データ分析で製造業の何が変わる?つまずくポイントも解説
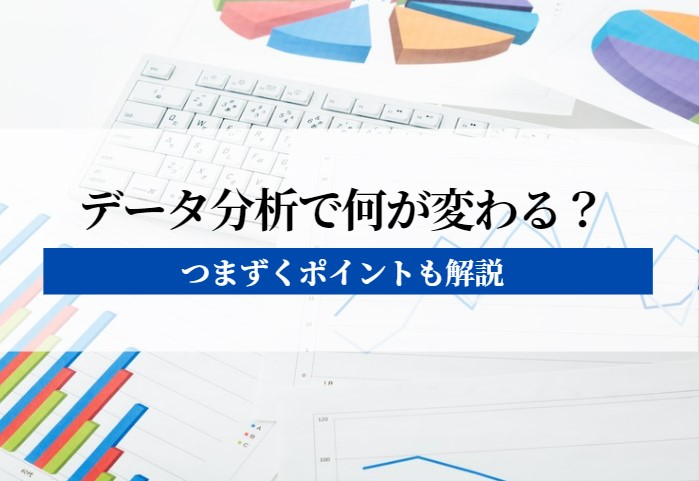
世界的な競争がますます激化する中で、日本の製造業は「高品質・高付加価値」を武器に戦ってきました。
しかし近年では、多品種少量生産や人材不足など、従来のやり方だけでは解決が難しい課題が増えています。
そこで注目されているのが「データ分析」を活用した現場改善です。
日々の生産ラインデータや品質情報、在庫の動きなど、現場には多くの数値・情報が眠っています。
それらを集めて見える化し、どんな工程がボトルネックなのか、不良を減らすにはどこを改善すればいいのか、といった問題の解決策を導き出せるのが、データ分析の最大の強み。
本記事では、製造業のデータ分析がもたらす変化や必要性、つまずきやすいポイントを解説します。
コンテンツ
製造業におけるデータ分析とは?
「データ分析」と聞くと、AIや統計ソフトを駆使して膨大な数字を読み解くイメージを持たれるかもしれません。
しかし製造業におけるデータ分析の本質は、生産現場に存在する数値・情報をうまく活用し、現場の課題を解決することです。
例えば、以下のような日々記録されるデータを集め、そこから生まれた傾向や問題点を“見える化”し、改善策を示すのが「製造業におけるデータ分析」の役割です。
・生産ラインデータ:どこで作業が遅れているか、どの工程が無駄か発見できる
・品質データ:不良品が出る原因を特定し、減らせる
・設備データ:機械の故障を事前に予測して、トラブルを未然に防げる
・在庫データ:部品の不足や余りを防ぎ、無駄なコストを削減できる
ここでの分析とは、単にエクセルで数値を管理するだけでなく「今、どこがボトルネックなのか?」「どんな対策で収益を伸ばせるか?」を数字から読み解くところまでを含みます。
なぜ製造業にデータ分析が必要なのか?
日本のものづくりは、職人の技と現場の経験を武器に、世界的にも高い品質を維持してきました。
しかし、近年は人材不足や多品種少量生産の広がり、国際的な価格競争など、技術力だけでは乗り越えづらい課題が多様化しています。
そうした背景から、データに基づいて問題点を洗い出し、組織的に改善を進めるやり方が急速に注目されるようになりました。
現場任せにしていた不良発生の傾向や需要予測のばらつきなどを、数字や事実に基づいて把握できるようになれば、意思決定のスピードと正確性が格段に高まると期待されているのです。
また、余剰在庫を削減したり、不具合が起きやすい工程を最小限に抑えることで、コスト面や納期面の課題を解決できる可能性も広がります。
「設備投資がどれくらい必要なのか」「専門家を雇わないと成功しないのではないか」といった不安はあるかもしれません。
しかし、重要なのはまず自社が抱える問題に対して数値的な裏付けをとり、具体的な対策へ落とし込むための第一歩を踏み出すことだと言えます。
データ分析で現場の「何」が変わる?
