製造業のDX事例を10個ご紹介!各企業に分けて徹底解説
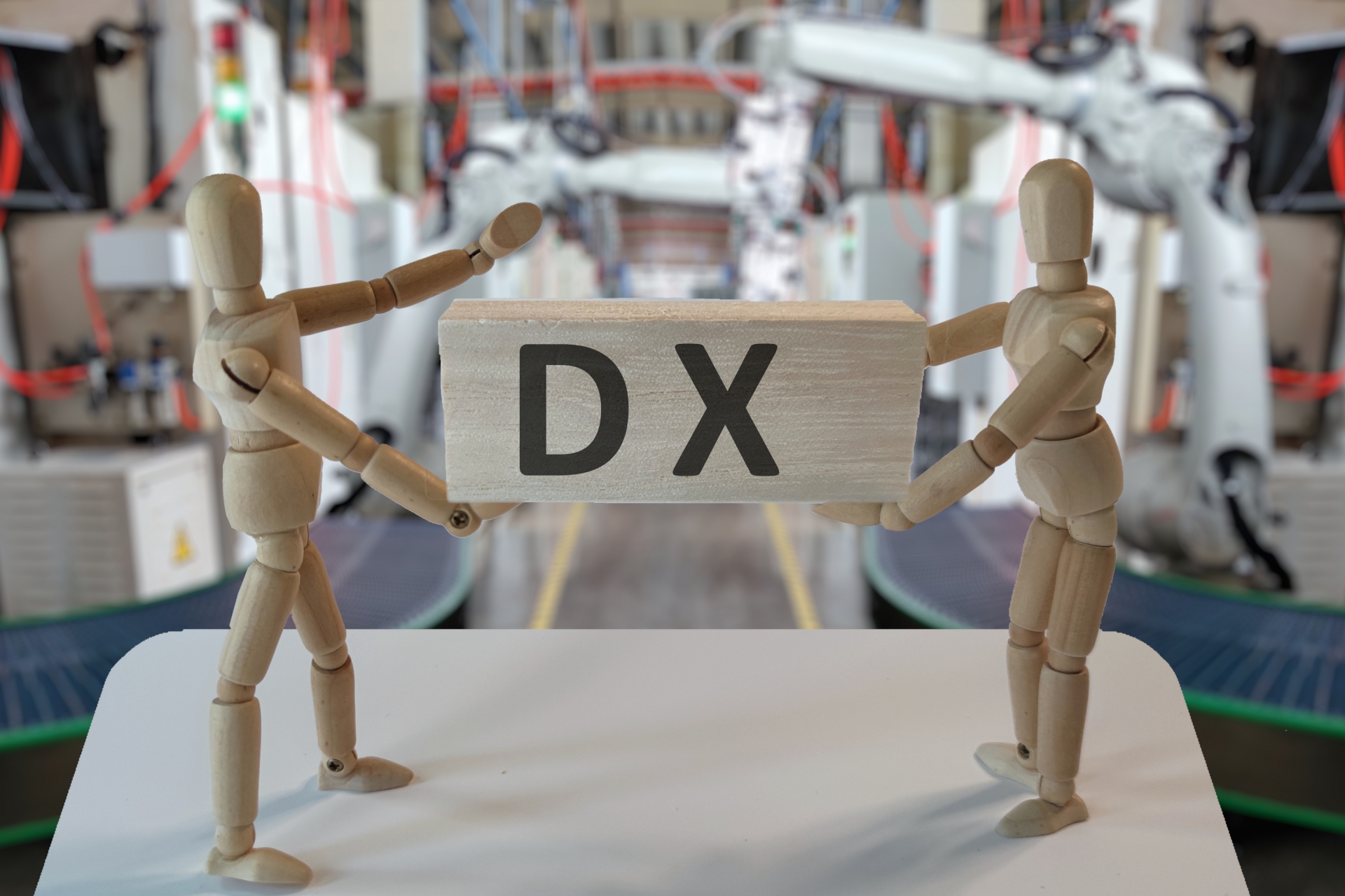
製造業において、DX(デジタルトランスフォーメーション)は生産性の向上や人材不足の解消に欠かせない取り組みとなっています。
しかし、どのようにDXを推進すればよいのか悩んでいる企業も多いのではないでしょうか。
本記事では、実際にDXに取り組んでいる企業の事例を10個紹介します。
具体的な取り組みを知り、自社に活かせるヒントを見つけてください。DXを進めるためのステップも解説しますので、ぜひ参考にしてください。
製造業にDXが必要と言われる理由
製造業においてDXが求められる理由は、業界が直面するさまざまな課題を解決できるからです。特に日本では、少子高齢化による人手不足や現場での情報共有不足による技術の属人化が深刻な問題となっています。DXの導入により、自動化や業務効率化が進み、業務の標準化や生産性向上が実現します。加えて、企業間の競争力強化にもつながり、変化する市場での柔軟な対応が可能になります。
人手不足を解決する
少子高齢化により製造現場の人手不足が深刻化しています。DXを導入することで、製造プロセスの自動化やAIを活用した効率化が進み、必要な人手を減らしながらも高い生産性を維持することが可能です。また、ロボットの導入によって単純作業を自動化し、従業員がより付加価値の高い業務に専念できる環境を整えます。
情報共有をして属人化を防ぐ
属人化は、特定の人材に依存して業務が進む状況を指します。例えば、ある仕事がその人しかできない状態やその人しか知らない情報がある状況が「属人化」と言えます。
製造現場では、熟練工の知識や経験に頼りがちな傾向があり、技術伝承や業務効率化の妨げになる傾向があります。DXによって業務をデジタル化し、データやノウハウを一元管理すれば、誰でもその情報にアクセスできるようになります。
属人化を防ぐことにより、情報共有が進み、特定の人に依存しない体制が整い、業務のスムーズな引き継ぎや継続的な改善が可能になります。
製造業のDX事例
1.沖電気工業株式会社 「バーチャル・ワンファクトリー」
沖電気工業株式会社は、埼玉県本庄市と静岡県沼津市にある2つの工場を仮想的に1つの工場として融合する「バーチャル・ワンファクトリー」プロジェクトを推進しています。
この取り組みは、「部門間融合」「生産融合」「試作プロセス融合」「IT融合」の4つの施策を進めることで、コスト削減と外部環境変化への対応力を強化することを目指しています。工場間の設計データを共通化し、生産の効率化を図るとともに、工場間の負荷分散を可能にしました。
これにより、多品種少量生産のニーズの取り込みと、人手不足への対応を実現しています。
2.トヨタ自動車株式会社 「工場IoT」
トヨタ自動車では「工場IoT」を導入し、生産現場のデジタル化を進めています。トヨタの「工場IoT」は、3D CADデータなど既存のデジタル化データを一元管理し、工場と現場の部署間にまたがる情報共有基盤を構築することが目的です。
現有資産の最大有効活用、データ分析の効率化、FA機器類からのデータ授受の有効活用、インターフェースの標準化など、効率や費用対効果を重視した取り組みが行われています。また、各社員がボトムアップでの小規模プロジェクトを立ち上げ、効果を見極めながら進める手法を採用しています。
これにより、人材育成も併せて、製造工程全体のデジタル化を段階的に進めることに成功しています。
3.三菱電機株式会社 「e-F@ctory」
