カイゼンは時代遅れ?トヨタ式の基本や進め方・具体例3つを紹介
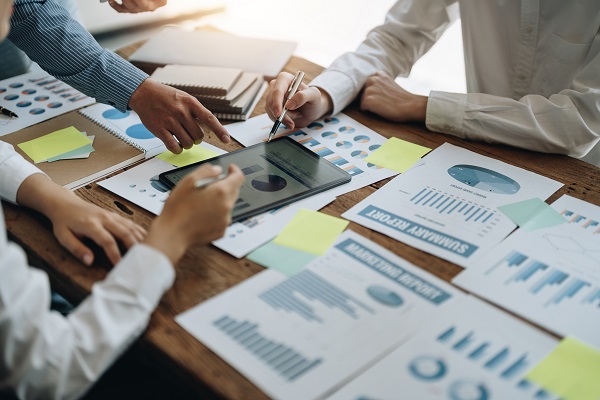
カイゼンとは、製造業の現場における業務を見直し、作業効率や安全性向上を目指す活動のことです。日本初の取り組みですが、海外でも“Kaizen”として高い認知度を誇っています。世界中の製造業のアップデートに貢献してきたカイゼンですが、近年では、
- 「カイゼンは時代遅れだ」
- 「カイゼンは古いし意味がない」
という声も挙がっています。果たして、カイゼンは時代遅れな取り組みなのでしょうか?今回は、初心者に向けてカイゼンの基本について解説します。トヨタ式カイゼンの事例、進め方や製造業での具体例も紹介するため、ご参考にしてください。
コンテンツ
カイゼンとは
カイゼンは「改善」のことですが、なぜカタカナ表記で区別しているのか、気になりますよね。「改善」には、悪い部分を改めて良くするという意味があります。明確になっている問題や課題点を、解消することが目的です。
一方で「カイゼン」には、現状に満足せず、今よりもっと良くするという意味があります。悪い部分だけに着目するのではなく、現状を良くするためにはどうしたらいいか、現状を見据えて対策していく、積極的な活動のことを指します。
以前はカイゼンは主に製造業の現場で採用されてきましたが、現在では建設業、サービス業、小売業など、幅広い業界で活用されています。実際にカイゼンは、時代遅れで古い活動では決してありません。むしろ、これからの時代に業界を問わず必要となる、意義の大きな取り組みになります。
トヨタ式カイゼンの事例
カイゼンが誕生した背景には、トヨタ自動車の取り組みがあります。トヨタ式カイゼンと呼ばれる有名なカイゼン活動では、生産現場のムダを徹底的に排除できるよう、分析して実行することに重きが置かれています。作業を効率化しながら、過剰在庫を抱えないよう努力し、生産性を高めることが目的です。トヨタ式カイゼンの具体的な内容と事例を紹介します。
レベルによる現状把握
トヨタ式カイゼンでは、「あるべき姿」として以下の3つのレベルを提示しています。
- レベル1…標準がある状態
- レベル2…標準通りにできる状態
- レベル3…常に標準が進化している状態
レベル1は、生産現場における理想の作業手順や明確な目標が、標準としてある状態のことを指します。目的達成はできていないが、目指すべきところはしっかりとわかっているという状態です。
レベル2は、標準通りに目標を達成できている状態のことです。
しかし、目標達成している状態を維持し続けるだけでは、以後の発展は見込めません。
レベル3では、目標達成できている状態を維持するだけでなく、更なる発展のために、標準を進化させられる状況にあることが求められます。
現場と標準の状態を常に把握・共有しながら、新たな改善案や目標の設定ができる状態です。
トヨタ式カイゼンは、まずは自分たちがどのレベルにいるのか、把握することから始まります。
組織であることの意識
トヨタ式カイゼンでは、組織やチームであることの意識を高めることを推奨しています。企業は、人を中心とした組織です。特に製造業の現場では、従業員のチームワークが生産性に大きく関係します。従業員が同じ目標に向かって、高いモチベーションを持つことができれば、自然とチームワークは良くなり当然、業務効率は向上します。
トヨタ式カイゼンでは、組織やチームであることの意識を高めるために、特に経営層と従業員同士のコミュニケーションを重視しています。経営層は現場の状況や問題点を理解し、企業の目標をしっかり従業員に伝えることが大切です。従業員も経営層に対して、現場の問題点や改善案、要望などを臆せず伝えられる良好な職場環境が理想的であり、目指すところとなります。
3Mを削減する
3Mとは、現場に潜むムリ・ムダ・ムラのことを指します。ムリとは、特定の人や工程に、能力以上の負担をかけることです。能力以上に負担をかけると、短期的には作業効率が上がっているようでも、いつか必ず歪みが生じます。
結果的に機械の故障やエラー、ヒューマンエラーの多発や事故の発生など、取り返しがつかない労災に発展することもあります。ムダは、付加価値を生まない非効率な作業のことです。ルーティーンワークの中で惰性化してしまっている作業や、古い慣習に基づく業務などが挙げられます。これらは生産性を大きく低下させている要因の一つです。
ムラは、業務にバラつきが生じることにより、工程時間や品質にもバラつきが発生してしまうことです。人員配置や生産計画に問題があることが、主な要因となっています。トヨタ式カイゼンでは、この3Mの削減に力を入れています。3Mは日常業務の中に生じやすい特徴があり、生産性向上を阻むものとして、特に大きなウエイトを占めています。
