業務改善の方法を6ステップでご紹介|具体例やフレームワークも
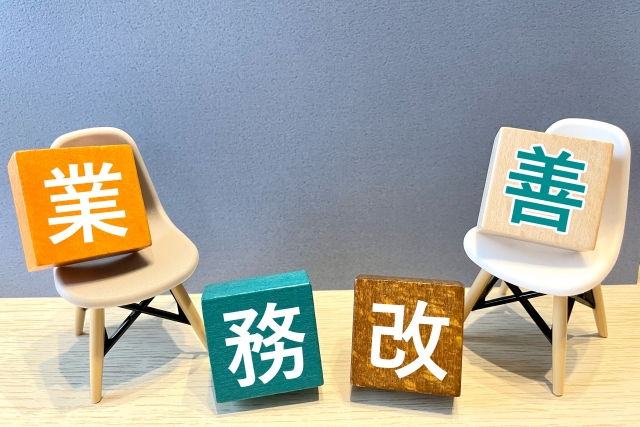
業務改善とは、業務の効率を上げるために現在の業務内容を見直して、手順の削減などにより見直しをすることです。製造業では業務改善を行うことにより、人手不足解消や生産品質の向上を見込めるメリットがあります。
しかし、実際に業務改善をするとなると、
- 「どこから手をつけたらいいのかわからない」
- 「業務改善をどうやって進めればいいのか悩んでしまう」
と踏み切ることが難しいと感じている人も多いのではないでしょうか。
今回は製造業の現場に焦点を当てて、業務改善の方法を6ステップでご解説します。
業務改善の具体例や役立つフレームワークもご紹介するため、ご参考にしてください。
業務改善に取り組む前に
業務改善を実施して成果を出すためには、事前準備が大切です。業務改善に取り組む前に確認しておきたいことをご紹介します。
業務改善の目的を確認する
業務改善の最終的な目標は、QCDを満たして向上させることです。
QCDとは品質(Quality)・コスト(Cost)・納期(Delivery)のことで、製造業に欠かせない3要素となっています。
まず品質(Quality)ですが、業務改善では工程管理システムの導入やツール連携などによって、作業の効率化を目指すケースが多くあります。
業務改善により作業を効率化すると、製造工程の停滞が解消されストレスの無い生産作業が行われ、作業員のミスによる不良発生率の低減が期待できます。
また、機械やシステムを導入すれば、作業の自動化が進み、設定作業等における人的ミスの発生率も下げられます。
品質の向上は顧客満足度に直結し、好影響を及ぼすこともメリットのひとつになります。
次にコスト(Cost)ですが、業務改善では最初の方のステップで、製造プロセスのムダを探し出します。
業務改善によりムダな業務・工程をカットできれば、少ない人数での生産活動が可能となり、作業員の数を減らせるため、人件費の削減が可能となります。
また、あまり機能していない設備やシステムを見直すことで、維持費や管理費などの固定費のコストカットも実現できます。
最後に納期(Delivery)ですが、業務改善による作業の効率化やムダな業務・工程のカットは、生産リードタイムの短縮につながります。
製造業で重要な納期遵守には、リードタイムの短縮が欠かせません。
リードタイムを短縮し、納期遵守を目指すためには、作業工程における段取り時間や運搬時間の効率化などを、業務改善として行うことが効果的です。
このように、1つ1つの業務改善行動の目的を確認しながら進めることが、最終的な目標達成のために重要となります。
業務改善行動自体が手段ではなく、目的にならないようにも気をつけましょう。
現場との共有を大切にする
業務改善案を出すときは、現場とのコミュニケーションやヒアリングを大切にしましょう。
現場に足を運び、どのような問題が生じているのか、実際に目で見てみることも有効です。また、業務改善の達成には現場の作業員の高いモチベーションが欠かせません。
なぜなら、現場の作業員のモチベーションが低いと、業務改善の実施が積極的に進まず、停滞してしまう可能性があるからです。
現場の作業員に高いモチベーションを持って取り組んでもらうためには、本当に困っていることや解決するべきだと思っていることに着眼し、業務改善計画を立てることです。
形だけの業務改善の立案や実施にならないように、現場との共有を大切にしながら進めていく必要があります。
トップダウン式とボトムアップ式がある
業務改善の進め方には、トップダウン式とボトムアップ式の2種類があります。
トップダウン式とは、経営層が業務改善へ積極的に取り組み、自らが立案した業務改善案を各部門や個人に対して落とし込んでいく方法です。経営層主体の手法になります。
一方、ボトムアップ式とは、現場で立案した業務改善案を経営層に提出し、許可を得てから実行していく方法です。こちらは現場主体の手法になります。
