工場の省人化に取り組むメリットを解説!具体的なステップと事例をご紹介
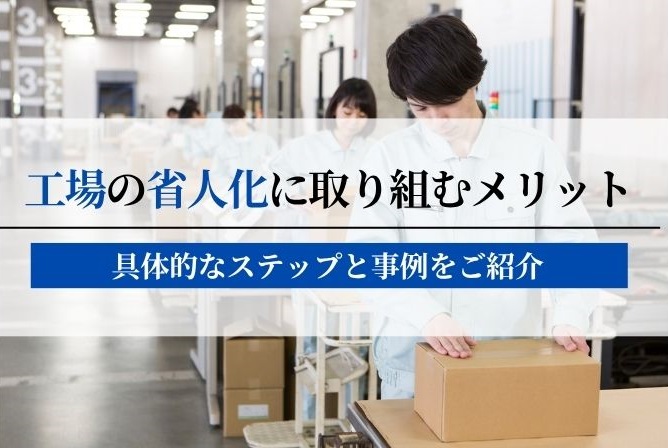
日本の製造業が直面する課題の一つが「人手不足」です。
少子高齢化が進み、労働力の確保が困難になる中、多くの企業が注目しているのが「省人化」の取り組みです。
省人化とは、単なる機械化や自動化ではなく、限られた人員でも高い生産性と品質を維持・向上させるための戦略的な取り組みを指します。
本記事では、省人化の基本的な考え方から導入のメリット、そして具体的な進め方を解説します。
さらに、実際に弊社あおい技研が手がけた省人化の成功事例もあわせてご紹介します。
コンテンツ
工場の省人化とは?
省人化とは、業務に従事する人員の数を減らしながらも、生産性や品質を維持・向上させる取り組みです。
工場においては、人が担っていた工程をロボットや自動化設備に置き換えることで、少人数でも安定した生産体制を構築することを目的とします。
背景には少子高齢化による人材不足や現場作業者の負担軽減といった課題があり、省人化はこれらの解決策として注目されています。
省人化を行うには工程の見直しやデジタル化、機器の導入が求められますが、企業全体の競争力向上にもつながります。
省人化と省力化の違いとは?
省人化とよく混同される概念に「省力化」がありますが、両者には明確な違いがあります。
省力化は作業効率を高め、従業員一人ひとりの負担を軽減することに主眼が置かれています。
例えば、重い荷物を運ぶ補助装置の導入や、作業工程の簡略化が該当します。一方で省人化は、人そのものを減らしても業務が成立する体制を目指すものです。
具体的には、工程を自動化し、人の作業をシステムや機械に置き換えることによって、人員削減を図ります。
工場の省人化に取り組むメリット
製造業が抱える課題を解決する手段として、省人化は非常に有効です。
人手不足の対応から生産性の向上、さらには組織全体の働き方改革まで、多方面にわたって効果が期待されます。
ここでは、省人化によって得られる主なメリットを4つの観点から詳しくご紹介します。
人手不足の対策
多くの製造業が直面しているのが「人手不足」の問題です。
特に少子高齢化が進む日本では、若手の確保が難しく、既存の労働力に頼りきる体制は限界を迎えつつあります。
省人化の導入により、業務の一部を自動化し、人の手を介さずに作業が進む体制を整えれば、限られた人員でも安定した生産が可能になります。
自動化により、採用にかかるコストや教育工数も削減でき、長期的な人材戦略にも良い影響を与えるのです。
従業員の生産性向上
省人化は、人手不足に対応するだけでなく、現場で働く従業員の生産性向上にも貢献します。
従来のように人手で対応していた反復作業や非効率な工程を自動化することで、従業員はより価値の高い業務に集中できるようになります。
例えば、不良品のチェックや単純な仕分け作業をAIやロボットが担うことで、作業者は改善活動や新製品開発など創造的な仕事に時間を割けるようになります。
結果として、工場全体の生産性向上が期待できます。
技術継承の効率化
製造業における長年の課題として、熟練工の退職による技術・ノウハウの継承があります。
属人化した作業は後継者育成に時間がかかり、効率的な技術継承が難しい状況です。
しかし、省人化の過程で工程を見える化・標準化し、システムやロボットに作業を引き継ぐことで、技術の再現性が高まり、教育コストを抑えながら次世代への伝承が可能になります。
省人化は、技術の形骸化を防ぎ、工場の持続可能性を高める一助となります。
働き方改革の推進
長時間労働や過酷な作業環境が問題視されてきた製造業において、省人化は働き方改革を進める有力な手段です。
機械化やシステム化により業務負担を軽減することで、労働時間の短縮や業務の効率化が進みます。
