業務改善で原因分析をする手法4つ|役立つフレームワークも紹介
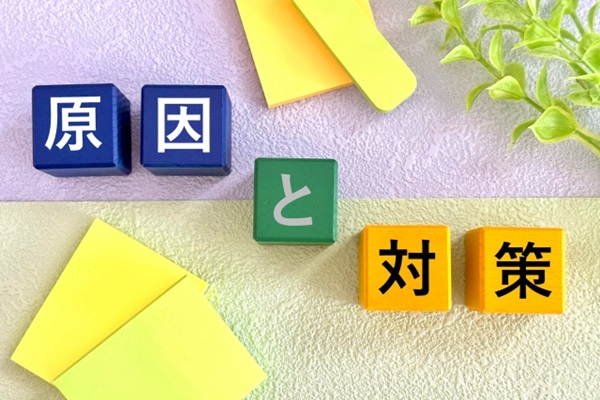
業務改善における原因分析は、問題を特定するプロセスとしてとても重要です。原因分析が適切に行われていないと、ボトルネックとなっている重要な問題を特定できません。業務改善における原因分析を正しく行うためには、効果的な手法やフレームワークを活用するのがおすすめです。
またBPMなどのツールを活用して、分析することもできます。今回は、業務改善における原因分析をする手法4つを紹介します。業務改善の原因分析に役立つフレームワークも掲載するので、ご参考にしてみてください。
コンテンツ
業務改善における原因分析とは問題を特定するプロセス
業務改善における原因分析は、問題を特定するプロセスでありとても重要です。業務改善をするためには、現状に潜む3M(ムリ・ムダ・ムラ)などの、問題や課題を洗い出さなくてはいけません。
浮き彫りになった問題や課題は、なぜ生じているのか原因分析と追及までセットで行うことで、効果的な改善案を立案できるようになります。
業務改善における原因分析をする手法4つ
業務改善における原因分析するときは、社内にある情報や市場の最新情報を参考にするのが効果的です。基本的な分析手法ではありますが、細かい点まで確認することで、思わぬ発見があることがあります。
ここでは業務改善における原因分析をする手法4つを紹介します。
社内データや日報を確認する
社内データや日報には、日々の小さな記録がたくさん残っています。社内に蓄積された、あらゆる項目のデータ分析を行うことは、多くの時間が必要となりますが、丁寧に行うことで、より精度の高い原因分析が期待できます。
業務日報や顧客からのクレーム記録を分析する
業務日報や顧客からのクレーム記録にも、問題や課題の原因のヒントが隠れています。特に、顧客からのクレーム記録には、現場で日常的に発生しているトラブルの情報が含まれています。情報全体を俯瞰的な視点で確認することを意識し、客観的にデータの傾向を掴み、原因分析を行いましょう。
アンケート調査やヒアリングを実施する
アンケート調査やヒアリングでは、新たな発見を見出せます。実際に業務内容表や業務量調査票などからは得られない、定性的な情報を収集できるのがメリットです。
例
- 従業員が想定外の工程で負担や疲労を感じていたことがわかった
- 顧客の満足度は製品の価格の低さよりも使用感としての品質の高さにあることがわかった
アンケート調査やヒアリングは自由記述式で実施することで、より定性的な情報を得られやすくなります。
社会情勢や市場の最新情報を参考にする
社内データだけでなく、社会情勢や市場の最新情報も参考になります。公に明かされている統計データやレポートは、重要な情報源です。SNSも含む各種メディアを活用し分析すれば、最新のリアルタイムな情報を得られます。
業務改善における原因分析に役立つフレームワーク
業務改善の原因分析をするときは、フレームワークを活用すると円滑に進みやすくなります。原因分析が行き詰まってしまったときの、打開策としてもおすすめです。業務改善の原因分析に役立つフレームワークを紹介します。
As is / To be
As is / To beは、現状と理想の差を明確化できるフレームワークです。As is(現状)とTo be(理想)をそれぞれ文章で書き出して、差は何なのか、どうすればギャップを埋められるのかを考えます。現状から理想を叶えるための方法を考えることで、問題の原因が明らかになり、分析も可能になります。
例
As is(現状)
- 新人とベテラン従業員の能力差がありすぎて生産数にムラが生まれている
To be(理想)
- 新人とベテラン従業員の能力差が少なく誰が担当しても生産数が安定している
=問題の原因は、マニュアルがない、作業が標準化されていない、新人とベテランでスキルやノウハウを共有する機会がないことにあると分析できる
ロジックツリー
ロジックツリーは、問題をシンプルに整理して分析できるフレームワークです。
