工程設計とは?フロー、重要さを解説【事例あり】
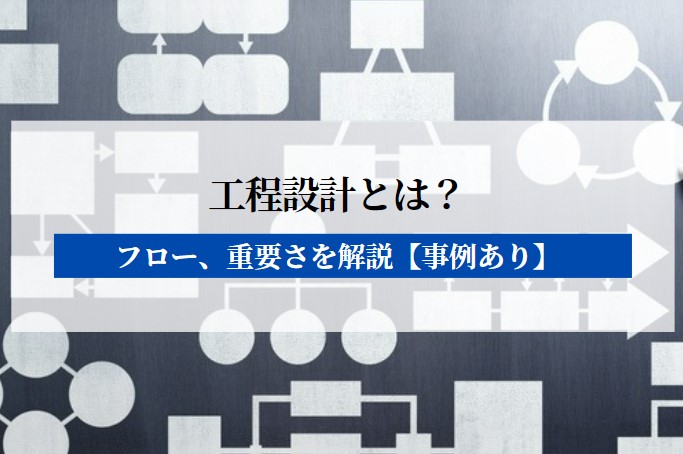
製品を設計するだけでは“モノづくり”は完成しません。
どの工程をどんな順番で、どの機械を使って作るのか――この「工程設計」をしっかりと固めておかないと、不良品が増えたり、コストや納期が予想以上に膨らんだりといったリスクが高まります。
本記事では工程設計の基本的な意味からフロー、重要性、さらにはあおい技研での事例を解説します。
コンテンツ
工程設計とは
工程設計とは、製品や部品の図面に基づいて「モノをどのように作るか」を具体的に決めていく作業です。
どの工程から先に加工を行い、どの機械を使い、どのタイミングで検査を入れるかなどを緻密に検討することで、効率よく高品質の製品を生み出せます。
もしこの工程設計が曖昧なままだと、いくら優れた図面があっても、実際の現場では不良品の発生や、想定外のコスト増大、納期遅れといったリスクが高まってしまいます。
工程設計の根底には「Q(品質)・C(コスト)・D(納期)のバランスをどうとるか」という考え方があります。
どれだけ品質が良くても納期を守れないようでは顧客の信頼を失いますし、コストがかかりすぎて製品価格が高騰すれば競争力を失いかねません。
また、環境負荷や安全性への配慮も欠かせない要素として認識されています。
そうした複数の視点を踏まえつつ、最も合理的でムダのないプロセスを構築するのが、工程設計の大きな役割です。
★関連記事
工程設計のフロー
加工方法を決める
製品設計図をもとに、適した加工方法を選定します。
鋳造やプレスといった「成型」、旋削やフライスなどの「切削加工」、塗装や熱処理といった「処理」、溶接やネジ止めといった「組立」など、選択肢は様々です。
【代表的な加工方法】
・成型:鋳造/鍛造/プレス など
・処理:メッキ/塗装/熱処理 など
・組立:溶接/接着/ネジ止め など
・切削:穴あけ/旋削/平削りなど
内製と外注の範囲を決める
加工方法が決まったら、どの工程を自社でやるか(内製)、どこを外部に頼むか(外注)を検討します。
特殊な技術が必要だったり、自社の設備が足りなかったりする工程は、外注に任せるケースも珍しくありません。
外注を使うことで、結果的にコストを抑えたり、繁忙期の生産量増加に対応したり、供給停止のリスクを分散したりといったメリットがあります。
生産能力を把握する
次に、生産能力をどこまで確保するかを検討します。
これは「どれくらいの量を、どんなペースでつくるのか」という見通しを立てる作業に当たります。
小ロット多品種の製品なら柔軟な対応力が求められますし、大ロット同一製品なら連続生産での効率性が重要になります。
需要や生産方式との整合性を取りながら、無理のない生産体制を設計します。
レイアウトを決める
作業工程に沿って工場のレイアウトを設計します。
単に機械を並べるのではなく、材料や仕掛品の流れ、作業者の動線をスムーズにする工夫が求められます。
よくあるレイアウトとしては、大型製品であれば「材料固定型」、機能ごとに設備を分ける「機能別型」、特定製品ごとに配置する「製品別型」など。
実際の加工フローと一致するように配置することで、ムダを減らし、生産効率を高められます。
工程設計が重要な理由
不良率の削減
工程設計が重要とされる理由は、まず第一に不良率の削減があります。
工程設計の段階で不良の発生要因を洗い出し、加工順序や検査のタイミングを調整しておけば、後からの手戻りを最小限に抑えられます。
不良品を作り込んでしまってから修正するのはコストと手間がかかるため、なるべく初期で不具合を潰しておくのが合理的というわけです。
人的ミスの防止
