7つのムダを初心者向けに徹底解説|それぞれの対処法や改善事例も紹介
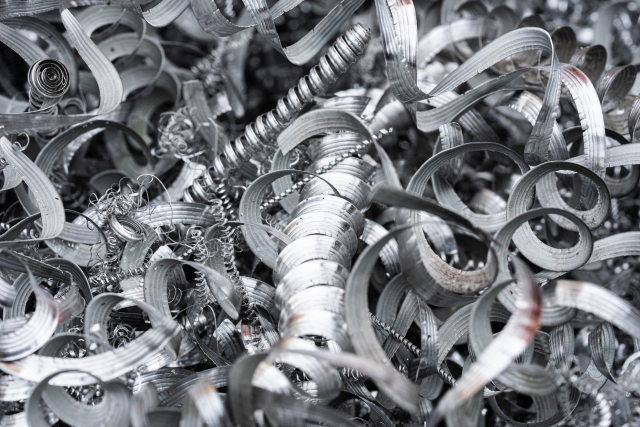
7つのムダとは、トヨタの生産方式を実現するために生まれた改善手法の一つです。現在、多くの製造現場で採用されている手法で、現状のムダを7つに分類し、洗い出すことで、改善点を明確にし、ムダの排除を目指します。
7つのムダを洗い出して排除するには、それぞれの適切な対処法を知っておくことが大切です。また製造業では7つのムダを活用した改善事例を参考にするのもおすすめです。
今回は初心者向けにそれぞれの対処法や改善事例について徹底解説しますので、ご参考にしてみてください。
コンテンツ
7つのムダとは
トヨタの生産方式である「自働化」と「ジャストインタイム」を実現するために、これらの4つ手法は生まれました。そして、7つのムダは、トヨタの生産における下記の4つの手法から展開されています。
- カイゼン…問題を改善するだけでなく、現状の作業効率をより良くするための改善活動
- 問題の見える化…問題が発生したときに、内容を誰が見てもわかるようにすること
- なぜなぜ分析…問題の本質的な解決のために「なぜ」を何度も繰り返し深く原因究明すること
- 7つのムダの排除…製造現場のムダを7つに分類し洗い出し改善点を明確にして排除すること
「自働化」と「ジャストインタイム」の実現手法の一つ
トヨタの生産方式である「自働化」とは、機械に異常が生じたらすぐに自動で停止し、不良品の発生を防ぐことです。
「じどうか」と読みますが、トヨタは「自動化」ではなく、ニンベンの付いた漢字を使い「自働化」と区別しています。
これは、前者の「自動化」が人の作業を”機械”に置き換えているのに対して、後者の「自働化」は人の”働き”を機械に置き換えているという考えに基づいているからです。
そのため「自働化」が実現すると、人が機械を管理する手間が省け、不良品の発生も未然に防げるため、生産性が向上します。
次にトヨタの生産方式「ジャストインタイム(JIT)」とは、「必要なものを、必要なときに、必要なだけ」供給し、生産することです。具体的には各工程に必要なものだけを用意し、流れるように停滞なく生産できるようにします。
「ジャストインタイム」が実現すると、在庫が適正化される事によりコストが削減し、さらに生産リードタイムも短縮できるため、結果的に生産性の向上見込めます。
トヨタの生産方式では「自働化」と「ジャストインタイム」を実現するため、製造現場のムダを7つに分類し、改善点を明確にして排除するために、7つのムダの手法は生まれました。
7つのムダ|加工・在庫・造りすぎ・手持ち・動作・運搬・不良と手直し
7つのムダは、「加工」、「在庫」、「造りすぎ」、「手持ち」、「動作」、「運搬」、「不良と手直し」に分類されます。それぞれの内容と対処法(排除方法)を紹介します。
加工のムダ
加工のムダとは、必要のない加工や検査の作業によるムダのことです。製造業において加工方法が最適化されていなかったり、そもそも必要のない検査をしていたりする可能性があります。
加工のムダの対処法は、時間のかかっている作業に着目して加工方法を見直したり、過剰な検査を撤廃したりできないか検討することです。
在庫のムダ
在庫のムダとは、必要のない在庫によるムダのことです。具体的には、「大量の発注が入ったときのために」、「不良品が出たときに使えるように」、など心理的な安心感を得るなどの理由で、現状使う予定がないのに抱えてしまっている在庫などを指します。
在庫のムダの対処法は、在庫管理の徹底と生産計画の緻密化です。そもそも在庫管理ができていないと、既に使えない状態の在庫を保持してしまっている可能性もあります。