つまり、3Mの削減が実現すれば、自然と生産性は格段に向上するということです。具体的には、業務負担の軽減、スピードアップ、コスト削減、品質の安定などのメリットがあります。
5Sを大切にする
5Sとは、職場環境を整えるための以下の5つの要素を指します。
- 整理(Seiri)…不要なものを捨てること
- 整頓(Seiton)…使いやすいように整理すること
- 清掃(Seisou)…掃除をすること
- 清潔(Seiketsu)…きれいな状態を維持すること
- しつけ(Shitsuke)…習慣付くようにルール化すること
複数の従業員が作業し、多くの工程が入り組む製造業の現場では、特に5Sの徹底が業務効率化に大きく貢献します。5Sが徹底された現場では、工具や部品がどこにあるのか明確であるため、探す手間が省かれ、効率化が進みます。5Sが出来ていない雑多な環境では思わぬ事故が起きやすくなりますが、清掃の行き届いたクリアな現場では、労災のリスクも低下します。基本的な項目ですが、意外とできていない現場は多いため、5Sを大切にすると効率的で、安全で、快適な職場環境が実現します。
カイゼンの進め方
カイゼンを進めるには、基本的な手順があります。改善策を実行する前に、本質的な問題や課題を洗い出すことも大切です。ここではカイゼンの進め方を解説したいと思います。
問題や課題を洗い出す
まずは、カイゼン活動の対象となる問題や課題を洗い出します。現状把握を行いながら、具体的な問題や課題を浮き彫りにしましょう。問題や課題を洗い出すときは、普段不便に感じていることや、危険性のある作業などに着目すると、発見しやすくなります。特定の問題や課題を改善することで得られるメリットまでイメージできると、カイゼン活動のモチベーションも高まります。
改善アイディアを出す
問題や課題が明確になったら、具体的な改善アイディアを考えます。
- 人員配置と構成を見直す
- 作業手順の順番を変更する
- マニュアルをペーパーレス化する
など、すぐに実行できそうなアイディアを考えるのがポイントです。多大な労力やコストがかかる改善アイディアは、実行と達成までに時間がかかってしまいます。カイゼンを成功させるコツは、すぐに取り組めて結果が出るような、まずは小さな改善活動を意識することです。
また、カイゼンの重要ポイントである「悪い部分だけに着目するのではなく、現状を良くするためにはどうしたらいいか」も合わせて考えることが大切です。
・省人化できそうな業務はないか
・作業時間を短縮するにはどうしたらいいか
などを考え、積極的に改善アイディアを打ち出していきましょう。
実行しながら評価をする
改善アイディアを元に、実際にカイゼン活動を実行していきます。大切なのは、実行の結果や過程を、具体的な数値で評価することです。カイゼンの評価には、各種データの整理や関係性の分析に役立つ代表的な手法である「QC7つ道具」や、複数の項目の結果を視覚的に表せる「レーダーチャート」の活用がおすすめです。主観的かつ曖昧に結果を評価するのではなく、数値データとして成果を表すことが、カイゼンのPDCAサイクルを回していくためにも重要になります。
製造業でのカイゼンの具体例3つ
現代でも多くの製造業の現場で、カイゼンが取り入れられ役立っています。カイゼンを導入するためには、具体例を知っておくことが大切です。ここでは製造業でのカイゼンの具体例3つを紹介します。
1.作業工程を見える化
生産現場の作業工程は、とても複雑です。トラブルが発生したときに、連携や対処をスムーズにするためには、作業工程の見える化が重要になります。作業工程の見える化は、タブレットやホワイトボードの活用で比較的簡単に実現します。
生産管理システムを導入し、生産ラインを可視化する方法もあります。
作業工程が見える化すると、問題やトラブルの発生をリアルタイムで把握・対応できるようになることが最大のメリットです。各工程の作業内容や進捗もわかるようになるため、チームワークが取りやすく、職場環境も向上します。
2.定型業務をシステム化
製造業の現場では、多くの定型業務が存在しています。定型業務は、積み重なると膨大な労力と時間を、捧げていることがわかります。カイゼンでは、まず定型業務が本当に必要なのかを考えます。その結果、必要と判断した定型業務は、定型業務のやり方にムダがないかを考え、省人化や自動化できないか検討してみましょう。
FAXを廃止して自動メール返信機能を導入したり、手動で行っていた受注発注作業をツールで自動化したり、最近では特にITを積極的に活用するのがおすすめです。
3.道具を追加し作業時間を短縮