次に、人的ミスを防ぎやすくなることもポイントです。
作業標準の徹底や設備の自動化により、ヒューマンエラーを起こしにくい工程を組み立てられます。
現場を経験豊富な職人だけに頼る体制では、担当者が変わった途端に品質がガタ落ちするリスクがあるのも事実。
工程設計でそれを防ぐ仕組みを作れば、長期的に安定した品質を維持できるようになります。
製造ライン全体の最適化
三つ目の理由が、製造ライン全体の最適化が進むこと。
個々の工程だけを見て最適化しても、後工程で在庫が滞留していれば意味がありません。
連続生産かロット生産か、あるいは個別生産かといった生産方式をどう選択するかも含めて、全体の流れを考えるのが工程設計の本質です。
こうすることで、作業者や機械設備の負荷を均等化でき、ムリ・ムラのない生産体制を作れます。
工程設計の課題
設計と現場が分断されている
工程設計の課題には、代表的なものとして「設計と現場が分断されている」ことが挙げられます。
例えば、設計部門が独自に材料や仕様を決定してしまうと、実際に加工する現場にとっては扱いにくい素材だったり、コストが高すぎたりするケースも。
購買や品質保証部門の意見が加わらないまま進行すると、後になって不具合が発生してからバタバタと対処しなければならず、結果的に納期やコストへ悪影響を与えます。
作業標準が属人化している
課題の二つ目は、せっかく作った作業標準や工程表が形骸化してしまうことです。
長年の習慣で担当者が独自のやり方に戻ってしまったり、新人がその場しのぎで覚えたために曖昧な作業が続いたりすると、標準化のメリットが得られません。
作業者本人が「なぜその手順が必要なのか」を理解しないまま運用すると、いざトラブルが起きたときに対応が後手に回ってしまいます。
工程設計は理想的なモノづくりを実現するための道筋を示してくれますが、部門間の連携や現場への浸透度が不足していると、そのメリットを十分に活かせません。
だからこそ、設計段階から調達や品質保証、生産現場などの当事者が集まり、それぞれが持つ知識や経験を踏まえて工程を組み立てることが大切です。
あおい技研での工程設計事例
工程設計の効果を実感できる事例として、鋳物製造を手がけるD社に対する、あおい技研の支援をご紹介します。
■会社名 株式会社D(工程計画システムの企画・開発事例)
■業種 製造業(鋳物製造)
D社では長年、工程計画の作成を一部のベテラン担当者に依存しており、「職人の勘」によって日々のスケジュールが組まれていました。
しかし、ベテランの退職を目前に控えたタイミングで、属人化のリスクが表面化。
若手へ引き継いだ際に生産性が大きく落ちるといった問題も起きていました。
あおい技研ではまず、現場の実態を丁寧にヒアリング・観察したうえで、ベテランと若手の工程設計の違いを分析。
その結果、「熱処理炉の使い方」が工程全体の鍵を握っていることが明らかになりました。
しかし、この熱処理工程には、炉の配置や組み合わせの判断、処理パターンの変化対応、前後工程との連携といった複雑な条件が絡み合っており、ルール化が困難な要素が多く含まれていました。
そこで取ったのが、“ベテランの思考を完全再現する”のではなく、“コンピュータの計算力を活かして最適なパターンを導き出す”というアプローチです。
具体的には、以下のような取り組みで工程を最適化しました。
・自動で幾何計算できるエンジンの開発
・製品の組み合わせによる熱処理パターンの自動化
・工程間の自動調整機能を備えたシステム
結果として、新たに導入された工程計画システムは、ベテランが作成したスケジュールと95%の再現性を実現。
属人化の解消とともに、納期見積もりの精度も向上し、経営判断のスピードアップにも貢献した事例です。