結果として、残業の削減や休日の確保が可能になり、従業員のワークライフバランスが改善されます。
また、多様な人材が活躍できる環境づくりにもつながり、企業の魅力向上と人材定着率の向上にも貢献します。
工場の省人化の具体的なステップ
工場の省人化を成功させるには、段階的に進めることが重要です。
省人化を実現するための4つのステップを紹介します。
・ステップ1:目的と課題の明確化
・ステップ2:現状把握
・ステップ3:作業の標準化・自動化の検討
・ステップ4:現場の運用定着
ステップ1:目的と課題の明確化
まず最初に行うべきは、なぜ省人化を進めるのかという目的の明確化です。
人手不足対策、コスト削減、働き方改革の推進など、企業によって目的は異なります。
また、同時に現場のどのような課題を解決したいのかを具体的に洗い出すことも重要です。目的や課題が曖昧なままだと、施策の優先順位や投資判断がぶれてしまい、効果的な施策が打てなくなります。
経営層から現場まで共通認識を持つことが、重要になります。
ステップ2:現状把握
次に取り組むのが、現場の現状把握です。
作業工程、工数、作業時間、担当者のスキルレベルなど、現場の詳細なデータを収集・分析します。
現状把握では、普段意識せずに行っている非効率な作業や重複している業務が明らかになることも少なくありません。
見える化によって課題が明確になることで、どの工程から改善を始めるべきか、どこに省人化の余地があるのかが判断しやすくなります。
ツールや業務日報を活用して、客観的に現状把握することが大切です。
ステップ3:作業の標準化・自動化の検討
現状の課題が見えてきたら、次は作業の標準化と自動化の検討に移ります。
まずは、属人化している作業や手順のバラつきを解消し、誰でも同じ成果が出せるような業務フローを整備します。
業務フローを作ることで、教育時間の短縮やミスの防止にもつながります。その上で、自動化可能な工程にはロボットなどの導入を検討します。
すべての工程を一度に自動化するのではなく、効果が大きく再現性の高い部分から段階的に導入するのが現実的です。
ステップ4:現場の運用定着
自動化の導入が終わっても、それで省人化が完了したわけではありません。最後に、新しい体制を現場に定着させる必要があります。
新しい設備やシステムを使いこなせるように教育・研修を行い、日々の運用に支障が出ないようサポート体制も整備します。
また、定着後も定期的な効果検証を行い、必要に応じて改善を続けることが求められます。現場の声に耳を傾け、実態に即した運用を継続することで、省人化の取り組みが形骸化せずに維持されていきます。
あおい技研の省人化事例
部品管理システムの確認時間を大幅削減
・対応したこと
株式会社Aでは、発注後の部品ステータスが把握できず、誤使用や請求確認ミスが多発していました。
弊社では、以下の3点を実施し省人化を支援しました。
①発注時に自動で部品番号を採番するシステム
②3枚綴りの専用納品書(納品書・検収書・現品票)の運用
③製造ライン情報を明記した現品票の貼付による識別強化
・効果
部品のステータスがリアルタイムで確認可能になり、回答時間を70%削減。
また、現品票によって部品の誤使用が防止され、倉庫やラインでの混乱も解消しました。
請求内容も検収書で明確になり、支払いの透明性が大きく向上しました。
ベテラン担当者の工程計画を95%再現
・対応したこと
鋳物製造を行う株式会社Dでは、工程計画がベテラン担当者の経験と勘に依存しており、技能継承や若手への引き継ぎに課題がありました。
そこで、弊社では以下3点を中心に工程計画システムを企画・開発しました。
①幾何計算を自動で行うエンジンの構築
②熱処理パターンの自動化機能の実装
③熱処理に連動した前後工程の調整機能の整備
・効果
これらシステムにより、ベテラン担当者の計画内容を95%の精度で再現可能に。
