工場内の物流を自動化したい!ハードルはなぜ高い?
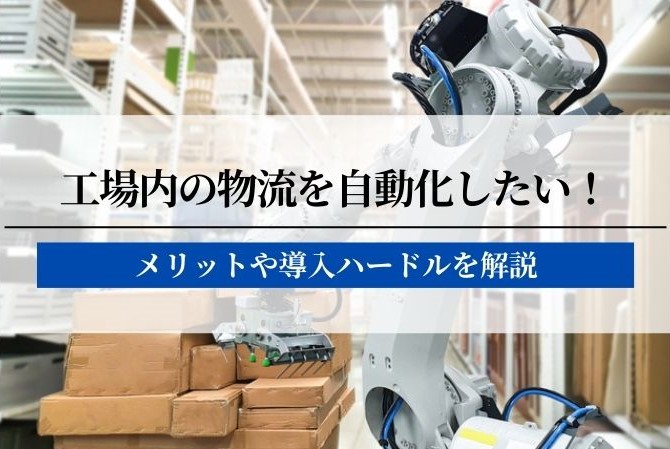
近年、ロボット技術やデジタルシステムの進化によって、工場の物流を自動化・省人化する動きが加速しています。
人手不足や生産性向上のために「導入したい」と考える企業も増えているものの、実際の現場では様々なハードルが存在し、スムーズに進まないケースも少なくありません。
・なぜ今、自動化が必要なのか?
・導入するとどんなメリットがあるのか?
・逆に、どんなハードルがあるのか?
工場内の物流を自動化するにあたって思い浮かぶ、上記の疑問点について解説します。
コンテンツ
工場内で物流の自動化が求められる背景
現代の製造業を取り巻く環境は、人手不足とコスト競争の激化という二つの大きな波にさらされています。
少子高齢化により働く人自体が減っているうえ、働き方改革で長時間労働が避けられるようになると、単純に「人を増やす」というやり方だけでは乗り切れません。
また、工場のコア業務である「製造(モノづくり)」を効率よく進めるには、材料の受け入れから生産ラインへの供給、完成品の出荷までの流れがスムーズであることが必須です。
ところが、多くの工場では台車やフォークリフトを使って人が重い荷物を運ぶ、在庫の位置を手作業で確認するなど、いまだに人手が主体という現場もまだまだ多いもの。
一方でロボット技術やIoT(モノのインターネット)の進化に伴って、「工場内物流」を自動化・省人化して人手不足を解消しようと考える企業は増えています。
つまり、「製造業の課題である人手不足や非効率性を改善するためには、工場内の物流をもっと楽にする必要がある。そのために、ロボットやデジタル技術をうまく活用したい」というのが背景です。
工場内の物流を自動化するメリット
工場内の物流を自動化することで得られるメリットは、大きく分けて四つあります。
コスト削減
メリットの一つ目として、人件費や誤出荷に伴う追加コストを抑えるという点で、コスト削減が期待できます。
従来、人手をかけて行われていた搬送・仕分けなどの工程をロボットや自動機器が担うようになると、作業者の人数を削減でき、人件費が下がります。
さらにヒューマンエラーが減ることで、誤出荷や追加搬送といったリカバリー対応の工数も削減されます。
作業者の負担軽減と安全性向上
次に「作業環境の改善」です。
作業者が負担していた重労働や危険な作業が軽くなるため、現場の労働環境が改善します。
自動搬送機やロボットが荷物を運んでくれるなら、作業者は腰や膝に負担をかけるような動作を続けなくて済みます。
また、フォークリフトとの接触事故や転倒事故が減るほか、高所作業や夜間の倉庫内移動などの安全リスクも減らせます。
こうした負担軽減は、労災リスクを低減して、作業者の定着率向上につながります。
生産性の向上
ロボット・自動化設備は、人間と違って休憩や交代を必要とせず、同じパフォーマンスで稼働し続けます。
必要な時に必要な物を確実に運べるようになることで、工場全体の生産性が底上げできることが大きなメリットです。
例えば、「部品が足りないから待機状態になる」というロスを減らし、かつスピードや正確性が安定する分、製造工程そのものの流れがスムーズになります。
DXの推進
工場内の物流自動化は、DX(デジタルトランスフォーメーション)の推進にも大きく貢献します。
自動化設備はたいていセンサーやネットワーク機能を備えており、どの時点で何が運ばれたか、在庫量がどう変化したかといった情報がリアルタイムで蓄積されます。
これらのデータは生産計画システムや販売管理システムと連動させればさらに大きな効果を発揮し、在庫最適化や需要予測などの高度な取り組みにも活かせます。
データに基づく意思決定が進むことで、工場全体の最適化が実現しやすくなります。
工場内物流自動化の具体例
では具体的に、どんな技術やシステムを使って自動化するのでしょうか。
代表的な例を以下に示します。
AGV(無人搬送車)/AMR(自律走行ロボット)
工場の床に貼られた磁気テープやQRコードをたどって走るタイプから、センサーやカメラで周囲の状況をリアルタイムに読み取り、障害物を避けながら自律走行するタイプまで、その種類は様々。
