工場内物流(構内物流)改善のポイントと手法を解説
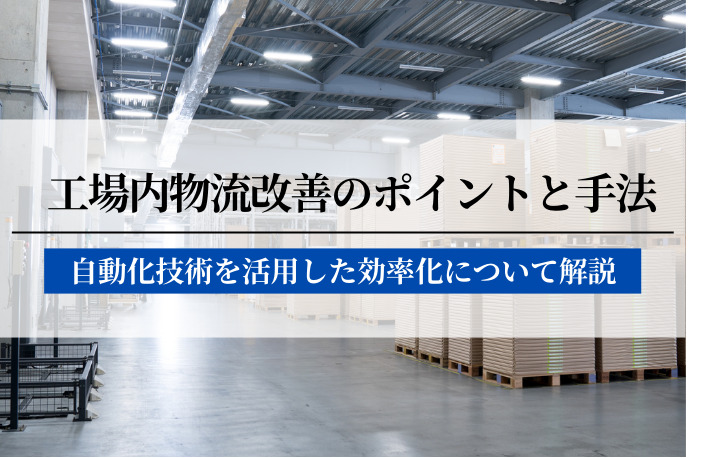
工場内物流(構内物流)の改善は、製造現場の効率化とコスト削減を図るために必要な作業です。
工場内物流は、製品の製造に必要な資材の調達、製品の保管、ピッキング、搬送、出荷といった工程で成り立っており、それぞれの段階で効率的な流れが求められます。
工場内の物流フローの効率化は、物流の品質向上と出荷の迅速化にもつながります。
本記事では、工場内物流の役割や改善のポイントを解説し、自動化ツールの導入事例についても紹介します。
コンテンツ
工場内物流とは?
工場内物流の概要と役割
工場内物流とは、工場内で資材や部品、製品を移動・運搬する業務全般を指します。
製造ラインや工程間で効率的にモノを供給することが、生産性向上に繋がる重要な業務です。
工場内物流が適切に管理されていない場合、生産の滞りやコスト増加を引き起こすことがあります。
そのため、物流業務を効率化することで、工場全体の生産性や品質の向上を目指します。
※「工場内物流」は「構内物流」とも称されることがあります。
工場内物流の種類
工場内物流には主に以下の3つの種類があります。
1. 調達物流
調達物流は、必要な原材料や部品を仕入先から調達し、工場内に搬入する工程を指します。
近年では「ジャストインタイム化」が進み、必要なものを必要な時に供給する効率的な管理が求められています。
2. 販売物流
販売物流は、工場で生産された製品を得意先や配送センター、小売店、消費者へ届ける工程を指します。
EC市場の拡大に伴い、消費者に直接配送するケースも増え、迅速かつ柔軟な対応が求められる分野です。
3. 回収物流
回収物流は、不良品や使用済み製品の回収、リサイクルの工程を指します。
持続可能な社会の実現が求められる昨今、回収物流の効率化や循環型物流の導入が課題となっています。
さらに、回収した製品はリサイクル原料やパーツとして再利用され、環境負荷の低減と資源の有効活用につながります。
工場内物流の工程
工場内物流の工程には、「受け入れ・入庫」→「ピッキング」→「搬送」→「出荷(準備)」の順番になっています。
ここでは、工場内物流の工程について詳しく解説します。
1. 受け入れ・入庫
工場内物流の最初の工程は、物品の受け入れと入庫です。
製品や材料が外部から工場に届いた際、まずその内容を確認し、数量や品目の誤りがないかを検品します。
その後、適切な保管場所を特定し、在庫管理システムに登録して入庫処理を行います。
この工程では、スムーズな作業と正確な記録が物流全体の効率を大きく左右します。
2. ピッキング
ピッキングは、必要な製品や材料を保管場所から取り出す工程です。
出荷や製造ラインへの供給のため、注文書や作業指示書に基づいて、品目や数量を正確に揃えることが求められます。
効率を高めるために、ピッキングリストのデジタル化やウェアラブルデバイスを活用した作業指示が一般化しています。ピッキングミスを防ぐことで、次工程のスムーズな進行に寄与します。
3. 搬送
搬送は、ピッキングされた物品を目的地まで移動させる工程です。
工場内では、フォークリフトやコンベヤーなどが使用される場合が多く、これらの機器を活用することで作業効率が向上します。
また、物品の移動中に発生する可能性のある損傷を防ぐため、適切な梱包や運搬方法を徹底することが重要です。
4. 出荷(準備)
出荷準備は、工場から出荷される製品を整える工程です。
ピッキングや搬送を経て集められた物品を梱包し、出荷先ごとに仕分けを行います。その際、配送ラベルの貼付や出荷リストの作成を行い、配送業者への引き渡し準備を整えます。
出荷の工程では、時間の厳守と正確な対応が求められます。特に複数の出荷先がある場合は、物流管理システムを活用して作業を効率化し、ミスを防止します。
工場内物流改善の4ステップ
1. 工場内物流の実態把握
工場内物流を改善するための第一歩は、工場内物流の実態を正確に把握することです。