それぞれの方法にメリット、デメリットがあり、どちらが適切かは企業の形態や業務改善の目的によって異なります。
例えば、トップダウン式が向いているのは、経営層主体での具体的な立案や判断が必要なため、業務改善として大掛かりなシステムの導入やDXの推進などを考えている場合は有効になります。
反対に、ボトムアップ式が有効な場面は、現場の声を大切にし、現状把握のもとですぐに改善できそうなところから小さく業務改善を始めていきたい場合は効果を発揮すると思います。
実際には多くの企業が、トップダウン式とボトムアップ式を上手く組み合わせて進めています。
どちらかに絞る必要はなく、臨機応変に手法を変えながら進めていく意識が大切です。
業務改善の方法【6ステップ】
業務改善の進め方には、適切な手順があります。ここからは、業務改善の方法6ステップのご紹介です。
1.現状把握
まずは、現場へのヒアリングを中心に現状把握を行います。
現状把握は業務改善実施にあたって、とても重要な項目です。
適切な現状把握が行われていないと、見当違いな問題や課題改善に取り組むことになり、大きな成果が見込めなくなってしまうからです。
次に現状把握を行うために業務内容やフローの見える化を実施します。
ツールを導入して業務内容を数値化したり、業務フロー図を作成したりして、どこにどのような停滞や問題があるのかを洗い出しましょう。
現状把握を怠ると、業務改善を行う意味自体が問われることになりかねません。
最も大切なステップとして、しっかり取り組む必要があります。
2.優先順位付け
現状把握によって問題や課題が洗い出されたら、優先順位を付けていきます。
優先順付けをするときに役立つのは、マトリックス図です。
マトリックス図とは、検討する要素を行と列に配置し、それぞれの関連度合いを交点に表示することで、問題解決を進めていく手法です。
例えば、列に業務改善を行うべき問題や課題を並べ、行には優先順位付けの判断基準(得られる効果の大きさ、必要なコスト、実施の難易度など)を配置します。
交点に◎、○、△などの記号を記入していくことで、優先順位を可視化できます。
3.業務改善方法の検討
優先順位の最も高い問題や課題を改善するために、どのような方法を取るか検討します。
業務改善の方法を考えるときは、「無くす・減らす・まとめる・変える」のどれかで考えると案が出やすくおすすめです。
例
- 無くす…工具を整理整頓し、探す時間を無くす
- 減らす…保管するスペースを工夫し、製品を移動する距離を減らす
- まとめる…製造ラインの区切りを見直し、複数の工程をまとめる
- 変える…新たなマニュアルを作成し、作業手順を変える
など。
4.業務改善計画作成
業務改善をスムーズに行えるように、業務改善計画を作成します。
業務改善計画を作成するときのポイントは、「だれが」「いつまでに」「どこまでするのか」を明確にすることです。
タスクを割り振り、評価方法も決めておくことで、1人1人が責任感を持って計画通りに業務改善を進められるようになります。
5.業務改善計画実施
業務改善計画が作成できたら、進捗状況を確認しながら実施していきます。
途中で上手くいかないことがあれば、適宜やり方や計画を考え直す姿勢を持っておくことも大切です。
業務改善計画を上手く進めるポイントは、まずは簡単なものから取り組むことです。スピード重視でハードルの低い業務改善から取り組めば、成果をすぐに得られます。
得た成果は成功体験となり、次の業務改善に対するモチベーション向上につながります。
モチベーションが高い状態で業務改善に取り組めることができれば、計画進行が加速していき、より高い成果を見込めることが可能となります。
6.業務改善の評価と定着
業務改善を実施したら、振り返り評価を行います。
業務改善にはゴールはありません。業務改善の内容をしっかりと定着できるようにルール化やマニュアル化などを行い、維持・管理することが重要です。業務改善達成後、新たに問題や課題が見つかることもあります。そのときは、また同じ手順で1のステップから取り組んでいきましょう。