運べる重量も数十キロから数トンまで対応できる機種があり、運搬対象やレイアウトに応じて適したロボットを選べるのがポイントです。
自動倉庫
自動倉庫は、ラックを巨大な機械装置で制御して、入出庫の際に在庫を自動で取り出すシステムを指します。
大がかりではありますが、保管効率を高めながらピッキングや積み下ろしを無人化しやすいという点がメリット。
工場の敷地面積や在庫の形状に合わせて、シャトル式や垂直式などいろいろな形式があるため、導入前にはシミュレーションが必要です。
パレタイジングロボット(パレタイザ)
パレタイジングロボットとは、工場内で製品や荷物をパレットに積み上げる作業(パレタイジング)を自動化するロボットです。
人間が完成品をパレットに積み上げたり、逆にパレットから取り出したりする作業は体力を要し、ミスも起こりがち。
そこをロボットアームで自動化すれば、人手の負担を大幅に減らせますし、段積み高さや配置も正確に行えるゆえに品質が安定します。
WMSや生産管理システムとの連携
前述したようなハード面の技術に加え、システム連携こそが自動化の要です。
具体的にはWMS(Warehouse Management System)やMES(Manufacturing Execution System)というシステムが倉庫内在庫や生産進捗を管理して「いつ・どこに・何を運ぶべきか」をロボットや自動倉庫に指示します。
生産管理システムとリンクすれば、ラインの状況をリアルタイムに把握して必要な資材を遅れなく供給できるようになります。
工場内物流の自動化が進まない理由
初期投資の大きさ
工場内物流を自動化するには、搬送ロボットや自動倉庫などの導入費がかかります。
床面の改装や設備の据え付けなどの工事も必要となる場合があり、比較的大規模な投資を要するケースが多いです。
予算面でハードルが高く、回収期間が読みにくいと判断されがちです。
レイアウトやスペースの制約がある
「搬送ロボットを導入したい」「自動倉庫を置きたい」と思っても、工場の通路幅や天井高、既存の設備のレイアウトによってはスムーズに設置できません。
無人搬送車(AGV)の走行ルートを確保できない、あるいは倉庫を立体化するほどの高さがないといった問題に直面すると、追加工事やレイアウト変更が必要になるため、導入を断念してしまうケースもあるでしょう。
業務フローの標準化が不十分
現場によって作業手順や保管ルールがバラバラの状態だと、自動化設備だけを導入しても十分な効果は得られません。
自動化設備は基本的に「決められたルール通りに物を搬送する」「登録された在庫データをもとに動く」という仕組みのため、事前に業務フローをしっかり標準化・統一化しておかなければ、運用が混乱するリスクがあります。
「まずは現状の棚卸し作業や生産ラインへの供給手順を整理しなければ導入できない」となり、先延ばしになってしまうのです。
生産計画やシステムとの連携の難しさ
工場内の物流を自動化するにあたっては、AGVや自動倉庫などのハードウェアだけでなく倉庫管理システム(WMS)や生産管理システム(MES)との連携が必要です。
製造工程が複雑だったり、社内で使われているITシステムが古かったりすると、新しい機器との連動には追加開発や既存システムの改修が必要になります。
そうしたシステム面の調整コストを考えると、「今は導入が難しい」と判断されてしまいます。
上述した理由により、「導入すればメリットが大きい」とは分かっていても、なかなか踏み切れない企業は少なくありません。
しかし、技術の進歩や導入支援サービスの充実により、以前より小回りの利くロボットやシステムも増えてきています。
コストや社内体制を含めた総合的な準備を進めつつ、一歩ずつでも自動化に向けて検討を始めてはいかがでしょうか。
「とは言え、まず何から始めたらいいかわからない」
そんなお悩みをお持ちの方、製造業に特化したコンサルティング会社「あおい技研」へご相談ください。
工場内物流の自動化、ご相談は「あおい技研」へ
自動化の仕組みづくりをすることで、工場内の物流は大きく変わります。