この工程では、物流フロー全体を観察し、データを収集・分析をして現場の状況を把握します。
具体的には、工場の現地調査や作業者へのヒアリングを通じて、実務で感じる非効率な部分や改善の余地を確認します。
工場の実態把握を徹底することで、次のステップへ移ることができます。
2. 現状課題の洗い出しと分析
改善の第一歩は、工場内物流における現状の課題を明確にすることです。
不必要な搬送や在庫管理の不備、作業者の負担など、物流フロー全体を把握し見直します。
問題点を洗い出し、データに基づいて原因を分析することで、改善の優先順位を明確化できます。
3. 「ECRS」手法によるムダ削減
「排除、結合、交換、簡素化」を示すECRS手法を活用し、作業のムダを徹底的に見直します。
不要な作業を排除し、複数の工程を結合することで効率化を図ります。
具体的には、重複した在庫確認作業の排除やピッキング、検品作業の結合、手作業での記録をデジタルツールへ移行など、作業手順の簡素化などを実施します。
参考元:ECRS(改善の4原則)|日本能率協会コンサルティング
4. 工場内の効率化を行う
課題分析とECRS手法を活用したムダ削減を経たら、次は工場内物流のさらなる効率化を行います。
効率化には、デジタルツールの導入や設備の再配置、人員配置の見直しなど、さまざまな取り組みが必要になります。
例えば、倉庫管理システムを活用することで、リアルタイムで在庫や搬送状況を把握できます。
作業者が効率よく必要な物品を管理し、無駄な動きを削減することが可能です。
一方で、大幅な工場レイアウトの変更やAGV(無人搬送車)の導入といった設備投資を伴う場合、慎重な計画立案が求められます。このようなケースでは、レイアウト変更や物流改善に関する専門的な知見が必要となるため、シミュレーションや物流改善を得意とする外部コンサルタントの活用を検討しましょう。
設備配置や搬送経路の最適化を実現することで、投資効果の最大化が期待できます。
工場内物流改善の事例
事例①:AGV・AMRなど搬送ロボット
ダイキン工業では、物流倉庫にハンドリフト牽引型の自動搬送装置(AGV)を導入し、入出庫作業の効率化を実現しました。
AGVは、磁気テープに沿って目的地まで荷物を無人で搬送し、最長往復約500mに及ぶ搬送作業の負担を軽減します。タブレット端末で簡単に行先を指示できるため、運用もスムーズです。
さらに、最大500kgの荷物を搬送可能な性能や長時間稼働を支えるカスタマイズされたバッテリーシステムにより、生産性が向上。導入の結果、作業負担の軽減だけでなく、生産性が15%向上し、従業員2名相当の省人化も達成しました。
事例②:無線通信自動認識システム(RFID)と仕分けシステムの事例
佐川グローバルロジスティクスでは、「無線通信自動認識システム(RFID)」と「仕分けシステム・t-Sort」を組み合わせ、入出庫検品作業と仕分け作業の生産性向上を図っています。
RFIDによる自動認識により検品作業の効率が向上し、仕分けミスもほぼゼロに。新規就労者の戦力化や作業スキルの修得時間が約7割削減されるなど人材育成においても効果が高まっています。
事例③:物流センターで保管・ケース、ピッキング業務の自動化
トランコムでは、物流センターにおける労働力不足や重筋作業の課題を解決するため、有軌道無人搬送台車(RGV)や搬送ロボット(AGV/AGF)を導入しました。これらを導入することにより、保管やケース単位でのピッキング業務を自動化し、効率的な物流オペレーションを実現しています。
RGVは倉庫内の上部空間を活用して保管効率を向上させ、AGVは床上での物品搬送を無人化。さらに、異なる荷姿にも対応可能なピッキングロボットを活用することで、柔軟で精度の高い作業が可能になりました。
導入結果として、大幅な省人化を実現するとともに、1/3のコストで倉庫内スペースの有効活用を達成しました。
参考元:国土交通省「物流DX導入事例集」
工場内物流の改善はあおい技研