三菱電機株式会社の「e-F@ctory」は、工場内で生産情報とITを連携させ、リアルタイムでデータを分析・活用する仕組みです。この仕組みにより、工場内の設備やエッジコンピューティングによる生産情報を活用し、生産性の向上やコスト削減が可能となりました。
また、エンジニアリングチェーンやサプライチェーンとも連携し、工場全体としての生産性を向上させることを目指しています。「e-F@ctory Alliance」の発足によって、技術領域の連携や、ソリューションの提供も進められています。
4.ヤマハ発動機株式会社 「経営目線のデジタル改革実行」
ヤマハ発動機株式会社では、デジタル技術を活用した経営目線でのビジネス改革に取り組んでいます。「既存のビジネスの効率化」と「未来のビジネスの創出」をテーマに、年間数十件のPoC(概念実証)を実施しています。
これにより、スマートファクトリーやデジタルマーケティングの推進、データ分析による業務効率化を行い、グローバルな全体最適を目指した改革を実施しています。また、マーケティング力強化やデジタル改革のリーダー育成にも注力しています。
5.ダイキン工業株式会社 「工場IoTプラットフォーム」
ダイキン工業株式会社では、大阪・堺に新工場「デジタル・ファクトリー」を設立し、工場IoTを活用した生産データの見える化と最適化に取り組んでいます。工場内でのIoTプラットフォームを整備することで、全ての設備をネットワークで繋ぎ、データの統合・分析を行い、生産効率を向上させています。
また、リアルタイムでの課題解決を可能とする「工場IoTプロジェクトセンター」を設置し、メンバーが集まりデータに基づいた議論や判断を行っています。
参照元:製造業DX取組事例集
製造業のDX事例【中堅・中小企業】
6.株式会社山本金属製作所
株式会社山本金属製作所は、大阪府大阪市に本社を置き、機械加工業を営む企業です。同社のDX取り組みは、「機械加工現場にイノベーションを起こす」ことを目指し、精密加工技術、ロボットシステムインテグレーション、センシング制御・計測評価の3つのコア技術を活用しています。
2008年の金融危機で受注が半減した際、同社は待つだけの姿勢から、市場を自ら開拓するビジネスモデルへの転換を図りました。そのため、機械加工のプロセスデータをリアルタイムで計測する仕組みを導入し、現場の見える化を実現しました。また、デジタル推進室が社内の橋渡し役となり、DXの推進を担い、デジタルツインを活用した新たなものづくりにも取り組んでいます。
7.株式会社樋口製作所
株式会社樋口製作所は、岐阜県各務原市に拠点を構え、金属加工を中心に、ブリッジエンジニアによるDXを進めています。同社のブリッジエンジニアチームは、製造現場とIT技術を結びつけ、現場の困りごとを解決することを目的に活動しています。
社内で自社プラットフォーム「Higuchi Data Integration Platform」を構築し、全社でデータを共有・活用することで生産性と品質の向上を図っています。また、Eラーニングを活用して、従業員のスキルアップを支援し、現場主導のアジャイル開発を進めることで、DX推進のスピードと精度を高めています。
8.西機電装株式会社
西機電装株式会社は、愛媛県新居浜市に本社を構える製造業で、大型クレーン等の制御盤設計・製造を手掛けています。DX推進のきっかけは、過去の生産管理システム導入の失敗でした。同社はその失敗を糧に、サイボウズ社のkintoneを活用し、業務効率化を進めました。
製造現場での簡単な操作が可能なIoTデバイスを自社開発し、現場社員の操作負担を軽減しました。また、中小企業向けの業務効率化コンサルティングサービスも展開しており、地域企業と協力してDXを推進しています。