不良率が減り、品質が安定する
データ分析を導入すると、不良品を生み出している工程を客観的に把握できるようになります。
温度や湿度などの製造環境が品質に影響しているケースや、ラインのスピードが速すぎて正確な作業ができていないケースなど、これまでは作業者の経験や勘に頼っていた部分がデータとして明確化します。
生産効率が上がり、ムダが削減される
データ分析を活用すると、ライン全体の稼働状況が「見える化」されるため、どこで時間のロスが発生しているかが明確になります。
以下のような “見えないムダ”をあぶり出すことで、生産プロセスの最適化を進められるのです。
・必要以上に稼働している設備 → 電力や人手のムダ
・待機時間が長すぎる工程 → ボトルネックの特定
需要予測が精度アップし、在庫が適正化する
これまでの「現場担当の経験による受注見込み」ではなく、過去の販売実績や季節変動、時期ごとの需要トレンドなどを統計モデルやAIで予測することで、精度の高い受注計画が立てられます。
受注数や販売実績をデータベース化し、統計的な手法やAIを使って需要を予測すれば、在庫リスクを減らしつつ欠品も防げるようになります。
データ分析でつまずく4つのポイントと解決策
① データはあるが「活用方法」がわからない
製造現場では、IoTやセンサーで多くのデータが取れるようになっていますが、「集めたデータをどう使えばいいの?」という悩みを抱える企業が多いです。
その原因は「何を解決したいのか」が明確になっていないから。
まず必要なのは、データを使って「何を改善したいのか?」という目的をはっきりさせることです。
目的がはっきりすれば、どのデータを見るべきかが明確になります。
「不良品を減らすためには?」など、具体的な目的を1つに絞ることから始めてみましょう。
★Point
活用方法がわからない → 何を解決したいのか?目的を明確にする
② 経営層と現場の目的がズレている
先ほど目的を明確にすることが大切と述べましたが、経営層と現場の目的を一致させることも大切です。
経営層は「生産性向上」、現場は「日々の負担を減らしたい」など、それぞれ目的が違う場合、データ分析が空回りしてしまいます。
これを解決するには、経営層と現場で「同じ目的」を共有すること。
経営側が現場と直接話し合い、「本当に困っていること」を理解した上で、双方が納得する共通の目的を決めるようにしましょう。
こうすることで、「データ分析は自分たちに役立つ」と現場も納得して協力しやすくなります。
★Point
経営層と現場の目的がズレている→ 話し合って、双方が納得する共通の目的を設定する
③ 分析ツールが難しくて現場が使いこなせない
多機能な分析ツールを導入したものの、複雑すぎて現場の担当者が使いこなせないケースもよくあります。
使えないツールは結果的に放置され、結局データ分析が進まない原因になります。
解決策としては、最初から高性能で複雑なツールを選ぶのではなく、現場が日常的に使えるようなシンプルなツールを選ぶのがおすすめ。
また、ツールを導入する前に実際の使い心地を一緒に確認して、研修やマニュアルなどのサポートを充実させることもフォローとして大切です。
★Point
分析ツールが難しくて現場が使いこなせない → 担当者が使いやすいツール&研修でのフォロー
④ 分析結果を現場改善に結びつけられない
データ分析の結果を出しても、それを現場の改善行動に結びつけられないという課題も多くあります。
分析結果が現場に反映されなければ、データを集めた意味がありません。
解決するためには、「分析結果を現場の具体的なアクションに落とし込む」までを徹底すること。
分析担当者と現場担当者が定期的に話し合い、「この結果から具体的にどんな行動ができるか?」を明確にしましょう。
現場で小さな改善を行いながら効果を見て、成功体験を積み重ねていけば、データ分析のありがたさを分かってもらえるはずです。
★Point
分析結果を現場改善に結びつけられない → 現場の具体的な「アクション」に落とし込むには?まで考える
製造業におけるデータ分析事例
富士電機株式会社
富士電機の山梨工場では、生産工程におけるエネルギー使用量の削減を目的に、データ活用を推進。
電力や温度などのデータをセンサーで収集、解析ソフトウェアを活用して「見える化」を実施しました。
可視化したデータを多方面から分析して、エネルギーが非効率な点を特定。