株式会社あおい技研は、製造業に特化した業務改善コンサルティングを提供し、製造現場の業務改善をサポートします。
80以上の製造現場での診断や改善の経験を活かし、お客様に合った工場内物流改善を提案します。
工場内物流の改善以外にもデータ分析やシステムの開発、現場のデジタル化などを通じて、お客様の業務改善と生産性向上を支援します。
製造業の業務改善については、あおい技研にご相談ください。
本日のポイント
- 工場内物流は、調達・保管・搬送・出荷など複数の工程から構成され、生産性向上の要となります。
- 効率化の第一歩は課題の明確化と分析。ECRS手法でムダを削減し、作業改善を進めることが重要です。
- 新しい技術の導入で、AGVやRFID、ピッキングロボットが生産性向上と省人化を実現します。
- 成功事例として、AGVの活用で15%の生産性向上やRFIDによる検品効率化が挙げられます。
- 継続的な改善活動とPDCAサイクルの実践が、長期的な効率化とコスト削減につながります。
製造業のDXはあおい技研
株式会社あおい技研は、製造業に特化した業務改善コンサルティングを提供し、製造現場のDX推進をサポートします。80以上の製造現場での診断や改善の経験を活かし、お客様に合ったDX戦略を提案します。
データ分析、業務効率化システムの開発、現場のデジタル化などを通じて、お客様の業務改善と生産性向上を支援します。
製造業のDXについては、あおい技研にご相談ください。
関連記事
-
工程管理の基本を3つの項目で徹底解説【工程管理表の作成方法も】
2022年3月28日
-
生産性向上の代表的な課題5つと対処法|製造業における重要性
2024年6月13日
-
業務効率化ツールを選ぶときのポイント5つ!エクセルで自作するのはあり?
2023年3月20日
-
工場を効率化する事例10個【製造業の小さな改善アイデア】
2022年4月28日
-
工場のヒヤリハットの原因4つ!対策と改善案のネタ切れに役立つ事例も紹介
2024年4月5日
-
産業用ロボットとは?サービスロボットとの違いや種類、導入するメリットを解説
2025年6月30日
-
在庫管理をバーコードでするメリット3つ!デメリットやエクセルで自作する方法も解説
2023年11月6日
-
製造業のIoT成功事例7つ!導入するメリットや課題もご解説
2022年4月12日
-
業務管理の基本6つを初心者向けに解説!理由や進め方・役立つツールも紹介
2022年8月30日
カテゴリー
- IT化
- QCD
- QCサークル
- コスト削減
- コンサルタント
- スマートファクトリー
- ボトルネック工程
- 中小企業
- 労働生産性
- 合理化
- 品質担保
- 品質管理
- 在庫管理
- 工場IoT
- 工場効率化
- 工程管理
- 工程管理システム
- 投入資源
- 業務効率
- 業務改善
- 生産ライン
- 生産性向上
- 生産管理
- 生産管理システム
- 経費削減
- 製造業
- 製造業 DX
- 製造業IoT
- 見える化
- 設備管理
新着コラム
-
2025年8月27日
HACCP 7原則12手順で守る「食の安全」!
-
2025年8月27日
GMP認定で支える「安全性」!製造の信頼は工程から始まる
-
2025年7月30日
工場の労働環境を改善するための具体策とは?改善のステップや事例もご紹介
-
2025年7月30日
工場の暑さ対策を徹底解説!2025年義務化対応と効果的な対策とは?
-
2025年7月30日
工場の5S活動とは?生産性と安全性を高める改善の進め方
-
2025年6月30日
産業用ロボットとは?サービスロボットとの違いや種類、導入するメリットを解説
-
2025年6月30日
工場の省人化に取り組むメリットを解説!具体的なステップと事例をご紹介
-
2025年6月30日
【産業用ロボット】主要メーカーの市場シェアはどれぐらい?市場規模などわかりやすく解説
-
2025年5月28日
事例から学ぶ工場の安全対策!製造業の労災件数も紹介
-
2025年5月28日
ベンダーコントロールとは?定義やToDoを解説