改善提案でネタ切れしたときの対処法3つ!参考になるトヨタの事例も紹介
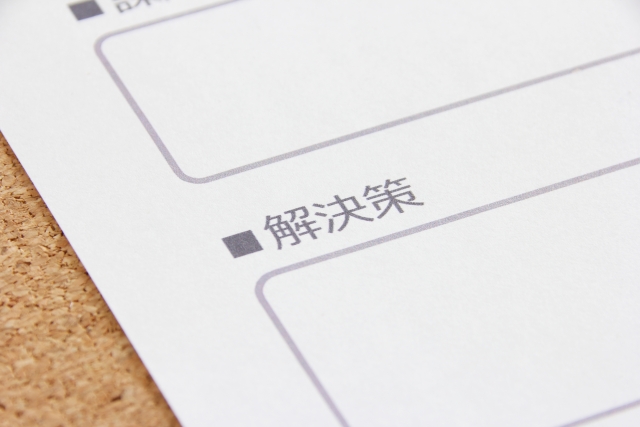
改善提案とは、日々の業務に潜む改善点を探し出し、その改善内容の提案を行うことです。改善提案は経営層や管理職の職員などに限らず、現場で働く従業員から行うケースもあります。ただ、改善提案をするのは難しく、ネタ切れになってしまうこともあるでしょう。
改善提案でネタ切れになってしまったときは、対処法を知って視点を変えてみることがおすすめです。視点を変えれば、新たな改善点が見つかり、得られる成果も大きくなります。今回は、改善提案でネタ切れしたときの対処法3つを解説します。改善提案のネタの参考になる、トヨタの事例も紹介するため、ご参考にしてみてください。
コンテンツ
改善提案でネタ切れしたときの対処法3つ
改善提案でネタ切れしてしまうのは、よくある話です。ネタ切れしてしまったからといって、適当に改善提案をするのはよくありません。対処法を知って、意義のある改善提案を行うようにしましょう。今回は改善提案でネタ切れしたときの対処法3つを解説します。
真似をする
改善提案のネタ切れになったときは、他社や他部署の過去の改善提案を真似する手段もあります。もちろん、そのまま流用するのではなく、参考にして自社や自分の部署の状況に合わせて、改善提案を考えることが大切です。
改善提案の事例は、本やWEB上の資料からでも知ることができます。頭が行き詰まってしまったときは、参考にできるような改善ネタの情報を積極的に探してみましょう。
テーマを絞り込む
改善案のネタ切れになる理由として、網羅的に考えすぎていることがあります。
そんなときは、テーマを絞り込むことで、深堀りした改善案を出せる可能性が高くなります。
例えば、今回は「作業環境について」、次回は「作業時間の短縮方法について」などです。テーマを絞り込むと、よりネタが出にくいのではと考える人もいるでしょう。しかし、実際にはテーマを絞り込むことで、考えるべきことが明確になり、改善提案のアイディアが発案しやすくなります。
視点を変える
改善案のネタ切れになったときは、思い切って視点を変えてみましょう。おすすめなのは、新入社員目線、外国人目線、顧客目線など、立場の視点を変えてみることです。視点を変えると、自分の立場からは見えてこなかった、課題や問題が浮き彫りになります。頭を柔らかくして、柔軟に考えることが大切です。
改善提案のネタの参考になる!トヨタの事例
改善で有名なのが、トヨタの成功事例です。トヨタの改善事例を知ると、改善提案のネタ出しの参考になります。改善提案のネタになるトヨタの事例を紹介します。
3M(ムリ・ムダ・ムラ)を削減して業務を改善
トヨタの改善で最も有名なのが、3M(ムリ・ムダ・ムラ)の削減です。
3Mの削減は、改善活動の基本でもあります。
- ムリ…能力以上の負荷がかかっている状態
- ムダ…付加価値を生まない非生産的な作業
- ムラ…業務の品質が一定ではない状態
この3つを意識して、業務に潜んでいないか洗い出しましょう。洗い出して改善提案を行い、改善活動を実施すれば大きな成果を得られます。
5Sで職場環境を整えて生産性を向上
5Sも、トヨタの改善事例で有名な手法です。5Sはシンプルな試みですが、製造業において大きな重要な取り組みのひとつです。
- Sorting(整理):必要なものと不要なものを分けて整える
- Setting-in-Order(整頓):必要なものをすぐに取り出せるようにする
- Shining(清掃):ゴミやホコリのないきれいで快適な状態にする
- Standardizing(清潔):整理・整頓・清掃の3Sの活動を維持できている状態
- Sustaining the Discipline(躾):整理・整頓・清掃の3Sの活動が習慣化し継続できる状態
5Sが徹底されると、現場の作業環境状況が大幅に向上します。トヨタは5Sの徹底によって、安全で効率的で快適な作業環境を実現しました。
ボトムアップ手法で現場の声を重視して改善
改善提案は、「トップダウン式」と「ボトムアップ式」で行われることがあります。トップダウン式とは、経営層が改善提案を行い、現場の従業員に命じ、協力してもらう方法です。このように従来、改善活動や提案はトップダウン式で行われるのが一般的でした。
現在主流となっている、ボトムアップ式を製造業に浸透させたのはトヨタです。
トヨタは現場の声を重視し、従業員たちに主体的に改善提案を行ってもらう形式を採用しました。
ボトムアップ式の改善提案のメリットは、
- 現場の声を重要視できる
- 従業員が能動的に取り組める
- 従業員のモチベーションが高くなる
ことです。
経営層からの指示を受けて動くのではなく、改善提案から実施まで自分たちで行うため、意欲的に動けるのがメリットです。
