工程分析とは?使われる記号や手法、改善ポイントを解説
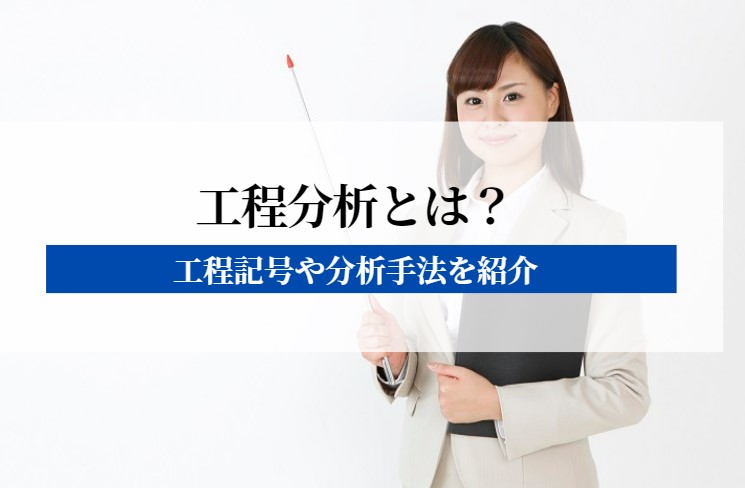
製造業の現場では、生産効率を向上させ、コストを削減し、品質を安定させることが常に求められています。
しかし、実際の生産工程を見てみると、ムダな作業や不要な運搬、滞留、過剰な検査などが原因で、思うように生産性が上がらないことも少なくありません。
そこで重要になるのが「工程分析」です。
工程分析は、生産ラインの各工程を細かく調査し、どの作業が本当に価値を生み出しているのかを明確にしながら、不要な工程を削減する手法。
本記事では、工程分析の基本から、使われる記号、具体的な手法、改善ポイントまでを解説します。
コンテンツ
工程分析とは
製造業において、原材料の投入から製品の完成までの一連の流れを「工程」と呼びます。
この各工程を細かく分析し、ムダを省き、生産効率を最大化するために行われるのが工程分析です。
例として、自動車の製造ラインを考えてみましょう。
部品の加工、組み立て、塗装、検査といった複数の工程が連続して行われますが、その中には不要な運搬や作業の待ち時間、非効率な動作が隠れていることがあります。
工程分析では、こうした「価値を生まない工程」を洗い出し、生産性を向上させるための改善策を導き出します。
工程分析の目的
コスト削減のために無駄な工程を削減する
生産ラインには、製品を加工する「価値を生む工程」と、それ以外の「価値を生まない工程(ムダ)」があります。
例えば、部品を何度も別の作業台に移動させる運搬作業や、作業員の手待ち時間は、直接製品の品質や性能には貢献しません。
工程分析を行うことで、こうした不要な運搬や停滞を削減し、製造コストの削減につなげることができます。
生産効率を向上させる(ボトルネックの特定)
すべての工程がスムーズに流れているわけではなく、特定の作業が遅れることで全体の生産スピードが低下することがあります。
例えば、部品の供給が遅れることで、組み立て作業が止まってしまうといったケースです。
工程分析を通じて 「どの工程で生産が滞りやすいのか」 を明確にし、作業の最適化を図ることができます。
品質管理を強化し、不良品を減らす
製造業では、品質のバラつきを減らし、不良品の発生を最小限に抑えることが求められます。
工程分析によって、どの工程で品質の低下が起きやすいのかを特定し、適切な対策を講じることで、ムダなリワーク(手直し)や廃棄コストを削減できます。
例えば、組み立て前の部品検査を強化することで、不良品がラインの後半に進むのを防ぎ、後工程での手戻りを減らせます。
標準化を進め、属人化を防ぐ
製造現場では熟練工の技術に頼る場面が多くありますが、属人化が進むことで生産の安定性が損なわれるリスクも。
工程分析を活用して作業手順を明確化することで、誰が作業しても同じ品質を保てる「標準化」を推進できます。
例えば、自動車の塗装工程では、塗料の量やスプレーの角度をマニュアル化し、作業者ごとのバラつきを抑える工夫が求められます。
このように工程分析は、単なる「作業の見直し」ではなく、コスト削減・生産性向上・品質強化など、製造業の競争力を高めるために用いられる手法です。
次の章では、工程分析を行う際に使用される記号や手法について具体的に解説していきます。
工程分析で使われる記号
工程分析では、作業の流れを可視化するために「工程記号」が用いられます。
以下の表に示すように、工程には「加工」「運搬」「停滞」「検査」の4種類があり、それぞれ記号が決められています。
加工(○:丸)
加工とは、原材料や部品に変化を加え、製品を形作る工程のことを指します。
例えば、金属板をプレス加工して形状を変えたり、部品を組み立てたりする作業が該当します。
加工は「直接的に付加価値を生む工程」のため、いかに効率的に加工するかが生産性向上のポイントです。
運搬(小さい○ or →:丸 or 矢印)
運搬は、部品や材料を移動させる工程を指します。
例えば、製造ラインの各工程間で部品を搬送する作業や、完成品を倉庫へ移動させる工程などが該当。
運搬自体は直接的に製品の価値を高める工程ではないため、無駄な運搬を減らすことがコスト削減につながります。
そのため、最適なレイアウト設計や工程間の距離短縮などが改善のポイントになります。
