QC7つ道具を初心者向けに解説!覚え方や使い方を5ステップで紹介
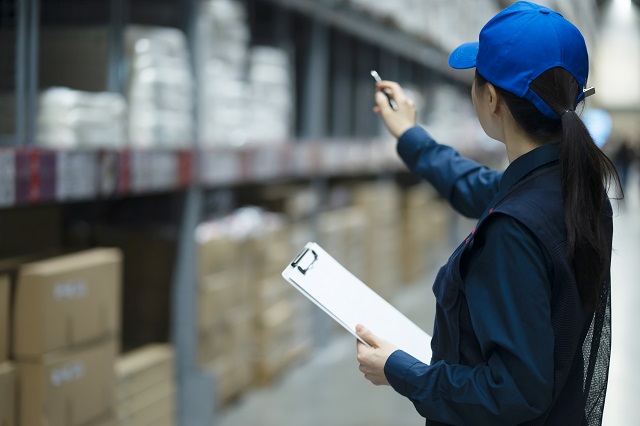
QC7つ道具は、製造現場のデータの整理や関係性の分析に役立つ、代表的な手法です。7つの手法を必要に応じて使うことで、製造現場の課題や問題を浮き彫りにします。QC7つ道具は、多くの製造現場で実際に使われている画期的な手法です。しかし、その基本と活用法を知らなければ、どのタイミングで導入すればいいのかわからず、困ってしまいます。
そのためQC7つ道具を活用するには、基本と活用法を身につけ、見落としがちな問題の発見や改善に役立てることが大切です。今回は、QC7つ道具について初心者向けに解説します。覚え方や新QC7つ道具との違い、活用法も詳しく紹介するため、ご参考にしてください。
コンテンツ
QC7つ道具とは
QC7つ道具は、特に製造業の品質管理やその改善に役立ちます。品質管理が徹底されていれば、製品の質が一定に保たれるため、不良品の発生率が低く、納期遅れが生じるリスクも下がります。そのため製造業にとって品質管理は、欠かせない重要な要素の一つです。QC7つ道具は、品質管理の実践に活用できるベーシックな手法です。
QC7つ道具は言葉の通り、以下の7つの道具(手法)のことを指します。
- パレート図
- 特性要因図
- グラフ
- ヒストグラム
- 散布図
- 管理図
- チェックシート
これらの手法を使って、製造現場のデータを整理・分析すると、隠れていた課題や問題が明確になります。QC7つ道具での分析は、課題や問題を「見える化」するだけでなく、原因究明や改善策を講じることにも役立ちます。
各手法について、それぞれ具体的に解説します。
パレート図
パレート図とは、対象項目を降順に並べた棒グラフと、各項目が全体に占める割合を、累積折れ線グラフで同時に表示する図のことです。パレート図を用いると、全体の中で大きな割合を占めている項目が明確になります。どの項目が最も結果に対する影響度(重要度)が高いのかを把握することが出来ます。
パレート図の活用例
横軸の項目に、研磨、溶接、塗装など製造工程を入力
↓
縦軸には不良品発生数の数値を入れる
結果:どの工程が全体の不良品発生数に対して大きく影響しているのかわかる
特性要因図
特性要因図とは、ある特性(結果)に至った要因を書き出していくことで、原因究明をしていく図のことです。魚の骨のような図になることから、フィッシュボーン図またはフィッシュボーンチャートとも呼ばれています。
特性要因図の活用例
「事故の発生」という特性を設定
↓
至った大きな要因を書き出す(人、設備、方法など)
↓
大きな要因の下に、それぞれの細かい要因を書き出していく
人:新入社員のミス、残業勤務中の疲労
設備:メンテナンス不足、老朽化 など
結果:特性に至った要因を体系的に書き出していくことで、主な原因が発覚する
原因に対する改善案を講じやすくなる
グラフ
- 棒グラフ…数量を比較できる
- 円グラフ…比率がわかる
- 帯グラフ…比率を比較できる
- 折れ線グラフ…変動がわかる
- レーダーチャート…バランスがわかる
一つのグラフだけを使うのではなく、あえて同じデータを使用し、複数のグラフを使ってみると、違う気づきを得られることもあります。複雑な数値データを、誰が見てもわかるように表示できます。
グラフの活用例
円グラフを用いて、複数の仕入先の会社名と各納入数を入力
結果:どの会社からどのくらいの比率で原材料を仕入れているのかが一目でわかる
ヒストグラム
ヒストグラムとは、データを一定ごとの範囲に区切り、それぞれの度数を表にまとめ、棒グラフにしたものです。測定したデータの分布状態やピーク値、ばらつきなどを把握できるため、課題や問題の発見に役立ちます。
ヒストグラムの活用例
横軸に機械設備がエラーを起こしてから何日で復旧したかの所要日数を入力
↓
縦軸にはエラーの件数を入力
結果:機械設備にエラーが発生してから復旧するまでの所要日数の分布状態、ピーク値、ばらつきなどがわかる
散布図
散布図とは、1つの事柄を2つの項目で表し、相関性がわかるようにする図のことです。2つの項目をそれぞれ縦軸・横軸にとり、相関性を点の集合で表します。2つの項目の間にある相関性や因果関係の確認に利用できます。
散布図の活用例
縦軸に不良品数、横軸に加工速度を入力
結果:加工速度が上がるほど不良品の発生率が高くなる、などの相関性がわかる
管理図
管理図とは、主に工程管理に使われる図です。中心線に目標値、上下線に上方管理限界線(UCL)と下方管理限界線(LCL)を配置して、データを時系列で折れ線グラフとして入力します。正常値と管理外れの、頻度や変化点や傾向などが明確になります。
管理図の活用例