★事例の詳細はこちらから
まとめ
工程設計は、単なるスケジュール作成や設備配置の話ではありません。
QCD(品質・コスト・納期)を両立させながら、現場全体の流れを最適化していくための「戦略」と言えるでしょう。
加工方法の選定、内製・外注の判断、生産能力の見極め、レイアウト設計など、それぞれが現場の成果に直結します。工程設計がうまく機能すれば、不良率の低減や生産性向上だけでなく、属人化のリスク回避にもつながります。
製造業専門のコンサルタント「あおい技研」では、工程設計に関するご相談も受け付けております。ぜひご用命ください。
製造業のDXはあおい技研
株式会社あおい技研は、製造業に特化した業務改善コンサルティングを提供し、製造現場のDX推進をサポートします。80以上の製造現場での診断や改善の経験を活かし、お客様に合ったDX戦略を提案します。
データ分析、業務効率化システムの開発、現場のデジタル化などを通じて、お客様の業務改善と生産性向上を支援します。
製造業のDXについては、あおい技研にご相談ください。
関連記事
-
仕事の効率化をするときにやってはいけないこと4つ|大切な考え方
2023年3月20日
-
業務改革プロジェクトを成功に導くコンサルタントの役割と活用ポイント
2021年6月28日
-
業務の効率化の具体例5つ!成功事例も併せて紹介
2024年7月9日
-
製造管理システムとしてMESを導入するメリット4つ|生産管理システムとの違いも解説
2024年1月15日
-
ベンダーコントロールとは?定義やToDoを解説
2025年5月28日
-
工場の動線を安全に確保するための手順を3ステップで紹介!レイアウト図の書き方も
2023年8月4日
-
工場の5S活動とは?生産性と安全性を高める改善の進め方
2025年7月30日
-
製造業の効率化を妨げている原因5つ!それぞれの改善法も紹介
2023年1月25日
-
工場のヒヤリハットの原因4つ!対策と改善案のネタ切れに役立つ事例も紹介
2024年4月5日
カテゴリー
- IT化
- QCD
- QCサークル
- コスト削減
- コンサルタント
- スマートファクトリー
- ボトルネック工程
- 中小企業
- 労働生産性
- 合理化
- 品質担保
- 品質管理
- 在庫管理
- 工場IoT
- 工場効率化
- 工程管理
- 工程管理システム
- 投入資源
- 業務効率
- 業務改善
- 生産ライン
- 生産性向上
- 生産管理
- 生産管理システム
- 経費削減
- 製造業
- 製造業 DX
- 製造業IoT
- 見える化
- 設備管理
新着コラム
-
2025年7月30日
工場の労働環境を改善するための具体策とは?改善のステップや事例もご紹介
-
2025年7月30日
工場の暑さ対策を徹底解説!2025年義務化対応と効果的な対策とは?
-
2025年7月30日
工場の5S活動とは?生産性と安全性を高める改善の進め方
-
2025年6月30日
産業用ロボットとは?サービスロボットとの違いや種類、導入するメリットを解説
-
2025年6月30日
工場の省人化に取り組むメリットを解説!具体的なステップと事例をご紹介
-
2025年6月30日
【産業用ロボット】主要メーカーの市場シェアはどれぐらい?市場規模などわかりやすく解説
-
2025年5月28日
事例から学ぶ工場の安全対策!製造業の労災件数も紹介
-
2025年5月28日
ベンダーコントロールとは?定義やToDoを解説
-
2025年5月28日
外部コンサルタントとは?内部との違いやメリット・デメリット
-
2025年4月25日
勘と経験に頼らないモノづくりとは?製造業10社のデータ活用事例を紹介