停滞
停滞とは、製品や部品が動かずに留まっている状態を指します。
これは生産の流れを阻害する要因の一つであり、無駄なコストや納期遅延の原因となります。
停滞には、以下2つの種類があります。
貯蔵(▽:三角形)
貯蔵は、意図的に製品や部品を保管することを指します。
一定量の在庫を持つことで生産の安定化を図るケースもありますが、過剰な貯蔵は保管コストやスペースのムダにつながるため注意が必要です。
滞留(D:ディー)
滞留は、工程間で製品や部品が無駄に待機している状態を指します。
前工程の処理が遅れているために後工程で作業が進まない場合などがここに該当します。
滞留が発生すると、リードタイムが長くなり、納期の遅延や生産効率の低下を招くため、工程分析によってボトルネックを特定し、スムーズな流れを作ることがポイントです。
検査
検査は、製品や部品の品質を確認する工程です。
不良品が市場に出るのを防ぐため、適切な検査を行うことが求められますが、過剰な検査はコスト増や生産遅延につながるため、効率的に実施する必要があります。
検査には、主に2つの種類があります。
数量検査(□:四角形)
数量検査は、生産数が計画通りか、部品の数に不足がないかを確認する工程です。
例えば、部品の数をカウント、製品のセット数チェックなどがここに当たります。
品質検査(◇:ダイヤ)
品質検査は、製品が規格通りに仕上がっているか、欠陥がないかをチェックする工程です。
例としては寸法検査、外観検査、機能テストなどがあります。
検査工程は品質向上のために不可欠ですが、不必要な検査を減らし、自動検査装置やIoT技術を活用することで効率化を図ることもポイントになります。
工程分析の手法
単純工程分析
単純工程分析とは、製品の生産工程全体の流れを把握し、作業の種類や回数を可視化する手法です。
工程全体をシンプルに整理し、ムダな作業や不要な運搬がないかをチェックします。
生産工程の全体像を「見える化」するのに適しているため、最初の分析として活用されます。
【分析例】
・自動車部品の生産ライン全体を把握する
・食品製造の各工程(材料投入→加熱→包装)の流れを整理する
詳細工程分析
詳細工程分析は、単純工程分析をさらに掘り下げ、特定の作業や工程に焦点を当てて分析する手法です。
製品工程分析と作業者工程分析の2つに分かれます。
製品工程分析
製品が生産される過程を詳細に記録し、加工・運搬・検査などの割合を分析する手法です。
「どの工程でどれだけの時間を使っているのか?」を明確にすることで、ムダな工程を削減できます。
【分析例】
・電子部品の組み立て工程の分析(どの作業に時間がかかっているかを可視化)
・食品加工ラインの最適化(包装工程の停滞を解消)
作業者工程分析
作業者の動作に着目し、効率よく作業できているかを分析する手法です。
作業者の動きを記録し、手待ち時間の削減や動作のムダを発見することが目的です。
【分析例】
・工場のライン作業員の動作を分析し、不要な移動を減らす
・製品の組み立て作業において、手作業の最適な順番を決める
運搬経路分析(流れ線図)
運搬経路分析とは、工場内での部品や製品の移動経路を図示し、ムダな運搬を減らすための手法です。
「流れ線図」とも呼ばれ、生産ラインのレイアウト改善に活用されます。
【分析例】
・工場内の運搬経路を最適化し、ムダな移動を削減
・材料や製品の移動時間を短縮し、作業効率を向上
連合作業分析
連合作業分析とは、2人以上の作業者が共同で行う作業を分析し、効率化を図る手法です。
特に、作業員の役割分担や動作の重複をなくし、連携の最適化を目指します。
【分析例】
・自動車の組み立てラインで、作業者の動きを最適化
・食品工場でのライン作業を効率化し、生産スピードを向上
工程分析の流れ
目的を決める
まず、工程分析を行う目的を明確にすることが重要です。
ここが曖昧なまま分析を進めると、改善の方向性が見えず、適切な対策を打ち出せません。
目的が明確になることでどの分析手法を用いるかが決まり、具体的な改善策につなげやすくなります。
【目的の例】
・生産コストを削減したい(不要な工程を減らす、作業時間を短縮する)
・生産スピードを向上させたい(ボトルネックを解消し、流れをスムーズにする)