9.株式会社リョーワ
株式会社リョーワ(福岡県北九州市)は、油圧装置のメンテナンス事業を基盤とし、AIを活用した外観検査システムを開発する企業です。油圧メンテナンス事業の将来性を見据え、DXを進めた点が評価されています。
2003年、油圧メンテナンス事業から転換し、AIによる外観検査を軸とする新規事業を立ち上げました。外観検査システム「CLAVI」は、中小企業でも導入可能な低価格のAIソリューションとして注目され、スマートフォンやMR(複合現実)を利用したシステムです。
また、油圧メンテナンスとの相乗効果を狙い、遠隔メンテナンスサービスの開発も進めています。社長のリーダーシップのもと、油圧修理屋からAI企業への変革を推進し、DXにおいて成功を収めています。
10.株式会社NISSYO
株式会社NISSYOは、東京都羽村市に本社を置き、電気機械器具の製造を行う企業です。同社は、20年で売上を10倍にするなど成長を続けており、デジタル化による業務改善に積極的に取り組んでいます。
同社のDXの特徴は、Google Workspaceによる全社共通ポータルサイトの整備や生産性向上のためのデータ活用、バックオフィス業務の最適化にあります。また、経営計画のオープン化や全員参加型の改善活動により、DXを推進する体制を整えています。
製造業のDXを進めるための手順
製造業でDXを成功させるためには、手順に従って計画的に進めることが重要です。ここでは、DX推進のための手順を紹介します。
1.DX推進の目的とゴールを確認する
DXを推進する際には、まず目的とゴールを明確にしましょう。製造業におけるDXの目的は多岐にわたりますが、生産性向上、コスト削減、品質改善、そして新たなビジネスモデルの創出などが主な目的です。これらの目的を明確に設定し、全社員で共有することで、DXに向けた具体的なアクションを取る際の指針となります。
また、達成したいゴールが定まっていれば、プロジェクトの進捗や成果を評価しやすくなり、社員の意識を統一し、全社的な取り組みを促進します。生産性向上において例を挙げると、自動化技術やAIを導入し、工場の生産ラインを効率化することが目的。これにより、作業時間の短縮や生産の高速化を図り、より多くの商品を短期間で生産できることがゴールと言えます。
2.現状分析と課題の特定
DX推進においては、現状の業務プロセスやシステムを分析し、課題を明確にしましょう。例えば、どの工程に無駄が生じているのか、属人化している業務があるか、情報の共有が不足しているかなど、課題を具体的に洗い出します。
現状分析に基づいて、どの分野にDXを導入することで効果が得られるのかを判断することが重要です。課題を正確に特定することで、DX推進の方向性がより明確になります。
3.小さく初めて成功事例を出す
DX推進は、いきなり大規模なプロジェクトを実行するのではなく、小さな取り組みから始めることがポイントです。スモールスタートで効果を確認し、成功事例を積み重ねることで、従業員の理解と協力を得やすくなります。
例えば、部分的な工程の自動化やデータ管理の改善など、短期間で効果が見えるプロジェクトを選びます。成功事例が蓄積されることで、次の大規模なDXプロジェクトへとつなげることができ、組織全体でのDX推進が加速します。
製造業のDXはあおい技研
株式会社あおい技研は、製造業に特化した業務改善コンサルティングを提供し、製造現場のDX推進をサポートします。80以上の製造現場での診断や改善の経験を活かし、お客様に合ったDX戦略を提案します。