カイゼンでは基本的に不要なものを取り除いていく作業が注目されますが、逆に追加によって問題が改善されることもあります。
例えば、とある企業は生産現場に電子天秤はかりを取り入れ、製品の数量ではなく重量を計ることで、数えるという無駄な時間の削減に成功しました。ムダをカットしていく作業や姿勢は大切ですが、新たなものを導入することで得られる成果もあります。あらゆる項目の削減にこだわると、必要なものまで失ってしまい、かえって生産性が低下してしまうこともあります。カイゼンに取り組むときは柔軟な考え方で、どうすれば今より良くなるかを検討しましょう。
カイゼンは時代遅れな取り組みではない(まとめ)
カイゼンは日本の製造業の現場で、古くから取り組まれてきました。本質的な内容ではあるものの、基本的な項目が多く、「カイゼンは時代遅れ」「カイゼンなんて意味がない」と言われることもあります。
しかし、日本のトヨタ自動車から誕生したトヨタ式カイゼンは、現在も世界中で広まって認知されています。製造業の現場でしか採用されていなかったカイゼンも、今では建設業やサービス業など、幅広い業界で活用され始めています。カイゼンは、決して時代遅れで古い、意味のない取り組みではありません。業界を問わず、企業の発展に大きく貢献する意義のある活動です。
今日のポイント
- カイゼンとは製造業の現場における業務を見直し、作業効率や安全性向上を目指す活動のこと
- トヨタ式カイゼンではレベルによる現状把握、組織であることの意識、3Mの削減、5Sの徹底が重要視されている
- カイゼンは問題や課題の洗い出し→改善アイディアを出す→実行しながら評価の手順で進める
製造業のDXはあおい技研
株式会社あおい技研は、製造業に特化した業務改善コンサルティングを提供し、製造現場のDX推進をサポートします。80以上の製造現場での診断や改善の経験を活かし、お客様に合ったDX戦略を提案します。
データ分析、業務効率化システムの開発、現場のデジタル化などを通じて、お客様の業務改善と生産性向上を支援します。
製造業のDXについては、あおい技研にご相談ください。
関連記事
-
工場の動線を安全に確保するための手順を3ステップで紹介!レイアウト図の書き方も
2023年8月4日
-
作業の効率化が進まない理由5つ!製造業における向上の事例も紹介
2023年9月12日
-
製造業の人手不足の解決策4つ|若者離れの理由や対策も併せて解説
2024年5月7日
-
業務の効率化の具体例5つ!成功事例も併せて紹介
2024年7月9日
-
業務改善で原因分析をする手法4つ|役立つフレームワークも紹介
2024年1月15日
-
業務効率化の事例15選 【製造業の改善ネタ探しに役立つ】
2023年1月25日
-
労働生産性とは?計算式や向上させるメリット3つをわかりやすく解説
2022年9月29日
-
生産工学とは?初心者向けに3つのポイントで徹底解説|日本大学生産工学部で学べることも紹介
2024年2月20日
-
効率化とは?4つのポイントで初心者向けに基本を徹底解説!
2023年2月27日
カテゴリー
- IT化
- QCD
- QCサークル
- コスト削減
- コンサルタント
- スマートファクトリー
- ボトルネック工程
- 中小企業
- 労働生産性
- 合理化
- 品質担保
- 品質管理
- 在庫管理
- 工場IoT
- 工場効率化
- 工程管理
- 工程管理システム
- 投入資源
- 業務効率
- 業務改善
- 生産ライン
- 生産性向上
- 生産管理
- 生産管理システム
- 経費削減
- 製造業
- 製造業 DX
- 製造業IoT
- 見える化
- 設備管理
新着コラム
-
2025年8月27日
HACCP 7原則12手順で守る「食の安全」!
-
2025年8月27日
GMP認定で支える「安全性」!製造の信頼は工程から始まる
-
2025年7月30日
工場の労働環境を改善するための具体策とは?改善のステップや事例もご紹介
-
2025年7月30日
工場の暑さ対策を徹底解説!2025年義務化対応と効果的な対策とは?
-
2025年7月30日
工場の5S活動とは?生産性と安全性を高める改善の進め方
-
2025年6月30日
産業用ロボットとは?サービスロボットとの違いや種類、導入するメリットを解説
-
2025年6月30日
工場の省人化に取り組むメリットを解説!具体的なステップと事例をご紹介
-
2025年6月30日
【産業用ロボット】主要メーカーの市場シェアはどれぐらい?市場規模などわかりやすく解説
-
2025年5月28日
事例から学ぶ工場の安全対策!製造業の労災件数も紹介
-
2025年5月28日
ベンダーコントロールとは?定義やToDoを解説