・品質を向上させたい(不良品の発生を抑える、検査工程を最適化する)
分析対象を決める
次に、どの製品・工程を対象に分析するのかを決定します。
すべての工程を一度に分析するのは難しいため、特に改善が必要な部分に絞って分析することが効果的です。
【分析対象の例】
・特定の製品ライン(新製品の生産ラインの効率を高めたい)
・生産効率の低い工程(組み立てラインのボトルネックを解消したい)
・不良品が発生しやすい工程(品質検査で弾かれる割合が高い工程を見直したい)
工程を分類する
次に、対象となる工程を「加工」「運搬」「停滞」「検査」などのカテゴリに分類します。
この分類を基に、どの工程にムダが多いのかを見極め、改善の方向性を明確にします。
【工程分類の例】
・加工:切削、溶接、組み立て
・運搬:コンベア搬送、フォークリフト移動
・停滞:在庫保管、前工程待ち
・検査:外観検査、寸法測定
時間や距離などを調査する
次に、各工程の詳細なデータを収集します。
特に「時間」と「距離」は、生産性に大きく影響を与えるため、しっかりと計測することが重要です。
例えば「組み立て作業に10分かかるが、そのうち3分は部品の受け渡しで使われている」と分かれば、部品の配置を変えるだけで作業時間を短縮できる可能性があります。
【調査の例】
・作業時間の測定(各工程にどれくらいの時間がかかっているか)
・移動距離の測定(部品や作業者の移動距離が長すぎないか)
・待機時間の測定(作業者や部品がどのくらい停滞しているか)
改善点を見つける
最後に、収集したデータをもとに、生産効率を向上させるための改善策を検討します。
このとき、重要なのは「加工以外の工程を減らす」ことです。
このポイントについては次で詳しく説明します。
【改善点の例】
・運搬距離が長い → 作業エリアを近づける
・滞留時間が長い → 前工程のスピードを上げる
・検査の手間が増えている → 不良の発生源を改善する
工程分析の改善ポイント
付加価値を生むのは加工だけ
工程分析の改善を考える際、「付加価値を生み出す工程」と「付加価値を生まない工程」に分ける考え方が重要です。
「加工」「運搬」「停滞」「検査」といった工程がありますが、直接的に製品の価値を生み出しているのは「加工」だけ。
・加工工程(付加価値を生む) → 原材料や部品に手を加え、製品を完成させる
・それ以外の工程(付加価値を生まない) → 運搬・停滞・検査は、製品の品質や機能に直接的には影響しない
つまり、運搬や停滞、検査に時間をかけるほど、「製造コストは増えるのに、製品の価値は変わらない」という非効率な状態になるのです。
だからこそ、いかに「加工工程」に集中し、その他の工程を減らせるかが工程分析のポイントです。
加工以外の工程をどのように最適化するか
運搬を減らす
製造現場では部品や材料が頻繁に移動しますが、運搬そのものには付加価値がありません。
そのため、「いかに運搬の回数や距離を減らすか?」が、生産性向上のポイントとなります。
このようなムダをなくすためには、作業エリアのレイアウトを最適化し、部品や工具を必要な場所に近づけることが大切です。
【改善策の例】
・作業台の近くに部品や工具を配置し、取りに行く手間を減らす
・工場のレイアウトを見直し、運搬距離を短縮する
・自動搬送機(AGV)やコンベアを導入し、手作業での運搬を最小化する
停滞を減らす
停滞とは、部品や製品が工程の間で待機している状態のことを指します。
生産の流れがスムーズでないと、部品や製品が「滞留」し、納期の遅れや作業の非効率につながります。
このような「滞留時間」を削減するためには、生産計画や作業の流れを調整し、工程間のギャップをなくすことが必要です。
【改善策の例】
・ボトルネック工程の改善(作業者の配置変更や自動化による処理能力向上)
・ジャストインタイム生産の導入(必要な部品を必要なタイミングで供給し、過剰在庫を持たない)
・生産スケジュールの最適化(前工程と後工程のスムーズな連携を確保する)
検査の無駄を減らす
品質管理のための検査は重要な工程ですが、検査自体は製品の価値を高めるわけではありません。
むしろ、不良品の発生を減らして「そもそも検査が不要な状態を作る」ことが理想的な改善方法と言えます。
例えば、「最終検査で大量の不良品が発見される」場合、それは製造プロセスのどこかに問題があるということ。