業務改善の具体例
製造業における業務改善がイメージできるように、具体例をご紹介します。
進捗管理には工程管理システムを導入する
製造業において、進捗管理はとても重要です。
進捗管理が上手くできていないと、スケジュールの遅延が発生し、納期遅れなどの問題を招くからです。
進捗管理の代表的な方法に、ガントチャートの作成があります。
ガントチャートを作成すると、作業計画を視覚的に表して見える化でき、進捗管理に役立ちます。
ガントチャートは紙やエクセルなどでアナログ的に作成できますが、管理が難しくリアルタイムで把握・共有がしにくいことがデメリットです。
工程管理システムでガントチャートを作成すれば、簡単な入力で正確な進捗状況を把握・共有できるようになります。
連絡事項をタブレットで共有できるようにする
日々の連絡事項(業務の変更点やトラブルなど)を、タブレットなどで確認できるようにします。
朝礼など口頭での連絡共有は忘れやすく、欠勤者には伝わらないことが大きなデメリットになります。
タブレットなどを活用し、連絡事項を保存、閲覧可能な状態にしておけば、見直しもできるため連絡共有がスムーズになります。
連絡事項以外にも、マニュアルや作業手順表なども各ファイルにまとめて、タブレットで共有できるようにしておくと便利です。
新入社員への指導はマニュアルやチェックシートを使う
新入社員への指導は、企業にとって重要です。
指導を口頭で行っている現場が多く見受けられますが、一度で覚えにくく作業前の確認も指導者に聞けない場合はできないデメリットがあります。
結果、作業効率が悪くなったりミスが増加したりと、問題や課題の原因を作ってしまう可能性もあります。
新入社員への指導方法改善としては、マニュアルやチェックシートの活用がおすすめです。
指導者がいなくても自発的にマニュアルを見て判断を行ったり、チェックシートでミスを防いだりできる効果が見込めます。
マニュアルやチェックシートをいつでもすぐに確認できるように、システムで一元管理すると、より作業を効率化できるでしょう。
業務改善に役立つフレームワーク
業務改善を行うときは、フレームワークの活用がおすすめです。業務改善案を出したり計画を立てたりするときに役立つ、フレームワークをご紹介します。
KPT
KPTとは、振り返りのためのフレームワークです。
一般的にはホワイトボードと付箋などを使用して、実行したことや新たな発案を以下の3つに分類していきます。
- K(keep)…良かったこと(今後も続けること)
- P(problem)…悪かったこと(今後はやめること)
- T(try)…今後挑戦すること
KPTは業務改善実施後、評価を行うときに役立ちます。実行したことの評価だけでなく、今後の課題も見つけられることがKPT最大のメリットです。
ロジックツリー
ロジックツリーとは、論理的思考のためのフレームワークです。
種類がいろいろありますが、特に業務改善に役立つのは「Whyツリー」で、問題を追求し原因を突き止めることを目的としています。
問題やそこから派生する要素をツリー状に書き出していき、真因を追求する手法です。業務改善では、問題や課題の洗い出しに役立ちます。
ECRS(イクルス)
ECRSとは、製造業で多く活用されている、業務フローの見直しに役立つフレームワークです。
- Eliminate(取り除く)
- Combine(まとめる)
- Rearrange(整理する)
- Simplify(単純化する)
この4つの手順に従って意見を出していくことで、業務フローの見直しなどの業務改善に役立てます。
シンプルな手法ですが、順序立てて業務改善案の立案ができるメリットがあります。
業務改善は事前準備と現状把握から始めることが大切(まとめ)
業務改善の方法は6ステップで取り組めますが、事前準備がとても大切です。