1つの問題に対して「Why?」を問いかけ考え、樹木が枝分かれしていくような形で、大きな項目から小さな項目に分解し、なおかつ階層化して整理していくことで、原因分析を行う手法です。
例
問題:不良率が下がらない
考えられる「Why?」
- 製造プロセスに問題がある
→原材料の品質が悪い。
→受け入れ検査の結果にバラツキがある
→受け入れロット単位にて品質にバラツキがある
→製造条件にバラツキがある。
→製造工程での処理時間にバラツキがある
→製造プロセスの条件にバラツキがある - 製造装置に問題がある
→トラブルが多発している
→トラブルが発生している装置が同一装置に集中してい
→部品の交換頻度にバラツキがある
→交換部品の劣化具合にバラツキがある - 作業者のスキルに問題がある。
→ベテラン作業者の新人作業者にてバラツキがある
→ベテラン作業者の作業効率が高い
→新人作業者の作業効率が低い
→作業手順にバラツキがある
→作業手順に作業グループ毎に偏りがある
→作業時間に作業グループ毎に偏りがある
なぜなぜ分析
なぜなぜ分析は、問題を深掘りできるフレームワークです。1つの問題に対して「なぜ?」を繰り返し問いかけることで、真の原因を分析します。
例
問題:納期に間に合わず1週間遅くなった
↓
なぜ?:当初の納期設定に無理があった
↓
なぜ?:営業部門が生産現場のキャパシティを考えずに、厳しい納期で受注をとったから
↓
なぜ?:営業部門と生産部門のコミュニケーション不足により、営業部門は生産部門のキャパシティを把握できていないから
↓
なぜ?:営業部門と生産部門の物理的距離が離れており、連絡を取ることが困難だから。また、問い合わせをしても、生産部門が忙しく回答がすぐに返ってこないから。
↓
なぜ?:生産状況や製造部門のキャパシティを把握するための仕組みがなく、営業部門の問い合わせのたびに生産部門の担当者が現場を駆け回らなければならないから。
この『なぜなぜ分析』はトヨタ自動車にて発案され、この問題解決と再発防止を目的に生み出されましたが、一般的には『なぜ?』を5回繰り返すことで真の原因に辿り着くと言われています。原因分析においてこの手法はとても有効な手段の一つとなっています。
https://it-trend.jp/project_management/article/33-0064#d0e9d87eb78fa54e47cd213ca7606442
BPMなどのツールを活用して分析するのもおすすめ
BPMとは、「Business Process Management」の略称で、業務プロセスを可視化・自動化できるツールです。BPMを導入すると、製造・出荷・販売などの業務プロセス全体を、一元管理できるようになります。
リアルタイムに情報を収集し蓄積できるため、業務改善における原因分析には大きく役立ちます。BPMは業務改善に役立ち、生産性向上を実現する画期的なツールですが、自社に合った形で導入・運用しなければ意味がありません。
却って非効率になったり、無駄なコストが発生したりする可能性もあります。
BPMなどの業務効率化や原因分析ツールを導入するときは、専門性の高いコンサルタントや企業に相談して検討するのがおすすめです。
専門家に相談してサポートしてもらうことで、コストを最小限に抑えて、無駄のない適切なツールの導入・運用が期待できます。あおい技研では、製造業での豊富なコンサルタント実績と経験を活かして、BPMのようなツール導入のご相談も承っています。
ただツールの導入をおすすめするのではなく、実際に現場に足を運んで、企業に合ったベストな業務改善方法や原因分析手法を、ご提案させていただきます。ご予算や状況に応じて、本当に必要なものだけをご提案させていただきますので、お悩みの方はいつでもお気軽にご相談ください。
業務改善で原因分析をするときは手法やフレームワークを活用しよう(まとめ)
業務改善における原因分析は、改善活動で高い成果を出すためにとても重要です。問題や課題の原因分析ができてないと、効果的な改善案の立案はできません。