検査に頼るのではなく、製造の早い段階で品質を確保し、不良の発生自体を防ぐ仕組みを作ることが重要になってきます。
【改善策の例】
・製造プロセスを改善し、不良品を減らす(設備の精度向上や作業手順の見直し)
・自動検査装置を導入し、必要な検査のみ行う(目視検査の負担を軽減)
・作業者への教育を強化し、ミスを減らす(標準作業手順の確立)
まとめ
工程分析は、生産現場のムダを洗い出し、効率的な生産体制を実現するために欠かせない手法のひとつ。
特に「加工」以外の工程(運搬・停滞・検査)を最適化し、いかに付加価値を生む作業に集中できるかが重要です。
【工程分析のポイント】
★ 運搬を減らす → 工場レイアウトを見直し、不要な移動を削減
★ 停滞をなくす → 生産計画を最適化し、工程間の流れをスムーズにする
★ 検査の無駄を減らす → 品質を上流で作り込み、不良品の発生を抑える
これらの改善策を実施することで、生産コストの削減・納期短縮・品質向上といったメリットが得られます。
「自社だけでは分析が難しい」「レイアウト配置を相談したい」そんなお悩みをお持ちの方は、製造業専門のコンサルタント「あおい技研」へご相談ください。
製造業のDXはあおい技研
株式会社あおい技研は、製造業に特化した業務改善コンサルティングを提供し、製造現場のDX推進をサポートします。80以上の製造現場での診断や改善の経験を活かし、お客様に合ったDX戦略を提案します。
データ分析、業務効率化システムの開発、現場のデジタル化などを通じて、お客様の業務改善と生産性向上を支援します。
製造業のDXについては、あおい技研にご相談ください。
関連記事
-
カイゼンは時代遅れ?トヨタ式の基本や進め方・具体例3つを紹介
2022年7月19日
-
製造業で検査を効率化する方法4つ!目視検査の見逃し対策法も併せて紹介
2024年8月15日
-
工場の稼働率を上げるには?有効な方法3つと計算式の求め方や目安を解説
2023年10月13日
-
工程管理システム導入で期待できる2つのこと|工程管理の基本と主な機能
2022年1月17日
-
業務改善の手法6つ【経費削減との違いもご解説】
2022年3月8日
-
生産管理とは?7つの業務内容と向いている人の特徴
2022年3月3日
-
工程管理の基本を3つの項目で徹底解説【工程管理表の作成方法も】
2022年3月28日
-
合理化とは?製造業における意味と効率化との違い・事例3つをご紹介
2022年6月15日
-
DXで業務効率化できる理由4つを徹底解説|製造業での事例
2022年4月28日
カテゴリー
- IT化
- QCD
- QCサークル
- コスト削減
- コンサルタント
- スマートファクトリー
- ボトルネック工程
- 中小企業
- 労働生産性
- 合理化
- 品質担保
- 品質管理
- 在庫管理
- 工場IoT
- 工場効率化
- 工程管理
- 工程管理システム
- 投入資源
- 業務効率
- 業務改善
- 生産ライン
- 生産性向上
- 生産管理
- 生産管理システム
- 経費削減
- 製造業
- 製造業 DX
- 製造業IoT
- 見える化
- 設備管理
新着コラム
-
2025年7月30日
工場の労働環境を改善するための具体策とは?改善のステップや事例もご紹介
-
2025年7月30日
工場の暑さ対策を徹底解説!2025年義務化対応と効果的な対策とは?
-
2025年7月30日
工場の5S活動とは?生産性と安全性を高める改善の進め方
-
2025年6月30日
産業用ロボットとは?サービスロボットとの違いや種類、導入するメリットを解説
-
2025年6月30日
工場の省人化に取り組むメリットを解説!具体的なステップと事例をご紹介
-
2025年6月30日
【産業用ロボット】主要メーカーの市場シェアはどれぐらい?市場規模などわかりやすく解説
-
2025年5月28日
事例から学ぶ工場の安全対策!製造業の労災件数も紹介
-
2025年5月28日
ベンダーコントロールとは?定義やToDoを解説
-
2025年5月28日
外部コンサルタントとは?内部との違いやメリット・デメリット
-
2025年4月25日
勘と経験に頼らないモノづくりとは?製造業10社のデータ活用事例を紹介