縦軸に不良品数、横軸に日付を入力して折れ線グラフで表示
結果:変化がどこで起きているのかがわかる
なぜそのタイミングで起きるのかを追求することで改善案を講じられる
チェックシート
チェックシートとは、項目ごとにデータを記入していくシートのことです。定形様式はなく、使いやすいように自由に作成できます。チェックシートは主に、「点検用」と「記録用」があります。
点検用チェックシートは、点検項目の抜け・漏れなどを防止することが目的です。チェックボックスにチェックを入れるだけの、かんたんな様式になります。記録用チェックシートは、データ収集が目的です。項目ごとに日付や時間、件数などを書いて集計します。
チェックシートの活用事例
機械設備の点検項目を全て書き出し、チェックボックスを設ける
結果:点検の抜け・漏れがなくなり、新入社員でもマニュアルを確認せずに済む
QC7つ道具の覚え方
QC7つ道具を全て覚えるのは、少し難しいかもしれません。おすすめは、語呂合わせで暗記することです。野球やサッカーの外国人監督をイメージし、以下のように「サンチェ監督(チームを)引っ張れそう」という覚え方をしてみてください。
【サン(散布図)チェ(チェックシート)監(管理図)督(特性要因図)引(ヒストグラム図)っ張れ(パレート図)そう(層別・グラフ)】ユニークな覚え方ですが、QC検定を受けるときなどに役立ちます。
新QC7つ道具とは
新QC7つ道具とは、主に言語データをわかりやすく、図や表に整理・分析する手法のことです。QC7つ道具の後に補完的な手法として台頭したため、「新」が付いています。新QC7つ道具は、以下の7つの道具(手法)のことを指します。
- 親和図法
- 連関図法
- 系統図法
- マトリックス図法
- アローダイアグラム
- PDPC法
- マトリックスデータ解析法
QC7つ道具との違い
QC7つ道具との違いは、扱うデータにあります。QC7つ道具が扱うのは数値データで、新QC7つ道具が扱うのは言語データです。QC7つ道具は製造現場で実測したデータを分析するため、主に製造現場だけで活用されてきました。
一方で、新CQ7つ道具は数値化が難しい問題を解決できる手法として、製造現場に限らず企画・設計・営業などの分野で、改善活動に活用されています。QC7つ道具は新QC7つ道具に比べて、古い、劣っている、使えないというイメージを持たれがちですが、決してそんなことはありません。あくまで両者は補完的な関係性であり、扱うデータによって使うべき手法が違ってきます。
QC7つ道具の使い方【5ステップで紹介】
QC7つ道具を活用する場合は、QCストーリーに沿って活用していきます。QCストーリーとは、品質管理における問題解決を手順化したものです。複数のステップを順番に進めていくことで、問題解決をスムーズに実現できます。
ここからは、例として「不良品が多く発生している原因の追求と改善をしたいとき」のQC7つ道具の使い方を解説していきます。今回は製造現場の数値データを分析するため、新QC7つ道具は使用せずに、QC7つ道具を活用して解析するものとします。
1.現状把握
まずは、不良品がどのタイミングでどのくらい発生しているのかなど、現状把握を行います。チェックシートで不良品の数を集計し、パレート図を用いて、どの工程が全体の不良品発生数に対して大きく影響しているのかを把握しましょう。
ヒストグラムも使うと、不良品発生の分布状態やピーク値、ばらつきなどを把握できるため、より細かい条件を分析できます。
このステップで活用できるQC7つ道具:チェックシート、ヒストグラム、パレート図
2.要因の解析
現状把握の後は、なぜそうなったのか(その条件下で不良品が発生してしまうのか)の要因解析を行います。折れ線グラフで変動を見える化したり、いろいろな項目で散布図を作り、複数の条件の相関性を分析したりしてみましょう。特性要因図を使えば、最も大きな要因を探し出すことができ、改善案も講じやすくなります。
このステップで活用できるQC7つ道具:散布図、特性要因図、グラフ
3.改善案の実施
不良品発生の現状把握と要因解析ができたら、改善案を立てて実施します。
改善案と改善活動の例
原因:従業員の過労働による疲労
改善案:人員配置を見直して一人あたりの負担を軽減
作業場の整理整頓を徹底して非効率な時間を削減 など
改善案の実施には、チェックシートが役立ちます。点検チェックシートで新たな業務の抜け・漏れを防いだり、記録チェックシートで生産量をリアルタイムで可視化したりといった活用法があります。
このステップで活用できるQC7つ道具:チェックリスト
4.改善効果の確認