業務改善における原因分析をする手法は多数ありますが、社内データの確認と分析、アンケート調査やヒアリングの実施、社会情勢や市場情報のチェックが基本です。普段はあまり気にしていない点に着目してみるだけでも、新たな発見が見出せる可能性が高くなります。
原因分析で行き詰まったときは、フレームワークを活用したり、BPMなどの専用ツールの導入を検討したりするのもおすすめです。
今日のポイント
- 業務改善における原因分析とは問題を特定するプロセスのこと
- 業務改善における原因分析をする手法4つは「社内データや日報の確認」「業務日報や顧客からのクレーム記録の分析」「アンケート調査やヒアリングの実施」「社会情勢や市場の最新情報のチェック」
- 業務改善における原因分析に役立つフレームワークにはAs is / To be、ロジックツリー、なぜなぜ分析などがある
- 専門性の高いコンサルタントや企業に相談しながらBPMなどのツールを活用して分析するのもおすすめ
製造業のDXはあおい技研
株式会社あおい技研は、製造業に特化した業務改善コンサルティングを提供し、製造現場のDX推進をサポートします。80以上の製造現場での診断や改善の経験を活かし、お客様に合ったDX戦略を提案します。
データ分析、業務効率化システムの開発、現場のデジタル化などを通じて、お客様の業務改善と生産性向上を支援します。
製造業のDXについては、あおい技研にご相談ください。
関連記事
-
合理化とは?製造業における意味と効率化との違い・事例3つをご紹介
2022年6月15日
-
労働効率とは?向上させて得られるメリット3つと計算方法・日本が低い理由を解説
2022年12月1日
-
在庫管理を見える化する方法3つ|メリットとExcelの活用事例も
2022年4月1日
-
工場にIoTを導入してスマートファクトリー化すると解決できる課題5つ
2022年4月28日
-
生産性を上げるために個人が取り組める3つのこと|経営者目線での施策も紹介
2022年11月9日
-
業務改善のプロセスが上手く進まない理由4つ【対処法】
2024年7月9日
-
制約理論を初心者向けにわかりやすく解説【業務改善手順の5ステップ】
2023年11月6日
-
効率化とは?4つのポイントで初心者向けに基本を徹底解説!
2023年2月27日
-
工場の設備管理はきつい?求人・資格・年収の3つの観点から徹底解説
2023年12月12日
カテゴリー
- IT化
- QCD
- QCサークル
- コスト削減
- コンサルタント
- スマートファクトリー
- ボトルネック工程
- 中小企業
- 労働生産性
- 合理化
- 品質担保
- 品質管理
- 在庫管理
- 工場IoT
- 工場効率化
- 工程管理
- 工程管理システム
- 投入資源
- 業務効率
- 業務改善
- 生産ライン
- 生産性向上
- 生産管理
- 生産管理システム
- 経費削減
- 製造業
- 製造業 DX
- 製造業IoT
- 見える化
- 設備管理
新着コラム
-
2025年8月27日
HACCP 7原則12手順で守る「食の安全」!
-
2025年8月27日
GMP認定で支える「安全性」!製造の信頼は工程から始まる
-
2025年7月30日
工場の労働環境を改善するための具体策とは?改善のステップや事例もご紹介
-
2025年7月30日
工場の暑さ対策を徹底解説!2025年義務化対応と効果的な対策とは?
-
2025年7月30日
工場の5S活動とは?生産性と安全性を高める改善の進め方
-
2025年6月30日
産業用ロボットとは?サービスロボットとの違いや種類、導入するメリットを解説
-
2025年6月30日
工場の省人化に取り組むメリットを解説!具体的なステップと事例をご紹介
-
2025年6月30日
【産業用ロボット】主要メーカーの市場シェアはどれぐらい?市場規模などわかりやすく解説
-
2025年5月28日
事例から学ぶ工場の安全対策!製造業の労災件数も紹介
-
2025年5月28日
ベンダーコントロールとは?定義やToDoを解説