そのため生産計画を緻密化すると、必要な在庫が明確になり、心理的な理由で過剰在庫を抱えなくても済むようになります。
造りすぎのムダ
造りすぎのムダとは、必要のない数まで生産を行う、造りすぎによるムダのことです。7つのムダの中でも、特に悪いと考えられています。
必要のない数まで生産を行うと、在庫管理などの余分なコストが発生するからです。造りすぎのムダの対処法は、生産計画を徹底することです。
生産計画を見直し、必要な生産数を明確にし、現場で確実に指示・情報共有できるようにします。
手待ちのムダ
手待ちのムダとは、作業員が手持ち無沙汰で何もすることがない状態によるムダのことです。具体的には、「前の工程から流れてくる作業を待つ時間」や「機械が稼働するのを待つ時間」などです。
手待ちのムダの対処法は、作業員の作業のバラつきを把握し、適切な人員配置を見直したり、機械が稼働するまでの時間にできる作業を計画に組み込んだりすることです。
動作のムダ
動作のムダとは、作業中に必要のない動作を挟んでいることによるムダのことです。たとえば、下に置いてあるものを取るために何度もしゃがんだり、工具を頻繁に持ち替えたり、効率の悪い動作を指します。
動作のムダの対処法は、作業環境の最適化とマニュアルや教育の徹底です。必要のない動作が生まれないように環境を整え、作業を標準化することが大切です。
運搬のムダ
運搬のムダとは、非効率なものの移動や必要のない移動距離によるムダのことです。一箇所に集約させているものを何度も移動したり、現場のレイアウトが適正化されておらず運搬に時間がかかったりするムダを指します。
運搬のムダの対処法は、工具や部品の置き場所を見直したり、現場のレイアウトを見直したりすることです。
不良と手直しのムダ
不良と手直しのムダとは、不良品の発生と伴う手直しのムダのことです。品質管理が甘いと起こりやすく、コストも手間もかかるため問題視されています。不良と手直しのムダの対処法は、品質管理と条件管理の徹底です。
7つのムダの具体的な改善事例
7つのムダに対処するためには、製造業の実際の改善事例を参考にするのがおすすめです。7つのムダの具体的な改善事例を紹介します。
加工のムダを排除:手作業の一部を機械で自動化
部品を切削する工程で発生するバリを手作業で取り除いていたのを、機械にバリ取り加工を追加し自動化できるようにしました。作業員の負担を軽減でき、バリ取りにかかる時間も短縮されました。
参考出典:https://www.imao.co.jp/kaizen-104.html
在庫のムダを排除:在庫の入出庫処理に電子タグを導入して効率化
部品の入出庫処理を手動入力で行なっていたのを、電子タグ(RFID)を導入して効率化できるようにしました。作業時間を短縮でき、在庫管理も正確に行えるようになりました。
参考出典:https://www.ricoh.co.jp/service/digital-manufacturing/media/article/detail16
動作のムダを排除:作業台を見直して効率化
作業台のスペースが小さく、下に置いてある備品がわかりづらく何度も取り出していたのを、備品置き場のスペースを広げることで取り出しやすく効率化しました。作業時間を短縮でき、作業員の身体の負担も軽減しました。
参考出典:https://www.imao.co.jp/kaizen-118.html
7つのムダはトヨタの生産方式を実現するための改善手法(まとめ)
7つのムダは、トヨタの生産における4つの手法(カイゼン・問題の見える化・なぜなぜ分析・7つのムダの排除)から展開されています。製造現場のムダを7つに分類し、改善点を明確にして排除することで、トヨタの「自動化」と「ジャストインタイム」の実現に貢献することが目的です。