カンバン方式でタスク管理や進捗計画を効率化
カンバン方式とは、必要なものを、必要なときに、必要な分だけ作ることを目的とした生産方式です。トヨタが開発した、代表的な生産管理の手法の一つでもあります。カンバン方式の仕組みは、まず下流工程で部品を使ったら、部品名と数量を記したカンバンを上流工程に送ります。
受け取った上流工程では、届いたカンバンに書かれた部品を補充します。こういった、シンプルな流れになっています。カンバン方式を採用すると、大量の在庫ストックを抱えなくて済むのがメリットです。情報や問題を共有化しやすい、利点もあります。
改善提案でネタ切れしたときは新たな視点で考えよう(まとめ)
改善提案は、現場の作業環境を快適にし、全体の生産性を向上させるために大切な取り組みです。最近はボトムアップ式で、現場の従業員が改善提案をする機会が増えています。とはいえ、「改善提案をしてください」と言われても、良いアイディアが浮かばない人は多いのではないでしょうか。
定期的に何度も改善提案をする場面があると、ネタ切れになってしまう人も少なくないと思います。改善提案でネタ切れになったときは、他社や他部署のアイディアを参考にしたり、テーマを絞り込んだり、視点を変えたりするのがおすすめです。
大切なのは、そのまま真似をするのではなく、自社の現場の状況に合わせて柔軟に調整することです。改善したあとにどんな成果を得られるかイメージしながら、意義のある改善提案をしていきましょう。
今日のポイント
- 改善提案とは日々の業務に潜む改善点を探し出し改善の提案を行うこと
- 改善提案でネタ切れしたときの対処法3つは「真似をする」、「テーマを絞り込む」、「視点を変える」こと
- 改善提案のネタで困ったらトヨタの成功事例を参考にするのがおすすめ
製造業のDXはあおい技研
株式会社あおい技研は、製造業に特化した業務改善コンサルティングを提供し、製造現場のDX推進をサポートします。80以上の製造現場での診断や改善の経験を活かし、お客様に合ったDX戦略を提案します。
データ分析、業務効率化システムの開発、現場のデジタル化などを通じて、お客様の業務改善と生産性向上を支援します。
製造業のDXについては、あおい技研にご相談ください。
関連記事
-
改善提案のネタ事例15選!製造業や工場現場での小さな改善例を紹介
2023年5月23日
-
業務改善提案のネタの見つけ方3つ【提案書の書き方と例文も】
2024年2月20日
-
生産の4Mとは?初心者向けに基本・重要性・フレームワークなどを解説
2024年3月4日
-
製造業にDXが必要な理由|3つのトレンドと注意点もご解説
2022年1月20日
-
製造業のサプライチェーンの課題4つ【対応策】
2024年3月4日
-
稼働率と可動率の違い|計算式と数値を上げる方法4つ
2023年11月6日
-
業務効率化の成功事例7つを参考にアイデア出しをしよう!業務の無駄の見つけ方も解説
2023年12月12日
-
製造業の利益率の目安とは?計算方法5つや向上させる方法を解説!
2024年10月3日
-
製造業の人材育成をするときのポイント6つ【生産性向上につながる】
2024年5月7日
カテゴリー
- IT化
- QCD
- QCサークル
- コスト削減
- コンサルタント
- スマートファクトリー
- ボトルネック工程
- 中小企業
- 労働生産性
- 合理化
- 品質担保
- 品質管理
- 在庫管理
- 工場IoT
- 工場効率化
- 工程管理
- 工程管理システム
- 投入資源
- 業務効率
- 業務改善
- 生産ライン
- 生産性向上
- 生産管理
- 生産管理システム
- 経費削減
- 製造業
- 製造業 DX
- 製造業IoT
- 見える化
- 設備管理
新着コラム
-
2025年7月30日
工場の労働環境を改善するための具体策とは?改善のステップや事例もご紹介
-
2025年7月30日
工場の暑さ対策を徹底解説!2025年義務化対応と効果的な対策とは?
-
2025年7月30日
工場の5S活動とは?生産性と安全性を高める改善の進め方
-
2025年6月30日
産業用ロボットとは?サービスロボットとの違いや種類、導入するメリットを解説
-
2025年6月30日
工場の省人化に取り組むメリットを解説!具体的なステップと事例をご紹介
-
2025年6月30日
【産業用ロボット】主要メーカーの市場シェアはどれぐらい?市場規模などわかりやすく解説
-
2025年5月28日
事例から学ぶ工場の安全対策!製造業の労災件数も紹介
-
2025年5月28日
ベンダーコントロールとは?定義やToDoを解説
-
2025年5月28日
外部コンサルタントとは?内部との違いやメリット・デメリット
-
2025年4月25日
勘と経験に頼らないモノづくりとは?製造業10社のデータ活用事例を紹介