製造業の工程管理、うまくいかない?原因と解決策を解説
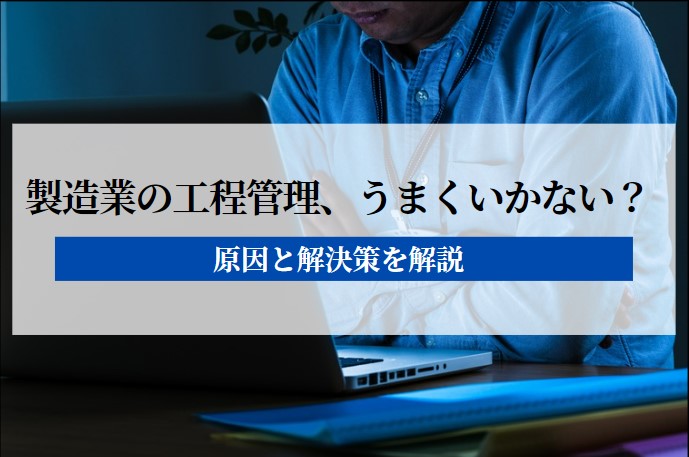
製造業の現場では、「計画通りに進めているつもりなのに、なぜかトラブルが起きる」「進捗が見えず、急に納期が厳しくなる」といった課題はあるあるなもの。
これらの背景に潜むのが、工程管理の機能不全です。
工程管理とは、計画に基づいて製造プロセスをコントロールするための重要な手法。
しかし、現場で実際に運用していくとなると、さまざまな壁にぶつかるのが現実です。
本記事では、工程管理の意味や手順、そしてうまくいかない原因と、改善ポイントを解説します。
コンテンツ
そもそも、工程管理とは?
ものづくりの現場では、品質や納期、コストなど、さまざまな要素を同時に満たす必要があります。そこに大きく関わるのが「工程管理」です。
工程管理とは、生産計画に基づいて製品づくりのプロセスを具体的な行程に落とし込み、進捗を監視・調整するマネジメント手法のこと。
どの工程をいつまでにどれだけ進めるか、人員や設備をどのように配置するかなどを可視化し、その計画を実際の現場で運用していくことに欠かせません。
工程管理はなぜ重要?
納期を守るため
製造業における納期遅れは、単なるスケジュールのズレでは済みません。
取引先からの信頼低下や、場合によっては契約の解除や違約金といった大きな損失につながるリスクがあります。
工程管理が機能していないと、現場では以下のような問題が起こりがちです。
・どの工程が遅れているのか分からない
・ボトルネックが発生しても気づけない
・生産状況がリアルタイムで把握できない
こうした状況では、計画通りに製造が進まず、結果として納期を守ることが難しくなります。
逆に、各工程の進捗状況が「見える化」されていれば、スケジュール調整や人員配置の最適化がしやすくなり、突発的なトラブルにも柔軟に対応できます。
納期遵守の精度が上がれば、顧客からの信頼も高まり、継続受注や新規取引にもつながります。
品質を安定させるため
製品の品質は、設計や素材だけでなく、「どのように作られたか」=工程の管理状況に大きく影響されます。
例えば、以下のようなケースは品質トラブルのもとです。
・作業手順が人によってバラバラ
・使う設備や条件が毎回異なる
・チェック項目が曖昧で、見落としがある
こうした属人化やバラつきが起きている現場では、「なぜ不良が出たのか」が見えづらく、再発防止も困難になります。
工程管理を徹底することで、作業の標準化や品質チェックのルール整備が可能になり、誰がやっても一定の品質を保てる状態がつくれます。
結果的に、不良品の削減やクレーム対応の減少といった品質面での安定が実現できるのです。
無駄なコストを抑え、生産性を上げるため
現場でのムダやロスは、目に見えづらいですが、確実にコストに直結します。
・無駄な待ち時間や手戻りが多い
・進捗が見えず、過剰に人員を割り当てている
・不良対応で材料や時間がロスしている
こうした「ちょっとした非効率」の積み重ねが、生産性を大きく下げてしまいます。
工程管理を通して生産計画や工程ごとの負荷を把握すれば、必要なリソースを必要な場所に正確に配置できます。
また、手戻りや無駄な作業が減ることで、原価が下がり、利益率の改善にもつながります。
単にコストカットするというよりも、ムダを省いて価値のある仕事に集中する体制を整えるという意味で、工程管理はコスト面でも重要なのです。
工程管理の基本手順
工程を設定する
最初のステップは、「どんな工程が必要なのか」を洗い出し、整理すること。
この段階が曖昧だと、後続の計画や管理に影響を及ぼすため、現場のヒアリングや工程分析がポイントになります。
以下のような点を明確にします。
・各工程の作業内容(どんな作業をするのか)
・使用する設備や工具
・作業場所や担当者の配置
・必要な材料や条件(温度・湿度など)
・作業時間の目安(後述の標準時間)
標準時間を設定する
次に必要なのが、「標準時間」の設定です。
これは、1工程あたりにかかる時間の目安であり、生産計画を立てる上での土台になります。
例えば、「この作業は1個あたり15分かかる」と決めておけば、「1時間で何個作れるか」「1日でどれだけ生産できるか」といったことが具体的に計算できるようになります。
この数字がないと、納期の逆算や人員配置が勘頼りになってしまいます。
