入できるものです。
大切なのは、そのまま取り入れるのではなく、自社の業務や課題に合ったものを選ぶこと。
業務改善はリソースを投じて長期的に行うものなので、本当に必要なものだけを実行しないと、却ってムダな作業が発生したり、改善案の投入コストが回収できなかったりします。
製造業の効率を高めるには、3M(ムリ・ムダ・ムラ)を見つけ出すことから始まります。
新たな3Mが生まれないように注意しながら、作業工程を見直したり無くしたりという具体的な改善に踏み出すのがおすすめです。
今日のポイント
1.業務改善の基本は3M(ムリ・ムダ・ムラ)を排除すること
2.アイディアは自社の業務に合ったものを選んで導入することが大切
3.実践するときは個別最適化に陥って本末転倒にならないように要注意
製造業のDXはあおい技研
株式会社あおい技研は、製造業に特化した業務改善コンサルティングを提供し、製造現場のDX推進をサポートします。80以上の製造現場での診断や改善の経験を活かし、お客様に合ったDX戦略を提案します。
データ分析、業務効率化システムの開発、現場のデジタル化などを通じて、お客様の業務改善と生産性向上を支援します。
製造業のDXについては、あおい技研にご相談ください。
関連記事
-
工場内の物流を自動化したい!ハードルはなぜ高い?
2025年2月27日
-
生産性が高い人とは?特徴をわかりやすく5つのポイントで解説!
2022年12月31日
-
作業の効率化が進まない理由5つ!製造業における向上の事例も紹介
2023年9月12日
-
工場の自動化に成功した企業の事例5つ【導入メリットやデメリット】
2022年6月27日
-
QC7つ道具を初心者向けに解説!覚え方や使い方を5ステップで紹介
2022年7月4日
-
業務改善で問題点の洗い出しをする方法3つ!重要な理由と注意点もご解説
2022年3月3日
-
製造業の人材育成をするときのポイント6つ【生産性向上につながる】
2024年5月7日
-
改善計画書の書き方を5つの必須項目で解説!記入例がわかるテンプレート付き
2023年4月17日
カテゴリー
- IT化
- QCD
- QCサークル
- コスト削減
- コンサルタント
- スマートファクトリー
- ボトルネック工程
- 中小企業
- 労働生産性
- 合理化
- 品質担保
- 品質管理
- 在庫管理
- 工場IoT
- 工場効率化
- 工程管理
- 工程管理システム
- 投入資源
- 業務効率
- 業務改善
- 生産ライン
- 生産性向上
- 生産管理
- 生産管理システム
- 経費削減
- 製造業
- 製造業 DX
- 製造業IoT
- 見える化
- 設備管理
新着コラム
-
2025年7月30日
工場の労働環境を改善するための具体策とは?改善のステップや事例もご紹介
-
2025年7月30日
工場の暑さ対策を徹底解説!2025年義務化対応と効果的な対策とは?
-
2025年7月30日
工場の5S活動とは?生産性と安全性を高める改善の進め方
-
2025年6月30日
産業用ロボットとは?サービスロボットとの違いや種類、導入するメリットを解説
-
2025年6月30日
工場の省人化に取り組むメリットを解説!具体的なステップと事例をご紹介
-
2025年6月30日
【産業用ロボット】主要メーカーの市場シェアはどれぐらい?市場規模などわかりやすく解説
-
2025年5月28日
事例から学ぶ工場の安全対策!製造業の労災件数も紹介
-
2025年5月28日
ベンダーコントロールとは?定義やToDoを解説
-
2025年5月28日
外部コンサルタントとは?内部との違いやメリット・デメリット
-
2025年4月25日
勘と経験に頼らないモノづくりとは?製造業10社のデータ活用事例を紹介