まずは、業務改善の最終的な目標であるQCDを満たして向上させることを念頭に置き、現場との共有を意識しながらの進行を心がけましょう。
業務改善の手順で特に大切なのは、最初のステップである「現状把握」です。現状把握では業務内容やフローの見える化を実施し、適切な問題や課題の洗い出しを行います。
その後は問題や課題の優先順位を付けて、業務改善方法の検討と計画作成、実施へと進んでいきます。
業務改善実施後は評価を行い、定着化を目指してルール化やマニュアル化の徹底など、日々工夫をしていきましょう。
業務改善の立案や実施には、今回ご紹介した具体例やフレームワークが、ご参考になればと思います。
今日のポイント
- 業務改善に取り組む前には目的の確認と現場との共有を心がけることが大切
- 業務改善は6ステップの手順で進めていき、特に最初の「現状把握」に重きを置く
- 製造業における業務改善の具体例やフレームワークは業務改善案の立案に役立つ
製造業のDXはあおい技研
株式会社あおい技研は、製造業に特化した業務改善コンサルティングを提供し、製造現場のDX推進をサポートします。80以上の製造現場での診断や改善の経験を活かし、お客様に合ったDX戦略を提案します。
データ分析、業務効率化システムの開発、現場のデジタル化などを通じて、お客様の業務改善と生産性向上を支援します。
製造業のDXについては、あおい技研にご相談ください。
関連記事
-
作業の効率化が進まない理由5つ!製造業における向上の事例も紹介
2023年9月12日
-
作業性を向上できる取り組み4つ|製造業における成功事例も紹介
2022年11月28日
-
在庫管理をバーコードでするメリット3つ!デメリットやエクセルで自作する方法も解説
2023年11月6日
-
7つのムダを初心者向けに徹底解説|それぞれの対処法や改善事例も紹介
2024年4月5日
-
製造業の見える化とは?意味と目指すメリット・実行する方法・事例をご紹介
2021年10月20日
-
工場を見える化する目的とメリット4つ!具体的な方法や事例・課題も解説
2022年7月1日
-
在庫管理を見える化する方法3つ|メリットとExcelの活用事例も
2022年4月1日
-
業務管理の基本6つを初心者向けに解説!理由や進め方・役立つツールも紹介
2022年8月30日
-
QCサークル活動の進め方|4つの基本要素と成功させるポイント
2021年12月24日
カテゴリー
- IT化
- QCD
- QCサークル
- コスト削減
- コンサルタント
- スマートファクトリー
- ボトルネック工程
- 中小企業
- 労働生産性
- 合理化
- 品質担保
- 品質管理
- 在庫管理
- 工場IoT
- 工場効率化
- 工程管理
- 工程管理システム
- 投入資源
- 業務効率
- 業務改善
- 生産ライン
- 生産性向上
- 生産管理
- 生産管理システム
- 経費削減
- 製造業
- 製造業 DX
- 製造業IoT
- 見える化
- 設備管理
新着コラム
-
2025年6月30日
産業用ロボットとは?サービスロボットとの違いや種類、導入するメリットを解説
-
2025年6月30日
工場の省人化に取り組むメリットを解説!具体的なステップと事例をご紹介
-
2025年6月30日
【産業用ロボット】主要メーカーの市場シェアはどれぐらい?市場規模などわかりやすく解説
-
2025年5月28日
事例から学ぶ工場の安全対策!製造業の労災件数も紹介
-
2025年5月28日
ベンダーコントロールとは?定義やToDoを解説
-
2025年5月28日
外部コンサルタントとは?内部との違いやメリット・デメリット
-
2025年4月25日
勘と経験に頼らないモノづくりとは?製造業10社のデータ活用事例を紹介
-
2025年4月25日
工程設計とは?フロー、重要さを解説【事例あり】
-
2025年4月25日
製造業の工程管理、うまくいかない?原因と解決策を解説
-
2025年3月24日
工程分析とは?使われる記号や手法、改善ポイントを解説