改善活動の後は、必ず効果を確認・評価しなくてはいけません。体感ではなく、数値データとして客観的に、効果を測定できるようにしましょう。改善効果の確認には、パレート図、ヒストグラム、グラフが役立ちます。改善取り組み前後を比較して、問題点が解消されたかを確認しましょう。
このステップで活用できるQC7つ道具:パレート図、ヒストグラム、グラフ
5.維持管理
最後は、問題解消した状態を、維持管理していくステップです。維持管理には、管理図が役立ちます。製品の品質が管理限界線内に収まっているか確認しながら、継続的な維持管理を行っていきましょう。
このステップで活用できるQC7つ道具:管理図
QC7つ道具は製造業の改善活動に欠かせない手法(まとめ)
QC7つ道具は、製造業の品質管理に役立つ手法です。7つの図やグラフ、シートを必要に応じて使うことで、製造現場の課題や問題を浮き彫りにします。
ポイントは、QC7つ道具の役割は、課題や問題を明確にするだけではないことです。課題や問題を「見える化」するだけでなく、原因究明や改善策の立案にも活用できます。新QC7つ道具との違いは、数値データと言語データのどちらを扱うのかです。QC7つ道具は決して古い手法ではなく、現在でも製造業の数値データを整理・分析して、改善活動を進めていくうえで欠かせない手法となっています。
今日のポイント
- QC7つ道具は製造現場のデータの整理や関係性の分析に役立つ代表的な手法
- QC7つ道具は「パレート図」「特性要因図」「グラフ」「ヒストグラム」「散布図」「管理図」
「チェックシート」のことを指す - QC7つ道具は語呂合わせで覚えるのがおすすめ
- QC7つ道具が扱うのは数値データで、新QC7つ道具が扱うのは言語データ
- QC7つ道具の使い方はQCストーリーのステップに沿って活用していく
製造業のDXはあおい技研
株式会社あおい技研は、製造業に特化した業務改善コンサルティングを提供し、製造現場のDX推進をサポートします。80以上の製造現場での診断や改善の経験を活かし、お客様に合ったDX戦略を提案します。
データ分析、業務効率化システムの開発、現場のデジタル化などを通じて、お客様の業務改善と生産性向上を支援します。
製造業のDXについては、あおい技研にご相談ください。
関連記事
-
作業性を向上できる取り組み4つ|製造業における成功事例も紹介
2022年11月28日
-
作業の効率化が進まない理由5つ!製造業における向上の事例も紹介
2023年9月12日
-
在庫管理をバーコードでするメリット3つ!デメリットやエクセルで自作する方法も解説
2023年11月6日
-
データ分析で製造業の何が変わる?つまずくポイントも解説
2025年3月24日
-
業務改善の方法を6ステップでご紹介|具体例やフレームワークも
2022年2月7日
-
勘と経験に頼らないモノづくりとは?製造業10社のデータ活用事例を紹介
2025年4月25日
-
7つのムダを初心者向けに徹底解説|それぞれの対処法や改善事例も紹介
2024年4月5日
-
業務管理の基本6つを初心者向けに解説!理由や進め方・役立つツールも紹介
2022年8月30日
-
在庫管理を見える化する方法3つ|メリットとExcelの活用事例も
2022年4月1日
カテゴリー
- IT化
- QCD
- QCサークル
- コスト削減
- コンサルタント
- スマートファクトリー
- ボトルネック工程
- 中小企業
- 労働生産性
- 合理化
- 品質担保
- 品質管理
- 在庫管理
- 工場IoT
- 工場効率化
- 工程管理
- 工程管理システム
- 投入資源
- 業務効率
- 業務改善
- 生産ライン
- 生産性向上
- 生産管理
- 生産管理システム
- 経費削減
- 製造業
- 製造業 DX
- 製造業IoT
- 見える化
- 設備管理
新着コラム
-
2025年8月27日
HACCP 7原則12手順で守る「食の安全」!
-
2025年8月27日
GMP認定で支える「安全性」!製造の信頼は工程から始まる
-
2025年7月30日
工場の労働環境を改善するための具体策とは?改善のステップや事例もご紹介
-
2025年7月30日
工場の暑さ対策を徹底解説!2025年義務化対応と効果的な対策とは?
-
2025年7月30日
工場の5S活動とは?生産性と安全性を高める改善の進め方
-
2025年6月30日
産業用ロボットとは?サービスロボットとの違いや種類、導入するメリットを解説
-
2025年6月30日
工場の省人化に取り組むメリットを解説!具体的なステップと事例をご紹介
-
2025年6月30日
【産業用ロボット】主要メーカーの市場シェアはどれぐらい?市場規模などわかりやすく解説
-
2025年5月28日
事例から学ぶ工場の安全対策!製造業の労災件数も紹介
-
2025年5月28日
ベンダーコントロールとは?定義やToDoを解説