工場診断で何がわかる?課題の「見える化」の大切さを解説
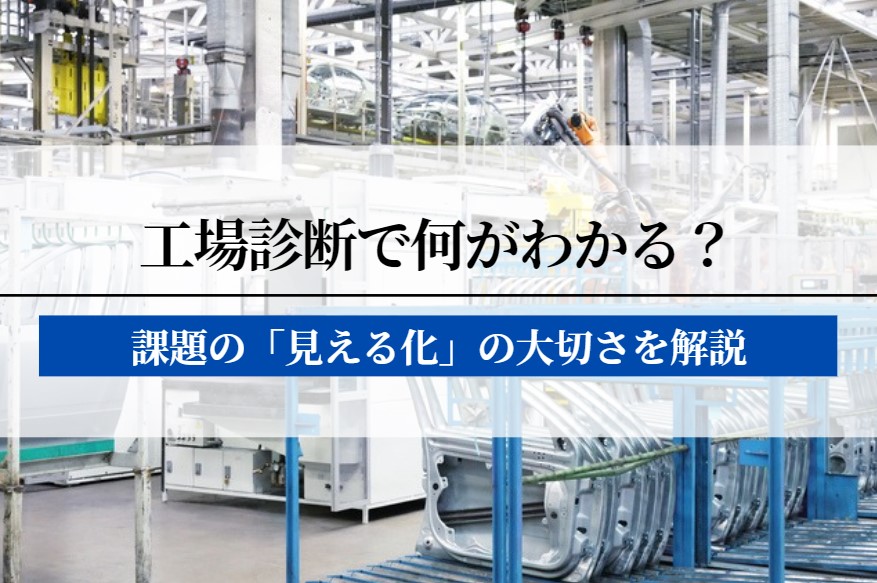
工場診断とは、分析した稼働状況や生産プロセスから課題点を見つけ、改善するための取り組みです。
診断では、コンサルタントや診断士が工場を訪問して、生産ラインや作業フロー、設備の稼働状況をチェックします。
古い設備が効率を下げている、動線に無駄があるといった課題を発見し、改善策を提示するのが主な流れです。
「工場の健康診断」と捉えるとイメージしやすいでしょう。
工場診断の主な目的は、工場運営の「見える化」と「効率化」です。
「問題があるならどう直せばいいのか?」を専門家とともに考えることで、パフォーマンスの最大化を図っているのです。
コンテンツ
工場診断の項目
生産戦略
製品や技術、人材、設備が経営目標に沿って適切に活用されているかを評価します。
要するに、「この工場が何を作りたいのか」「それを作るためにどんな技術や設備が必要なのか」「人材がちゃんと揃っているのか」を見ます。
場当たり的な対応ではなく、長期的な視点での方向性が明確かもチェックポイントです。
【課題の例】
・新製品を作りたいけど、現場の設備が古すぎて対応できない
・優秀な人材が辞めてしまう、定着率が低い
品質管理
製造工程全体での品質管理が徹底されているかを確認します。
特に、各工程で設定された品質基準を満たしているか、問題が発生した際の対応方法を評価します。
【課題の例】
・検査はしているが、不良品が見逃される
・不良品が出ても原因がわからない
モノの流し方
原材料から製品が完成するまでの「流れ」が効率的かどうかを診断します。
材料の供給、作業工程間の連携、そして完成品の配送までを見直します。
【課題の例】
・材料が届くタイミングがバラバラで、無駄な待ち時間が発生している
・完成品が倉庫に溜まりすぎて邪魔になっている
作業効率
作業員の動きや機械の稼働状況をチェックし、無駄な動きや手待ち時間が発生していないかを確認します。
個人の経験や感覚に頼らず、誰がやっても同じ結果になるように仕組みを標準化するのが目的です。
【課題の例】
・同じ作業を複数人が重複して行っている
・必要な工具や部品が適切な場所に配置されておらず、移動に時間がかかる
工場レイアウト
工場内の設備や作業ラインの動線が最適化されているかをチェックします。
適切なレイアウトは、作業効率の向上だけでなく従業員の負担軽減や安全性の向上にもつながります。
【課題の例】
・作業エリアと保管エリアが遠く、移動に無駄が多い
・通路近くに機械があり危険
5S
製造業でよく用いられる「5S」とは「整理・整頓・清掃・清潔・躾(しつけ)」のこと。
工場全体の効率・安全性を高めるための基本的な活動ができているかをチェックします。
【課題の例】
・道具が整理されておらず、必要な物を探す時間がかかる
・作業場に不要な物が散乱し、動線が妨げられている
工場診断を依頼するメリット
課題がわかる
「自分の工場が抱えている課題が明確にわからない」
そんな悩みを持つ経営者は少なくありません。
工場診断では、第三者の視点から現状を分析し、課題を「見える化」することができます。
例えば、生産工程に無駄がある、作業効率が低いなど普段は気づきにくい問題点を専門のコンサルタントが客観的に指摘します。
この「気づき」がなければ、課題解決に向けた第一歩は踏み出せません。
診断を通じて自分たちの工場の現実を知れるのは、大きな価値と言えます。
課題の解決策がわかる
課題がわかったとしても、「次にどうすれば良いのか」が見えないと解決にはつながりません。
工場診断では、専門コンサルタントが課題に対する具体的な解決策を提案してくれます。
例えば、生産フローの再構築や機械の配置転換など現状や経営目標に基づいたアドバイスが得られます。
「問題が明らかになっただけ」で終わらず、その先の道線まで示してもらえることがメリットです。
パフォーマンスの最大化につながる
工場診断を受けることで、課題とその解決策がわかるとお伝えしました。
課題が一つひとつ解決されることで、生産ライン全体がスムーズに動くようになり、従業員の働きやすさも向上します。
また余計なコストが削減されることで、利益率の改善にも寄与します。
こうした改善が積み重なることで、結果として工場全体のパフォーマンスが向上するのです。
経営戦略の明確化
工場診断は、単に現場の効率を改善するだけではなく、経営戦略にも役立ちます。
診断結果を踏まえた上で、どの製品に注力すべきか、どの市場に進出すべきかといった経営判断の材料になるためです。