工程計画を立てる
工程の内容と標準時間が固まったら、実際のスケジュール設計=工程計画に入ります。
ここで決めるのは、以下のような内容です。
・どの工程を、どの順番で、いつまでに終わらせるか
・各工程に何人配置するか
・作業の優先順位や、設備の使用順序
ここで大事になるのが「負荷の調整」。
今どれだけ作業が溜まってるかという「負荷の山積み」、その作業をどう分散・分配するかという「負荷の山崩し」といった考え方で、人と時間のバランスを見ながら、無理のない計画を立てる必要があります。
工程管理がうまくいかない?原因と対策
作業が属人化していて、誰が何をやってるのかわからない
製造現場でよくあるのが、特定の作業が特定の人に依存してしまっている「属人化」の状態です。
例えば、Aさんしか工程Bのやり方を知らない、Bさんが休んだらCの作業が止まってしまう。
こうした状況が続くと、業務の見通しが立たず、工程全体の進捗も管理しづらくなってしまいます。
この状態の一番の問題は、作業内容が「見える化」されていないため、計画も改善もできないこと。
属人化が進んでいる現場では、誰が何をどのように行っているのかが把握しづらく、ミスや遅延の発生にも気づきにくくなります。
こうした課題を解決するためには、作業を標準化し、誰が見ても分かる形で共有することが大切。
具体的な改善ポイントとしては、以下のような取り組みが効果的です。
【Point】
・各作業工程の手順を整理し、マニュアルや作業フロー図としてドキュメント化する
・作業ごとのチェックリストを導入し、作業者ごとのやり方のばらつきを減らす
・業務の属人化状況を洗い出し、「この作業は誰ができるのか」のスキルマップを作る
これらの取り組みによって、万が一担当者が不在でも作業を止めずに進められる体制が整います。
結果として、生産の安定性が高まり、トラブル対応にも余裕が生まれるようになります。
工程全体が見える仕組みがない
工程管理がうまくいかない原因のひとつとして、「今、現場がどういう状況なのか」がリアルタイムで見えないこともあります。
どの工程がどれくらい進んでいるのか、どこで遅れが発生しているのかが把握できないと、的確な判断や対策が取れません。
この「可視化不足」の状態が続くと、納期遅れや人員のムダな再配置、品質のばらつきなどが起きやすくなります。
また、問題が起きても「誰も気づかずに手遅れになる」というケースも。
こうした状況を改善するには、工程ごとの進捗や作業状況を可視化する仕組みが必要です。
【Point】
・Excelやクラウドツールなどを使って、工程表や進捗表を共有する
・作業完了報告をデジタル化し、即時で状況が反映されるようにする
・見える化ボードや、簡易な工程表示システムの導入も有効
進捗が見えるようになるだけで、「気づいたときには遅かった」が減り、トラブルの早期発見・対応が可能になります。
結果として、現場全体の安定感や信頼性も向上します。
管理の方法自体に無理がある
工程管理がうまくいかない根本的な原因として、「管理手法やツールが実情に合っていない」というケースもよくあります。
例えば、複雑な工程を紙やExcelだけで管理していると、情報の抜け漏れや更新ミスが頻発。
また、担当者が変わるとファイルの使い方が分からず、管理が継続できなくなるリスクもあります。
この問題の本質は、「良いツールを使っているか」ではなく、「現場の規模や課題に合ったツールを選べているか」です。
改善するには、まず現場で実際に起きている困りごとを整理したうえで、必要な機能や運用のしやすさに合った方法を選ぶことが大切です。
【Point】
・工程表や進捗表の管理ルールを明確化し、誰でも使える形式にする
・Excel管理に限界を感じているなら、クラウド型の簡易工程管理ツールから試してみる
・複雑な工程や複数ラインがある現場なら、工程管理システムの導入を検討する
システム化が必要かどうかは現場次第ですが、重要なのは「管理のために余計な手間をかけないこと」。
管理が目的にならず、改善につながる手段として機能しているかが重要です。
計画と実行がズレているのに、見直しができていない
工程計画は立てて終わりではなく、日々の実行と結果を照らし合わせて改善することが重要です。
しかし、実際には忙しさのあまり一度立てた計画を放置したまま進んでしまうケースも少なくありません。