また、AIによる需要予測を取り入れることで、エネルギーコストを最小限に抑える運転パターンを計画しました。
こうした取り組みの結果、生産量が増加する中でも5年間で34%の省エネを達成し、エネルギー自給率100%を実現しています。
※参照元:富士電機株式会社┃半導体分野向けEMSソリューション
三菱電機株式会社
三菱電機では工場の自動化を支えるFA機器について、機器同士のデータ連携が不十分で生産性向上やコスト削減の課題がありました。
この問題に対して、FA機器とITシステムを連携する「e-F@ctory」を開発。
生産現場のデータをリアルタイムで収集・分析し、より適切な制御を行う仕組みを構築しました。
データ活用により生産効率が向上し、より技術連携を強化する体制も整備。
生産現場の情報だけでなく、CADデータなどのエンジニアリングチェーンとの連携も可能になりました。
※参照元:経済産業省┃製造業DX取組事例集┃PDF31ページ
まとめ
製造業におけるデータ分析は、単なる「数値の管理」ではなく、品質の向上や生産性の改善、コスト削減といった実務的な成果につながるものです。
まずは「どの課題を解決したいのか」をはっきりさせ、現場を巻き込みながら具体的な行動へ落とし込むことが大切。
そもそも、どのように課題を特定したら良いのか?とお悩みの場合は、製造業専門のコンサルタント「あおい技研」へご相談ください。
製造業のDXはあおい技研
株式会社あおい技研は、製造業に特化した業務改善コンサルティングを提供し、製造現場のDX推進をサポートします。80以上の製造現場での診断や改善の経験を活かし、お客様に合ったDX戦略を提案します。
データ分析、業務効率化システムの開発、現場のデジタル化などを通じて、お客様の業務改善と生産性向上を支援します。
製造業のDXについては、あおい技研にご相談ください。
関連記事
-
在庫管理をバーコードでするメリット3つ!デメリットやエクセルで自作する方法も解説
2023年11月6日
-
QCサークル活動の進め方|4つの基本要素と成功させるポイント
2021年12月24日
-
工場を見える化する目的とメリット4つ!具体的な方法や事例・課題も解説
2022年7月1日
-
製造業の見える化とは?意味と目指すメリット・実行する方法・事例をご紹介
2021年10月20日
-
作業性を向上できる取り組み4つ|製造業における成功事例も紹介
2022年11月28日
-
作業の効率化が進まない理由5つ!製造業における向上の事例も紹介
2023年9月12日
-
7つのムダを初心者向けに徹底解説|それぞれの対処法や改善事例も紹介
2024年4月5日
-
勘と経験に頼らないモノづくりとは?製造業10社のデータ活用事例を紹介
2025年4月25日
-
業務改善の方法を6ステップでご紹介|具体例やフレームワークも
2022年2月7日
カテゴリー
- IT化
- QCD
- QCサークル
- コスト削減
- コンサルタント
- スマートファクトリー
- ボトルネック工程
- 中小企業
- 労働生産性
- 合理化
- 品質担保
- 品質管理
- 在庫管理
- 工場IoT
- 工場効率化
- 工程管理
- 工程管理システム
- 投入資源
- 業務効率
- 業務改善
- 生産ライン
- 生産性向上
- 生産管理
- 生産管理システム
- 経費削減
- 製造業
- 製造業 DX
- 製造業IoT
- 見える化
- 設備管理
新着コラム
-
2025年7月30日
工場の労働環境を改善するための具体策とは?改善のステップや事例もご紹介
-
2025年7月30日
工場の暑さ対策を徹底解説!2025年義務化対応と効果的な対策とは?
-
2025年7月30日
工場の5S活動とは?生産性と安全性を高める改善の進め方
-
2025年6月30日
産業用ロボットとは?サービスロボットとの違いや種類、導入するメリットを解説
-
2025年6月30日
工場の省人化に取り組むメリットを解説!具体的なステップと事例をご紹介
-
2025年6月30日
【産業用ロボット】主要メーカーの市場シェアはどれぐらい?市場規模などわかりやすく解説
-
2025年5月28日
事例から学ぶ工場の安全対策!製造業の労災件数も紹介
-
2025年5月28日
ベンダーコントロールとは?定義やToDoを解説
-
2025年5月28日
外部コンサルタントとは?内部との違いやメリット・デメリット
-
2025年4月25日
勘と経験に頼らないモノづくりとは?製造業10社のデータ活用事例を紹介