工程計画の属人化を解消し、若手でも安定した工程管理が行えるようになりました。
また、納期予測の精度も向上し、経営判断に活用できる点も高く評価されています。
まとめ
工場の省人化は、ただ人を減らすだけでなく、生産性向上・人手不足対策・技術継承の効率化・働き方改革といった多くの課題解決に貢献する重要な施策です。
導入にあたっては、目的の明確化から現状把握、標準化・自動化の検討、そして現場への定着という段階を踏むことが成功の鍵となります。
さらに、実際の企業の取り組みからは、システム導入による確認作業の削減やベテランの技術継承など、成果につながる具体的なヒントも得られます。
製造現場の将来を見据えた持続可能な改革として、省人化の取り組みを積極的に進めていきましょう。
製造業のDXはあおい技研
株式会社あおい技研は、製造業に特化した業務改善コンサルティングを提供し、製造現場のDX推進をサポートします。80以上の製造現場での診断や改善の経験を活かし、お客様に合ったDX戦略を提案します。
データ分析、業務効率化システムの開発、現場のデジタル化などを通じて、お客様の業務改善と生産性向上を支援します。
製造業のDXについては、あおい技研にご相談ください。
関連記事
-
業務改革(BPR)の進め方と成功のポイント3つ【業務改善との違い】
2024年1月15日
-
業務標準化の事例5選!目的・進め方・メリット・デメリットを徹底解説
2024年9月2日
-
IoTの活用事例7つを厳選して徹底解説【企業や工場】
2023年6月30日
-
スマートファクトリーとは?簡単に5つの事例を交えながら紹介|ロードマップも解説
2023年7月3日
-
製造業のIoT成功事例7つ!導入するメリットや課題もご解説
2022年4月12日
-
インダストリアルエンジニアリングとは?初心者向けに手法3つと役立つ資格を徹底解説
2024年2月20日
-
工程分析とは?使われる記号や手法、改善ポイントを解説
2025年3月24日
-
QCDとは?初心者向けに4つのポイントで重要な理由や関係性を解説!
2022年9月20日
-
改善のフレームワーク7選|ECRSやKPTなど役立つアイデアを初心者向けに徹底解説
2023年4月17日
カテゴリー
- IT化
- QCD
- QCサークル
- コスト削減
- コンサルタント
- スマートファクトリー
- ボトルネック工程
- 中小企業
- 労働生産性
- 合理化
- 品質担保
- 品質管理
- 在庫管理
- 工場IoT
- 工場効率化
- 工程管理
- 工程管理システム
- 投入資源
- 業務効率
- 業務改善
- 生産ライン
- 生産性向上
- 生産管理
- 生産管理システム
- 経費削減
- 製造業
- 製造業 DX
- 製造業IoT
- 見える化
- 設備管理
新着コラム
-
2025年7月30日
工場の労働環境を改善するための具体策とは?改善のステップや事例もご紹介
-
2025年7月30日
工場の暑さ対策を徹底解説!2025年義務化対応と効果的な対策とは?
-
2025年7月30日
工場の5S活動とは?生産性と安全性を高める改善の進め方
-
2025年6月30日
産業用ロボットとは?サービスロボットとの違いや種類、導入するメリットを解説
-
2025年6月30日
工場の省人化に取り組むメリットを解説!具体的なステップと事例をご紹介
-
2025年6月30日
【産業用ロボット】主要メーカーの市場シェアはどれぐらい?市場規模などわかりやすく解説
-
2025年5月28日
事例から学ぶ工場の安全対策!製造業の労災件数も紹介
-
2025年5月28日
ベンダーコントロールとは?定義やToDoを解説
-
2025年5月28日
外部コンサルタントとは?内部との違いやメリット・デメリット
-
2025年4月25日
勘と経験に頼らないモノづくりとは?製造業10社のデータ活用事例を紹介