データ分析、業務効率化システムの開発、現場のデジタル化などを通じて、お客様の業務改善と生産性向上を支援します。
製造業のDXについては、あおい技研にご相談ください。
まとめ
- 製造業におけるDXは、生産性向上や人手不足の解消に取り組んでいる
- 大企業から中小企業まで、さまざまな成功事例がある
- DX導入の際は、目的設定と現状分析が重要
- スモールスタートで成功事例を積み重ねることが効果的
- DX推進には、弊社(あおい技研)のような専門コンサルティング会社のサポートも有効
製造業のDXはあおい技研
株式会社あおい技研は、製造業に特化した業務改善コンサルティングを提供し、製造現場のDX推進をサポートします。80以上の製造現場での診断や改善の経験を活かし、お客様に合ったDX戦略を提案します。
データ分析、業務効率化システムの開発、現場のデジタル化などを通じて、お客様の業務改善と生産性向上を支援します。
製造業のDXについては、あおい技研にご相談ください。
関連記事
-
製造業のDX推進に役立つツールを徹底解説!DXツールを導入するメリットとは?
2024年10月25日
-
製造業DXの効果的な進め方とは?取り組むメリットや課題を解説
2024年11月28日
-
製造業のDXに求められるデジタル人材とは?
2024年11月28日
-
生産性を上げる方法を2つの視点で解説|製造業での取り組み事例も紹介
2024年5月7日
-
仕事の効率化をするときにやってはいけないこと4つ|大切な考え方
2023年3月20日
-
製造業のDXにコンサルティングは必要?必要性や役割を解説
2024年11月28日
-
業務効率化の事例15選 【製造業の改善ネタ探しに役立つ】
2023年1月25日
-
業務効率化の成功事例7つを参考にアイデア出しをしよう!業務の無駄の見つけ方も解説
2023年12月12日
-
業務改善の手法6つ【経費削減との違いもご解説】
2022年3月8日
カテゴリー
- IT化
- QCD
- QCサークル
- コスト削減
- コンサルタント
- スマートファクトリー
- ボトルネック工程
- 中小企業
- 労働生産性
- 合理化
- 品質担保
- 品質管理
- 在庫管理
- 工場IoT
- 工場効率化
- 工程管理
- 工程管理システム
- 投入資源
- 業務効率
- 業務改善
- 生産ライン
- 生産性向上
- 生産管理
- 生産管理システム
- 経費削減
- 製造業
- 製造業 DX
- 製造業IoT
- 見える化
- 設備管理
新着コラム
-
2025年7月30日
工場の労働環境を改善するための具体策とは?改善のステップや事例もご紹介
-
2025年7月30日
工場の暑さ対策を徹底解説!2025年義務化対応と効果的な対策とは?
-
2025年7月30日
工場の5S活動とは?生産性と安全性を高める改善の進め方
-
2025年6月30日
産業用ロボットとは?サービスロボットとの違いや種類、導入するメリットを解説
-
2025年6月30日
工場の省人化に取り組むメリットを解説!具体的なステップと事例をご紹介
-
2025年6月30日
【産業用ロボット】主要メーカーの市場シェアはどれぐらい?市場規模などわかりやすく解説
-
2025年5月28日
事例から学ぶ工場の安全対策!製造業の労災件数も紹介
-
2025年5月28日
ベンダーコントロールとは?定義やToDoを解説
-
2025年5月28日
外部コンサルタントとは?内部との違いやメリット・デメリット
-
2025年4月25日
勘と経験に頼らないモノづくりとは?製造業10社のデータ活用事例を紹介