7つのムダは、「加工」、「在庫」、「造りすぎ」、「手待ち」、「動作」、「運搬」、「不良と手直し」に分類されます。それぞれのムダを理解し、適切な対処を行なっていくことで、生産性向上を目指せます。
今日のポイント
- 7つのムダとはトヨタの生産方式を実現するための手法の一つ
- 7つのムダは「加工」「在庫」「造りすぎ」「手待ち」「動作」「運搬」「不良と手直し」
- 7つのムダを洗い出して排除を目指すためには適切な対処法を知っておくことが大切
製造業のDXはあおい技研
株式会社あおい技研は、製造業に特化した業務改善コンサルティングを提供し、製造現場のDX推進をサポートします。80以上の製造現場での診断や改善の経験を活かし、お客様に合ったDX戦略を提案します。
データ分析、業務効率化システムの開発、現場のデジタル化などを通じて、お客様の業務改善と生産性向上を支援します。
製造業のDXについては、あおい技研にご相談ください。
関連記事
-
QC7つ道具を初心者向けに解説!覚え方や使い方を5ステップで紹介
2022年7月4日
-
データ分析で製造業の何が変わる?つまずくポイントも解説
2025年3月24日
-
勘と経験に頼らないモノづくりとは?製造業10社のデータ活用事例を紹介
2025年4月25日
-
QCサークル活動の進め方|4つの基本要素と成功させるポイント
2021年12月24日
-
業務管理の基本6つを初心者向けに解説!理由や進め方・役立つツールも紹介
2022年8月30日
-
製造業の見える化とは?意味と目指すメリット・実行する方法・事例をご紹介
2021年10月20日
-
作業の効率化が進まない理由5つ!製造業における向上の事例も紹介
2023年9月12日
-
作業性を向上できる取り組み4つ|製造業における成功事例も紹介
2022年11月28日
-
業務改善の方法を6ステップでご紹介|具体例やフレームワークも
2022年2月7日
カテゴリー
- IT化
- QCD
- QCサークル
- コスト削減
- コンサルタント
- スマートファクトリー
- ボトルネック工程
- 中小企業
- 労働生産性
- 合理化
- 品質担保
- 品質管理
- 在庫管理
- 工場IoT
- 工場効率化
- 工程管理
- 工程管理システム
- 投入資源
- 業務効率
- 業務改善
- 生産ライン
- 生産性向上
- 生産管理
- 生産管理システム
- 経費削減
- 製造業
- 製造業 DX
- 製造業IoT
- 見える化
- 設備管理
新着コラム
-
2025年7月30日
工場の労働環境を改善するための具体策とは?改善のステップや事例もご紹介
-
2025年7月30日
工場の暑さ対策を徹底解説!2025年義務化対応と効果的な対策とは?
-
2025年7月30日
工場の5S活動とは?生産性と安全性を高める改善の進め方
-
2025年6月30日
産業用ロボットとは?サービスロボットとの違いや種類、導入するメリットを解説
-
2025年6月30日
工場の省人化に取り組むメリットを解説!具体的なステップと事例をご紹介
-
2025年6月30日
【産業用ロボット】主要メーカーの市場シェアはどれぐらい?市場規模などわかりやすく解説
-
2025年5月28日
事例から学ぶ工場の安全対策!製造業の労災件数も紹介
-
2025年5月28日
ベンダーコントロールとは?定義やToDoを解説
-
2025年5月28日
外部コンサルタントとは?内部との違いやメリット・デメリット
-
2025年4月25日
勘と経験に頼らないモノづくりとは?製造業10社のデータ活用事例を紹介