こうしたズレが積み重なると、工程ごとのバランスが崩れ、納期や品質、リソース配分に悪影響が出てしまいます。
この問題を解決するには、PDCAサイクルを実践レベルで回す仕組みが必要です。
【Point】
・定期的に「予定と実績のギャップ」をチェックする時間を設ける
・作業記録やトラブル内容を残し、次の計画に活かせる仕組みを整える
・改善提案を歓迎する文化をつくり、現場からの声が反映されるようにする
こうした取り組みを継続することで、計画と実行のズレが少なくなり、工程管理の精度も高まっていきます。
まとめ
工程管理は、製造業における「品質」「納期」「コスト」を守るための大切な土台です。
属人化、可視化不足、ツールの不一致、そして計画の形骸化。
これらの課題は、どの製造現場にも起こりうるものであり、放置していると生産性の低下につながります。
だからこそ大切なのは、「うまくいかない原因」を明確にし、自社の業務フローや規模に合った形で改善していくこと。
小さな取り組みでも、積み重ねることで大きな変化につながります。
製造業専門のコンサルタント「あおい技研」では、こうした現場課題に寄り添った改善支援を行っております。
「何から見直せばいいか分からない」「まずは相談してみたい」そんな段階でも大歓迎です。
現場の悩みを解決したいとお考えの方は、ぜひ一度お問い合わせください。
製造業のDXはあおい技研
株式会社あおい技研は、製造業に特化した業務改善コンサルティングを提供し、製造現場のDX推進をサポートします。80以上の製造現場での診断や改善の経験を活かし、お客様に合ったDX戦略を提案します。
データ分析、業務効率化システムの開発、現場のデジタル化などを通じて、お客様の業務改善と生産性向上を支援します。
製造業のDXについては、あおい技研にご相談ください。
関連記事
-
製造業の業務改善アイディア例10選!具体的な見直し方法と注意点もご解説
2021年10月17日
-
部分最適とは?メリット3つとデメリットを徹底解説!進めるポイントも
2024年10月3日
-
カイゼンは時代遅れ?トヨタ式の基本や進め方・具体例3つを紹介
2022年7月19日
-
ベンダーコントロールとは?定義やToDoを解説
2025年5月28日
-
改善点とは?製造業における意味と洗い出すときに必要な7つの視点
2023年5月23日
-
業務改善の事例7個【進めるときの注意点や気づきの重要性】
2022年9月26日
-
業務プロセス改善の目的3つを徹底解説|役立つフレームワークとコンサル依頼のメリット
2023年9月12日
-
仕事を効率化するのに大切な考え方3つ【意外な方法】
2023年2月27日
カテゴリー
- IT化
- QCD
- QCサークル
- コスト削減
- コンサルタント
- スマートファクトリー
- ボトルネック工程
- 中小企業
- 労働生産性
- 合理化
- 品質担保
- 品質管理
- 在庫管理
- 工場IoT
- 工場効率化
- 工程管理
- 工程管理システム
- 投入資源
- 業務効率
- 業務改善
- 生産ライン
- 生産性向上
- 生産管理
- 生産管理システム
- 経費削減
- 製造業
- 製造業 DX
- 製造業IoT
- 見える化
- 設備管理
新着コラム
-
2025年7月30日
工場の労働環境を改善するための具体策とは?改善のステップや事例もご紹介
-
2025年7月30日
工場の暑さ対策を徹底解説!2025年義務化対応と効果的な対策とは?
-
2025年7月30日
工場の5S活動とは?生産性と安全性を高める改善の進め方
-
2025年6月30日
産業用ロボットとは?サービスロボットとの違いや種類、導入するメリットを解説
-
2025年6月30日
工場の省人化に取り組むメリットを解説!具体的なステップと事例をご紹介
-
2025年6月30日
【産業用ロボット】主要メーカーの市場シェアはどれぐらい?市場規模などわかりやすく解説
-
2025年5月28日
事例から学ぶ工場の安全対策!製造業の労災件数も紹介
-
2025年5月28日
ベンダーコントロールとは?定義やToDoを解説
-
2025年5月28日
外部コンサルタントとは?内部との違いやメリット・デメリット
-
2025年4月25日
勘と経験に頼らないモノづくりとは?製造業10社のデータ活用事例を紹介