また、診断を受けることで、経営者自身が自社の課題や強みを再確認する機会にもなります。
現場と経営の両面から見直す工場診断は、成長を目指す企業にとって非常に重要な情報なのです。
お試し工場診断ならあおい技研
あおい技研は、製造業に特化した業務改善コンサルティング会社です。
製鉄や組立て系産業、食品、医療機器、化学系素材など携わってきた現場は80以上。
もちろん、お試し工場診断も承っております。
【実績】
・工場構内の物流改善
・各種工程の分析、作業改善のご提案
・労働生産性の向上
・製造ライン増設や工場リプレースにかかるレイアウト検討、シミュレーション
ものづくりの仕事では、一つひとつの現場に違った課題、難しさがあるもの。
「○○方式」といった一律の方法だけを提案するのでは、本質的な問題解決にはなりません。
私たちは現場の「かかりつけ医」として、データ分析を基にした仮説と施策を打ち出します。
業務改善やコスト削減など、ものづくりの現場ならではのお悩みをぜひご相談ください。
まとめ
工場診断は、第三者の視点で現場の課題を洗い出し、一つずつ解決していくためにあります。
主な診断項目は、生産戦略、品質管理、モノの流し方、作業効率、5S。
それぞれの課題を改善し続けることで、パフォーマンスの最大化を図れます。
「今のままじゃまずい」と感じているなら、工場診断を受けるタイミングかもしれません。
お試し工場診断なら、製造業のかかりつけ医「あおい技研」にお任せください。
製造業のDXはあおい技研
株式会社あおい技研は、製造業に特化した業務改善コンサルティングを提供し、製造現場のDX推進をサポートします。80以上の製造現場での診断や改善の経験を活かし、お客様に合ったDX戦略を提案します。
データ分析、業務効率化システムの開発、現場のデジタル化などを通じて、お客様の業務改善と生産性向上を支援します。
製造業のDXについては、あおい技研にご相談ください。
関連記事
-
生産性が製造業で最も重要である理由5つ|工場の生産性向上の事例も掲載
2023年8月4日
-
勘と経験に頼らないモノづくりとは?製造業10社のデータ活用事例を紹介
2025年4月25日
-
工場の稼働率を上げるには?有効な方法3つと計算式の求め方や目安を解説
2023年10月13日
-
工場のヒヤリハットの原因4つ!対策と改善案のネタ切れに役立つ事例も紹介
2024年4月5日
-
製造管理システムとしてMESを導入するメリット4つ|生産管理システムとの違いも解説
2024年1月15日
-
工場の設備管理はきつい?求人・資格・年収の3つの観点から徹底解説
2023年12月12日
-
工場の動線を安全に確保するための手順を3ステップで紹介!レイアウト図の書き方も
2023年8月4日
-
工程設計とは?フロー、重要さを解説【事例あり】
2025年4月25日
-
合理化と効率化の違いをわかりやすく解説|それぞれの取り組み例5つ
2024年4月5日
カテゴリー
- IT化
- QCD
- QCサークル
- コスト削減
- コンサルタント
- スマートファクトリー
- ボトルネック工程
- 中小企業
- 労働生産性
- 合理化
- 品質担保
- 品質管理
- 在庫管理
- 工場IoT
- 工場効率化
- 工程管理
- 工程管理システム
- 投入資源
- 業務効率
- 業務改善
- 生産ライン
- 生産性向上
- 生産管理
- 生産管理システム
- 経費削減
- 製造業
- 製造業 DX
- 製造業IoT
- 見える化
- 設備管理
新着コラム
-
2025年7月30日
工場の労働環境を改善するための具体策とは?改善のステップや事例もご紹介
-
2025年7月30日
工場の暑さ対策を徹底解説!2025年義務化対応と効果的な対策とは?
-
2025年7月30日
工場の5S活動とは?生産性と安全性を高める改善の進め方
-
2025年6月30日
産業用ロボットとは?サービスロボットとの違いや種類、導入するメリットを解説
-
2025年6月30日
工場の省人化に取り組むメリットを解説!具体的なステップと事例をご紹介
-
2025年6月30日
【産業用ロボット】主要メーカーの市場シェアはどれぐらい?市場規模などわかりやすく解説
-
2025年5月28日
事例から学ぶ工場の安全対策!製造業の労災件数も紹介
-
2025年5月28日
ベンダーコントロールとは?定義やToDoを解説
-
2025年5月28日
外部コンサルタントとは?内部との違いやメリット・デメリット
-
2025年4月25日
勘と経験に頼らないモノづくりとは?製造業10社のデータ活用事例を紹介