導入前の要件定義や現場フローとの調整は、ぜひ「あおい技研」にご相談ください。
【実績例】
・工場構内の物流改善
・各種工程の分析、作業改善のご提案
・労働生産性の向上
・熟練作業者のノウハウ可視化、システム要件への落し込み
・製造ライン増設や工場リプレースにかかるレイアウト検討、シミュレーション
ものづくりの仕事では、一つひとつの現場に違った課題、難しさがあるもの。
「○○方式」といった一律の方法だけを提案するのでは、本質的な問題解決にはなりません。
私たちは現場の「かかりつけ医」として、データ分析を基にした仮説と施策を打ち出します。
業務改善やコスト削減など、ものづくりの現場ならではのお悩みをぜひご相談ください。
まとめ
工場内物流の自動化は、人手不足の解消やコスト削減、生産性の向上といった多くのメリットをもたらします。
しかし、導入には初期投資やレイアウトの問題、業務フローの標準化といったハードルがあり、これらをクリアしなければ十分な効果を発揮できません。
そのハードルを乗り越えるためには、自社だけで悩まずに製造業に特化したコンサルタント「あおい技研」にご相談ください。
製造業のDXはあおい技研
株式会社あおい技研は、製造業に特化した業務改善コンサルティングを提供し、製造現場のDX推進をサポートします。80以上の製造現場での診断や改善の経験を活かし、お客様に合ったDX戦略を提案します。
データ分析、業務効率化システムの開発、現場のデジタル化などを通じて、お客様の業務改善と生産性向上を支援します。
製造業のDXについては、あおい技研にご相談ください。
関連記事
-
データ分析で製造業の何が変わる?つまずくポイントも解説
2025年3月24日
-
工場の自動化に成功した企業の事例5つ【導入メリットやデメリット】
2022年6月27日
-
製造業DXが進まない理由3つ|進めるときのポイント
2024年6月13日
-
業務改善で問題点の洗い出しをする方法3つ!重要な理由と注意点もご解説
2022年3月3日
-
生産の4Mとは?初心者向けに基本・重要性・フレームワークなどを解説
2024年3月4日
-
業務効率化の手法7つ|アイデア出しができないと悩んだときに
2023年1月25日
-
時間で生産性を表す人時生産性を向上させる方法4つ!重要性とメリットも紹介
2022年11月8日
-
改善提案のネタ事例15選!製造業や工場現場での小さな改善例を紹介
2023年5月23日
-
業務の平準化のメリット7つ【製造業】
2024年6月13日
カテゴリー
- IT化
- QCD
- QCサークル
- コスト削減
- コンサルタント
- スマートファクトリー
- ボトルネック工程
- 中小企業
- 労働生産性
- 合理化
- 品質担保
- 品質管理
- 在庫管理
- 工場IoT
- 工場効率化
- 工程管理
- 工程管理システム
- 投入資源
- 業務効率
- 業務改善
- 生産ライン
- 生産性向上
- 生産管理
- 生産管理システム
- 経費削減
- 製造業
- 製造業 DX
- 製造業IoT
- 見える化
- 設備管理
新着コラム
-
2025年7月30日
工場の労働環境を改善するための具体策とは?改善のステップや事例もご紹介
-
2025年7月30日
工場の暑さ対策を徹底解説!2025年義務化対応と効果的な対策とは?
-
2025年7月30日
工場の5S活動とは?生産性と安全性を高める改善の進め方
-
2025年6月30日
産業用ロボットとは?サービスロボットとの違いや種類、導入するメリットを解説
-
2025年6月30日
工場の省人化に取り組むメリットを解説!具体的なステップと事例をご紹介
-
2025年6月30日
【産業用ロボット】主要メーカーの市場シェアはどれぐらい?市場規模などわかりやすく解説
-
2025年5月28日
事例から学ぶ工場の安全対策!製造業の労災件数も紹介
-
2025年5月28日
ベンダーコントロールとは?定義やToDoを解説
-
2025年5月28日
外部コンサルタントとは?内部との違いやメリット・デメリット
-
2025年4月25日
勘と経験に頼らないモノづくりとは?製造業10社のデータ活用事例を紹介